Continuous Vibration Monitoring: Principles & Applications
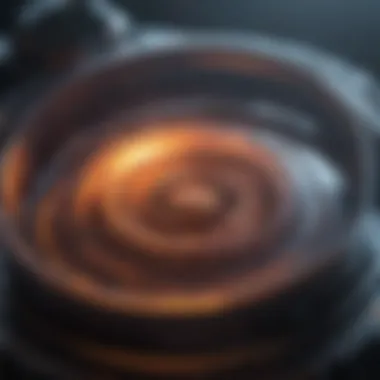
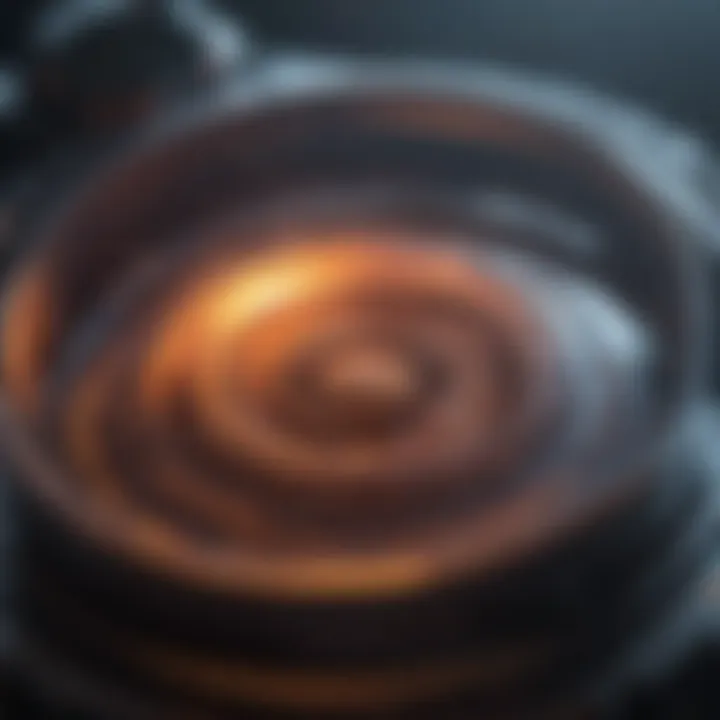
Intro
In an era where precision and reliability define success in industrial operations, continuous vibration monitoring emerges as a cornerstone technique. With technology advancing at a breakneck pace, maintaining machinery health isn't just an option; it’s a necessity. This approach not only assists in spotting potential failures within machinery but also enhances operational efficiency. By collecting and analyzing data on vibrations, industries from manufacturing to aerospace can read the behaviors of their equipment like an open book.
Continuous vibration monitoring refers to the process of using sensors and diagnostic tools that provide real-time feedback on the health of machinery. As simple as it seems, this practice involves a complex interplay of physics, engineering, and technology. The data collected can predict failures, thereby saving costs and leading to improved operational outcomes.
Understanding the principles behind vibration analysis is pivotal. These principles involve measuring vibrations at various points and frequencies. Practically speaking, this means utilizing accelerometers and transducers to capture and quantify movement data. Such insights lead operators to make informed decisions ahead of catastrophic failures, underpinning the concept that prevention is better than cure.
Through this article, we shall venture into the mechanics behind continuous vibration monitoring and its relevance across different sectors. Moreover, we'll dissect the merits of ongoing monitoring, challenges that surface during its implementation, and prospects for future advancements in this field. By considering real-world applications and pertinent case studies, we offer knowledge that resonates with scholars, researchers, and professionals in maintenance, data analysis, and engineering.
As we unravel the core concepts of this critical monitoring technique, we'll illuminate how these insights foster improved machine reliability and operational efficiency. Let’s delve into the key findings.
Foreword to Continuous Vibration Monitoring
The realm of machinery health and performance can often resemble a finely tuned orchestra. Each component, like an instrument, must play its part seamlessly, ensuring that everything runs harmoniously. Continuous vibration monitoring stands as a central conductor in this scenario, steadily observing and analyzing the 'music' made by machines.
Definition and Importance
Continuous vibration monitoring is employed as a proactive technique aimed at assessing the condition of machinery and equipment, to identify potential failures before they manifest. In a world where downtime can cost untold amounts in productivity and repairs, the value of this monitoring technique becomes crystal clear. By continuously capturing vibration data, it offers insights that help maintenance professionals make informed decisions about when to service equipment.
The importance of this continuous monitoring cannot be overstated. Think about it: equipment failure often doesn’t happen overnight. It usually shows a plethora of signs, often observable through vibrations. By monitoring these vibrations consistently, companies can intervene at the first sign of trouble—kind of like tuning a guitar before a concert instead of trying to fix it midway through a performance.
Furthermore, the data collected can be stored and analyzed over time, which allows for trends and patterns to be recognized. This historical data not only helps in predicting future failures but also aids in optimizing maintenance schedules, ultimately leading to enhanced operational efficiency.
Historical Context
The roots of vibration monitoring trace back to the early 20th century when the industrial revolution was in full swing. The rise of machinery and heavy equipment in factories highlighted the need for effective monitoring systems to ensure ongoing operational efficiency. Initially, methods of vibration detection were rudimentary, often involving standardized methodologies based on visual inspections and rudimentary audio feedback.
Over the decades, technological advancements have fundamentally altered this landscape. The introduction of accelerometers in the 1950s marked a significant leap forward, enabling more accurate and detailed vibration assessments. These devices could measure vibrations at a much finer scope than human assessments ever could.
By the late 20th century, with the advent of digital technology, the fidelity of vibration monitoring continued to evolve. Notably, the integration of computer systems allowed for real-time analysis, which fundamentally changed how industries approached machinery maintenance. Today, continuous vibration monitoring has become a staple in various sectors ranging from aerospace to automotive industries.
As we usher into a new era, the evolving technologies promise even more sophisticated monitoring capabilities—resulting in a cycle of perpetual improvement. Understanding this context equips industry professionals with the knowledge to appreciate how far we’ve come and points towards where we are likely headed. By learning from history, stakeholders can make better choices that lead to safer and more efficient operations.
Fundamental Principles of Vibration Monitoring
Understanding the fundamental principles of vibration monitoring is akin to laying down the bedrock for any successful structural analysis or machinery assessment. Vibration monitoring doesn’t just serve as a technical tool but as a vital element in managing the efficacy and longevity of equipment. Recognizing these principles allows professionals to diagnose issues early, prolong machinery lifespans, and ultimately save significant costs associated with downtime and repairs.
Basic Concepts of Vibration
Vibration itself can be broadly defined as the oscillatory motion of an object around an equilibrium position. In practical terms, when machinery operates—be it an electric motor, turbine, or large industrial press—various components produce vibrational energy due to mechanical movement and friction. This energy manifests in several forms, including displacement, velocity, and acceleration.
- Displacement: This refers to the distance the machinery moves from its rest position during vibration. Measuring displacement offers insights into how much a mechanical part is strained during operation.
- Velocity: Often considered for its operational relevance, velocity measures the speed of vibration changes, thus indicating how rapidly an equipment component is altering its position.
- Acceleration: This aspect captures the rate of change of velocity, providing critical information regarding the forces acting on equipment and hinting at potential failure points.
Each of these components must be monitored to create a complete picture of a machine's health. It’s not unlike a doctor checking a patient’s heart rate and rhythm—it’s all about understanding the signals presented.
Key Terminology
Grasping the key terminology in vibration monitoring is essential for effective communication among industry professionals and academics alike. Here are some crucial terms to familiarize oneself with:
- Amplitude: This represents the maximum extent of vibration, providing a quantifiable measure of its intensity. High amplitude can often indicate a problem needing immediate attention.
- Frequency: The number of cycles per unit of time, usually measured in Hertz (Hz). Frequency analysis can help identify specific operational issues, as machinery tends to vibrate at distinct frequencies based on its components.
- Harmonics: These are multiples of a fundamental frequency that arise from regular mechanical movement. Monitoring these can be critical, as they might point to misalignments or wear in machinery.
- Dynamic Response: This encompasses how well a system reacts to vibrations, and it’s vital for understanding potential negative impacts on performance.
When these terms are mastered, they enrich the conversation around machinery health and facilitate deeper engagement with the subject matter. Keeping this terminology handy can make life a lot easier when discussing findings or exploring vibration monitoring technologies.
"Emphasizing the fundamental principles of vibration monitoring aids not just in reactive measures but transforms maintenance into a proactive, strategic process."
By embedding oneself in these fundamental concepts and terminologies, the path toward effective implementation of continuous vibration monitoring becomes clearer. It is an enabler in various applications, from industrial machinery to aerospace engineering, making the grounding principles imperative for success.
Types of Vibration Monitoring Techniques
Understanding the different types of vibration monitoring techniques is essential for effectively assessing machinery performance and reliability. Each of these techniques serves unique purposes and bumps against various practical and economic considerations. Grasping the distinctions between active, passive, remote, on-site, continuous, and periodic monitoring unveils a world of strategies that can influence maintenance schedules, safety protocols, and even overall operational efficiency.
Active vs. Passive Monitoring
In the realm of vibration monitoring, the choice between active and passive monitoring can often dictate the outcome of maintenance strategies. Active monitoring involves using devices that actively transmit data, like accelerometers or strain gauges, to measure vibrations as they occur. Think of it as having a watchdog: it’s always there, continuously observing and barking out alerts.

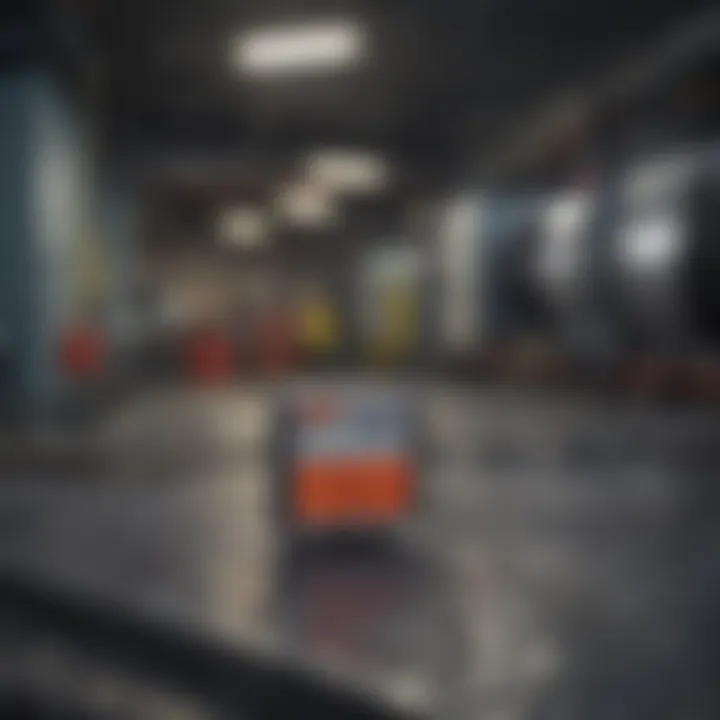
On the other hand, passive monitoring tends to leverage existing machinery vibrations without imposing additional complexity. It's more like casually observing rather than actively seeking out disturbances. Here, most sensors collect data in a less intrusive manner, which can be advantageous as it minimizes interference with operations. While passive systems may miss certain rare events, they shine in environments where constant monitoring isn't feasible or where resource allocation is strict.
Remote vs. On-site Monitoring
Location plays a pivotal role in how data is gathered for vibration monitoring. Remote monitoring enables engineers to collect data from machinery located in hard-to-reach places or on assets spread over vast distances. This technique allows for an ongoing assessment without the need for constant physical presence, which can save time, effort, and even travel costs.
In contrast, on-site monitoring offers a hands-on approach—engineers use handheld devices or stationary systems to collect real-time data right at the source. This can be particularly handy in diagnosing immediate issues and provides the benefit of immediate tactile evaluation. However, it can become labor-intensive and possibly disruptive to ongoing operations. Each technique has its pros and cons, and the choice often hinges on operational demands and logistical constraints.
Continuous vs. Periodic Monitoring
The distinction between continuous and periodic monitoring is crucial for crafting a reliable maintenance program. Continuous monitoring captures trends and anomalies in vibrations on an ongoing basis, akin to a health monitor that streams vital signs in real-time. This presents a comprehensive picture and aids in the adoption of predictive maintenance strategies, helping to foresee equipment failures before they manifest into costly downtime.
Conversely, periodic monitoring—often scheduled at regular intervals—incurs lower initial costs but may overlook significant changes between assessments. This method is akin to taking a quick pulse rather than tracking heart rate variability over time. While beneficial in certain contexts, relying solely on periodic checks can lead to missed insights and unexpected failures, particularly in high-speed or high-stress environments.
Here’s a brief overview of the two methods:
- Continuous Monitoring:
- Pros: Immediate feedback, early detection of issues.
- Cons: Higher setup costs, data management can be complex.
- Periodic Monitoring:
- Pros: Lower costs, easier data management.
- Cons: Potential to miss critical failures, less comprehensive data.
In summary, navigating the types of vibration monitoring techniques forms the backbone of effective machinery health management. Selecting the appropriate strategy requires balancing the benefits with the operational constraints, ensuring that the monitoring structure aligns with maintenance goals while optimizing performance.
Technologies in Vibration Monitoring
In the realm of continuous vibration monitoring, the dominance of technology plays a crucial role. As machinery becomes more complex and industries grow increasingly competitive, the need for precise and dependable monitoring systems has soared. The various technologies that facilitate this process not only enhance operational efficiency but also contribute significantly to predictive maintenance strategies. Let’s explore the components of this technological ecosystem, focusing on sensors, data acquisition systems, and analysis software.
Sensors and Transducers
Sensors and transducers are at the heart of vibration monitoring systems. They are designed to detect and convert mechanical vibrations into measurable electrical signals, allowing for accurate assessment of machinery condition.
- Types of Sensors: There are several types of sensors used in vibration monitoring, including piezoelectric accelerometers, capacitive accelerometers, and laser displacement sensors.
- Importance of Sensitivity: The sensitivity of these sensors plays a pivotal role in detecting subtle vibrations that can indicate potential machinery failures.
- Installation Considerations: Proper installation is critical. The placement of sensors on machinery should be strategic, focusing on areas with the highest likelihood of experiencing vibrations. This not only increases the effectiveness of monitoring but also saves time and money in the long run.
"The choice of sensor directly influences the quality of the monitored data, and consequently, the insights derived from it."
Data Acquisition Systems
Once the sensors have done their job, the next critical element is the data acquisition system. This system gathers, digitizes, and stores the data for analysis.
- Data Handling: Effective data acquisition systems handle vast amounts of information quickly and reliably, ensuring that no crucial data is lost.
- Sampling Rates: High sampling rates are essential for capturing transient events. The faster the events occur, the more frequent the data capture must be.
- Integration with Other Systems: Modern data acquisition systems often integrate with existing supervisory control and data acquisition (SCADA) systems, allowing for real-time monitoring and alerting.
Software for Analysis
The final piece of the puzzle is the analysis software. This software processes the collected data, transforming it into actionable insights.
- Data Visualization: Good analysis software includes features for data visualization, enabling users to easily interpret complex information through graphical means.
- Automated Alerts: These systems can be set up to trigger alerts based on predefined thresholds, enabling proactive maintenance before failures occur.
- Advanced Analytics: Some software employs machine learning algorithms to predict failures based on patterns in the data, significantly enhancing the efficacy of the monitoring process.
The integration of these technologies ensures that continuous vibration monitoring can keep pace with the demands of modern industries. With the right tools in place, organizations can safeguard their operations, reduce unnecessary costs, and enhance overall productivity.
Applications of Continuous Vibration Monitoring
Continuous vibration monitoring serves as a cornerstone in many industries where machinery operation is critical. The ability to constantly track and analyze vibration patterns can bring considerable benefits. It’s not just about collecting data; it’s about transforming that data into actionable insights. So, let’s dive into how continuous vibration monitoring finds its place in various sectors.
Industrial Machinery
In the realm of industrial machinery, continuous vibration monitoring is invaluable. Factories today are akin to a symphony, where different machines play their parts to ensure the success of production. If one instrument goes off-key, the entire performance could be jeopardized. By using sensors to detect abnormal vibration patterns, operators can pinpoint potential issues before they escalate into serious equipment failures.
- Predictive maintenance is one prime application in factories. Instead of relying solely on scheduled maintenance, data collected from vibration monitors helps in making informed decisions about repairs. This not only prolongs equipment life but also optimizes productivity.
- Cost savings is another vital component. Diagnosing problems early can prevent costly downtime and extensive repairs. For example, if a pump develops an unusual vibration signal, the maintenance team can intervene early, avoiding a complete failure that could require extensive shutdowns.
Aerospace Engineering
Vibration monitoring in aerospace engineering poses unique challenges yet offers profound benefits, specifically regarding safety and performance. Aircraft components endure extreme environmental conditions, leading to vibrations that can be both complex and critical.
Continuous monitoring equips engineers with the ability to keep tabs on components like engines and structures during flight. This monitoring can indicate:
- Possible structural fatigue, which can compromise an aircraft's integrity over time.
- Engine health through ongoing vibration analysis, allowing for scheduled repairs that are dictated over time, rather than rushed fixes that may lead to more significant problems.
For instance, modern jets often integrate such systems for real-time data analysis. Engineers rely on this information to not only maintain the aircraft but also to enhance design features in future models.
Automotive Sector
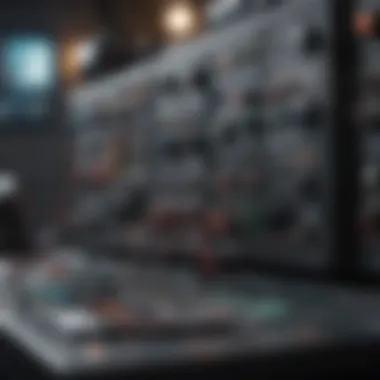
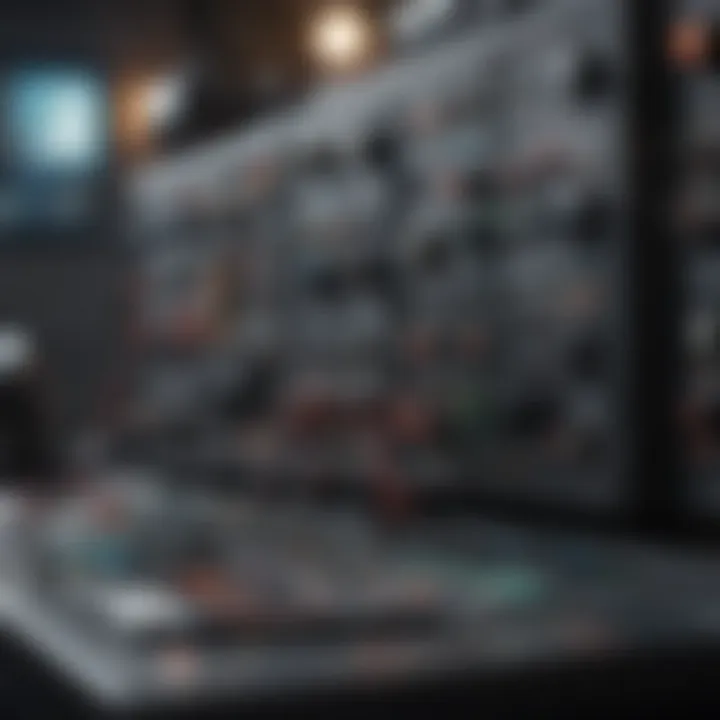
In the automotive world, continuous vibration monitoring serves as a vital tool for enhancing vehicle performance and safety. Cars today combine advanced technology with a complex array of mechanical systems that contribute to their operation.
- Condition-based maintenance is a game changer here. Instead of waiting for problems to become evident, vibration sensors can identify wear and tear on critical components such as suspension systems, engines, and brakes.
- Additionally, it can also enhance automotive design. Engineers utilize vibration data during the development phase to create vehicles that can better handle real-world conditions, leading to improvements in comfort and safety features.
Monitoring vibrations allows manufacturers to collect feedback throughout the vehicle’s lifecycle, which then informs future iterations, making them safer and more reliable.
"Continuous monitoring is not just about detecting issues but understanding them to evolve constantly."
Benefits of Continuous Vibration Monitoring
Continuous vibration monitoring stands out as a pivotal element in maintaining the health of machinery and preventing unexpected failures. By adopting this approach, companies can unlock various benefits that can significantly enhance operational efficiency and reliability. Here’s a detailed exploration of these advantages.
Enhanced Predictive Maintenance
One of the prime benefits of continuous vibration monitoring is its role in predictive maintenance. Traditional maintenance practices often rely on fixed schedules or reactive measures when failures occur. However, by implementing continuous monitoring, companies can detect changes in vibration patterns that signal impending issues long before they escalate.
This leads to a few key considerations:
- Timely interventions: Recognizing signs of wear or misalignment early allows for maintenance to be scheduled at convenient times, minimizing disruption.
- Resource optimization: Predictive maintenance prevents unnecessary inspections or replacements, saving both time and money.
- Data-driven decisions: The use of historical vibration data provides a solid foundation for any maintenance decisions, reducing guesswork.
As a result, organizations can maintain a more efficient workflow and extend the lifespan of their machinery.
Reduction of Downtime
Another significant advantage of continuous vibration monitoring is the substantial reduction in downtime. Equipment failure can bring production to a standstill, leading to costly delays and loss of revenue. Continuous monitoring offers a solution to this age-old problem by enabling operators to:
- Monitor machinery health in real time: This capability means that irregularities are detected immediately, allowing for swift corrective actions.
- Plan maintenance around operational schedules: Instead of waiting for a breakdown, maintenance can be planned during non-peak hours, aligning with the overall operational strategy.
- Minimize emergency repairs: Constant oversight means machines operate within safe parameters resulting in fewer unexpected breakdowns.
These proactive measures ultimately translate into a smoother operation and significant cost savings for businesses.
Improved Safety Protocols
Safety in industrial operations cannot be compromised, and continuous vibration monitoring plays a crucial role in enhancing safety protocols. As machinery ages and wear and tear become more pronounced, the risk of accidents escalates. With continuous monitoring, these risks can be mitigated through:
- Early detection of dangerous states: Identifying unusual vibrations signals potential failures that could lead to catastrophic events. An example might be a fan experiencing erratic vibrations that, if ignored, could lead to catastrophic failure.
- Support for safety audits: Reliable data aids compliance with safety regulations and standards, assuring that protocols are followed rigorously.
- Employee confidence: Knowing that machinery is continually monitored improves worker morale and trust in their working environment, fostering a better safety culture.
"Continuous monitoring is not just a method; it's a strategic approach to ensuring workplace safety and machine health."
In summary, the benefits of continuous vibration monitoring extend far beyond mere machinery upkeep. It transforms the way organizations approach maintenance, operational efficiency, and safety, establishing it as an invaluable tool in modern industrial practices. By embracing this technology, businesses can navigate the complexities of machinery management with greater confidence and foresight.
Challenges in Implementation
Implementing continuous vibration monitoring is not as straightforward as adding a few sensors and calling it a day. While the benefits are clear, there are significant challenges that need to be navigated. Understanding these hurdles helps in crafting a practical approach that addresses the intricacies of the field. In this section, we will dissect the challenges—technical limitations, costs and budget constraints, and the complexities involved in interpreting the data.
Technical Limitations
Technical limitations are often the first stumbling block in the road to effective vibration monitoring. It’s crucial to acknowledge that not all machinery is created equal. Some older machines may not have been designed with monitoring capabilities in mind, making installations tricky. Compatibility issues arise when current technology does not align with older equipment. Additionally, proximity to noise sources can compromise sensor accuracy. If the vibrating machinery is surrounded by other equipment that vibrates as well, discerning between important signals and background noise becomes challenging.
Moreover, there’s the issue of sensor placement; an improper position can yield unreliable data. Sensor drift and sensitivity also depend on environmental factors, like temperature and humidity, which can undermine monitoring accuracy. These technical limitations necessitate thorough groundwork for selecting and positioning sensors appropriately to ensure they capture true vibrational patterns.
Costs and Budget Constraints
No one ever said you can get something for nothing. The costs associated with continuous vibration monitoring can pile up quickly. Setting up the infrastructure—purchasing high-quality sensors, installation, data acquisition systems—adds up. Then, there’s the recurrent expense of maintaining the system, including calibration and software updates. The shift from traditional monitoring, which might require limited resources, to a continuous system demands a well-thought-out budget.
Even if an organization recognizes the importance of continuous monitoring for machinery health, financial constraints may force them to compromise on the quality of equipment or skip layers of monitoring altogether. Organizations may end up using cheaper, less reliable systems due to budget limitations, potentially leading to poorer outcomes in machine performance or even failures down the road. So, balancing budget considerations with the goal of effective monitoring is a delicate dance that management must carefully navigate.
Data Interpretation Complexity
Having the data is one thing, but making sense of it is an entirely different ball game. Continuous vibration monitoring can produce torrents of data, which, if not processed correctly, can drown out valuable insights. With the advent of Internet of Things (IoT) technologies, tons of continual data comes flooding in, often in real-time. Analyzing that data requires a skilled interpretation framework.
The challenge lies not in just collecting this data but in translating it into actionable intelligence. Trained personnel who can interpret vibration signals correctly are paramount for an organization. Misinterpretation could lead to unnecessary maintenance or, worse, ignoring a relationship between vibrations and potential machine failure.
More often than not, the time between detection and response is critical, and delays in interpreting data can result in costly machine downtimes. Therefore, organizations must invest in training or hiring skilled analysts who can turn numerical data into clear narratives about the machinery's health.
"In the world of vibration monitoring, having data is only half the battle; knowing what to do with it is where the real skill lies."
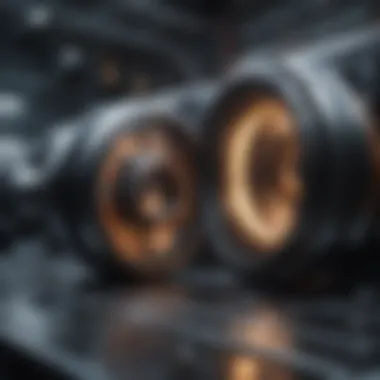
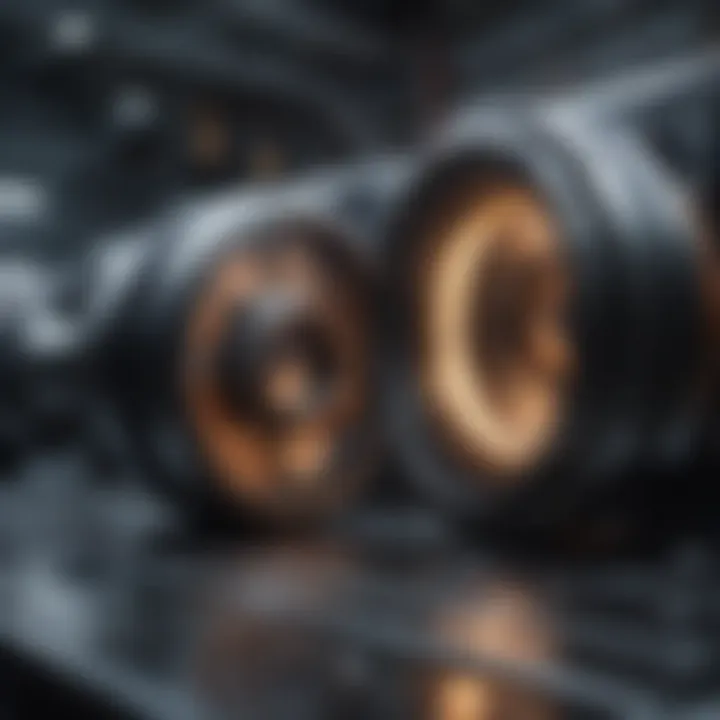
Each of these challenges—technical limitations, budget constraints, and complex data interpretation—highlights the necessity of thoughtful planning and dedicated resources for successful implementation of continuous vibration monitoring. A methodical approach to overcoming these hurdles is not just sensible; it's essential for reaping the full benefits of this critical technology.
Case Studies in Vibration Monitoring
Case studies play a crucial role in understanding how continuous vibration monitoring operates in real-world settings. They provide concrete evidence of the benefits and challenges associated with this technology, showcasing how industry leaders utilize it to their advantage. Through these examples, readers can grasp not only the functionality but also the practical implications that vibration monitoring has within various sectors.
Exploring case studies illuminates the road from theory to practice, demonstrating successful implementations and revealing lessons learned. This narrative becomes especially pertinent for students, researchers, and professionals keen on grasping the nuances of vibration monitoring. It builds a bridge between academic insights and pragmatic outcomes, reinforcing the significance of continuous monitoring in maintaining machinery health and operational efficiency.
Successful Implementations
Successful implementations of continuous vibration monitoring can often resemble a finely tuned orchestra. Each component must harmonize for optimal performance. One pertinent example comes from the aerospace industry. Airbus has adopted continuous vibration monitoring systems in their aircraft. By equipping engines with sophisticated sensors, they can identify anomalies in real-time. This proactive approach has led to improved safety while also optimizing maintenance schedules and reducing costs.
Another illustrative case involves a major automotive manufacturer utilizing vibration monitoring to assess assembly line machinery. The firm installed continuous monitoring systems on critical machinery, which allows technicians to detect changes in vibration patterns that could indicate wear or potential failures. This system pays dividends by preventing production stoppages, exemplifying how targeted monitoring aligns with operational efficiencies.
In both instances, embracing vibration monitoring has resulted in better decision-making and ultimately enhanced productivity.
Lessons Learned
With every success story, there are also valuable lessons to be garnered. One crucial lesson is the necessity of integrating operator training into the deployment of vibration monitoring systems. In the aerospace case, a common oversight was the lack of in-depth training for personnel on how to interpret the data from the sensors. This gap resulted in underutilization of the system's capabilities at first, with several key indicators being overlooked. Continuous education is essential, especially when technological advancements occur at breakneck speed.
Drawing from the automotive example, it became clear that the selection of suitable sensors impacted the efficacy of the monitoring systems. Upon initial deployment, the chosen sensors didn’t account for specific vibrational frequencies common in that particular machinery. This oversight led to false readings and unnecessary maintenance actions. The lesson here emphasizes the importance of thoroughly understanding operational parameters and selecting the right monitoring tools accordingly.
"Proper implementation and integration of continuous vibration monitoring not only saves costs but creates a culture of proactive maintenance that can reshape operational norms."
Future Trends in Vibration Monitoring
As industries evolve, the need for effective monitoring techniques becomes increasingly urgent. Continuous vibration monitoring is no exception. Understanding future trends in this field is vital for adapting to technological advancements and improving operational effectiveness. It highlights the intersection of innovative technologies and practical applications, which ultimately benefits machinery health and safety protocols. This section will delve deeply into specific elements that are shaping the landscape of vibration monitoring, including advancements in sensor technology, integration with IoT systems, and the applications of machine learning.
Advancements in Sensor Technology
The revolution in sensor technology has been nothing short of remarkable. Sensors that were once bulky and limited in capabilities have transformed into compact, highly sensitive devices. These modern sensors boast greater precision, sensitivity, and durability, allowing for effective vibration capture under various conditions.
- Wireless Capabilities: One significant breakthrough is the advancement of wireless sensor technology. This enables easier installation and reduces the risk of cable damage. Wireless sensors can seamlessly communicate data in real-time, providing continuous assessment without the hassle of extensive wiring.
- Miniaturization: Size matters when it comes to vibration sensors. The miniaturization of these devices means they can be placed in hard-to-reach areas of machinery where monitoring is crucial, yet challenging to access.
- Multi-functionality: The newer models of sensors often come equipped with multi-functionality, such as measuring temperature, pressure, and vibrations all in one device. This holistic approach provides a more comprehensive view of machinery health.
The continuous enhancement of sensor technology is not just about performance but also encompasses affordability and reduced energy consumption, making sophisticated monitoring accessible to a wider range of industries.
Integration with IoT
The integration of continuous vibration monitoring systems with Internet of Things (IoT) technologies marks a new era in industrial maintenance. The convergence of these technologies opens the door to unprecedented opportunities for better decision-making and operational efficiency.
- Real-Time Data Collection: With IoT, data is collected in real-time and transmitted to centralized systems for monitoring and analysis. This immediacy allows engineers and maintenance staff to identify issues as they arise, reducing response times significantly.
- Remote Monitoring: The ability to monitor machinery from virtually anywhere is a game changer. Maintenance teams can quickly assess vibration data remotely, reducing the need for site visits and enabling prompt action when necessary.
- Predictive Analysis: IoT devices can utilize vast amounts of data, making it possible to predict potential failures. The algorithm can analyze trends and alert the team to anomalies, which greatly enhances maintenance scheduling.
Integrating IoT with vibration monitoring doesn't just streamline processes, it also promotes proactive maintenance strategies and helps to extend the lifespan of equipment.
Machine Learning Applications
Machine learning is steadily carving its niche in vibration monitoring. The capabilities of machine learning algorithms to learn from and interpret vast volumes of vibration data bring forth exciting possibilities for predictive maintenance.
- Pattern Recognition: Machine learning models can identify patterns in vibration data that might be imperceptible to the human eye. By recognizing these patterns, potential issues can be anticipated before they escalate.
- Automated Diagnostics: Utilizing machine learning in diagnostic processes minimizes human error. Automated systems can tag anomalies, categorize severity, and recommend specific maintenance actions based on historical data and learned behaviors.
- Customized Solutions: Algorithms enable more tailored approaches to vibration monitoring, catering to the unique characteristics of different machines and environments. This is especially useful in sectors like aerospace and automotive where precision is paramount.
The implementation of machine learning in vibration monitoring stands to transform how maintenance teams approach equipment health, creating smarter and more reliable solutions.
"The synergy of advanced sensor technologies, IoT integration, and machine learning capabilities is reshaping the future of vibration monitoring, providing industries with tools that are not only smart but adaptable for the challenges ahead."
Finale
In concluding this discussion on continuous vibration monitoring, it's crucial to underscore the significant role this practice plays across numerous industries. This isn't merely about placing sensors and gathering data; it's about creating a culture of vigilance and proactive management that is paramount in today's fast-paced environment. Continuous monitoring not only enhances machinery longevity but also safeguards workers and optimizes operational efficiency.
Summation of Key Insights
Throughout this article, we've traversed various facets of continuous vibration monitoring. Here’s a quick recap of the key insights:
- Definition and Relevance: Continuous vibration monitoring helps assess the health of machinery in real time, preventing failures and extending the service life of equipment.
- Importance of Technology: The implementation of advanced sensors and data analysis tools has revolutionized the way industries approach maintenance.
- Applications in Industries: From aerospace to automotive, continuous monitoring finds its use in diverse sectors, each benefiting from reduced downtime and improved productivity.
- Challenges Weighing In: Technical limitations, budget constraints, and the complexity of data interpretation pose significant challenges that businesses must overcome.
"Regular monitoring is not an optional luxury but an operational necessity in modern machinery management."
Understanding these insights allows stakeholders to strategize better, ensuring that best practices are adopted and effectively integrated into operations.
Final Thoughts on Continuous Monitoring
Looking toward the future, it becomes increasingly clear that continuous monitoring will only grow in importance. With advancements in sensor technology and the integration of IoT, the potential for businesses to harness data will evolve, creating even smarter predictive maintenance strategies. Additionally, embracing machine learning techniques can facilitate more insightful data analysis processes, allowing for quicker decision-making.
In summary, organizations that invest in continuous vibration monitoring are not only protecting their assets but also paving the way for innovative business practices. As industries continue to confront new challenges, embracing this technology can provide a competitive edge, making it a wise investment for both present and future needs.