A Comprehensive Examination of Thermoset Polymers and Their Impact
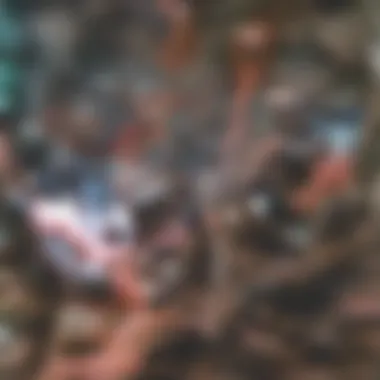
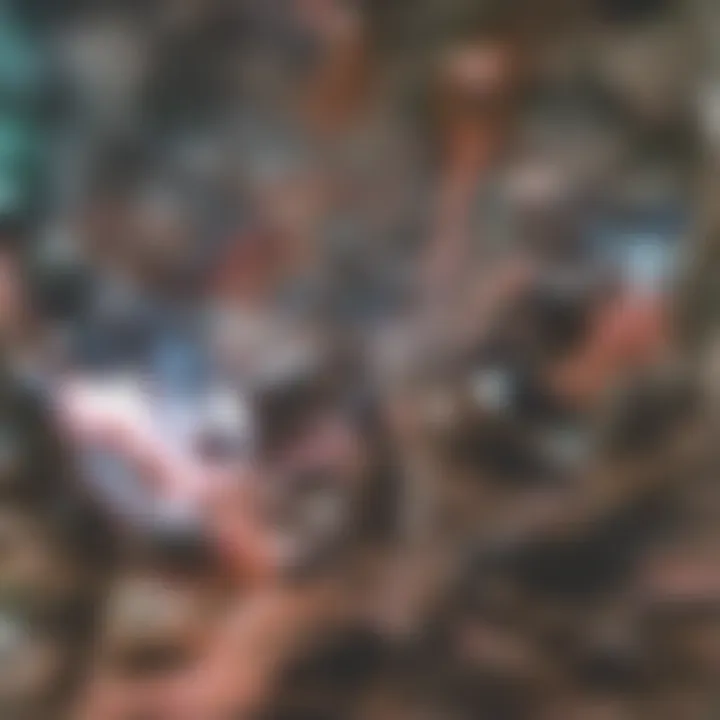
Intro
Thermoset polymers represent a unique category of synthetic materials known for their robustness and thermal stability. These polymers undergo a curing process, transforming them from a malleable state into a rigid structure that cannot be re-molded. This characteristic distinguishes thermosets from thermoplastics, which can be reshaped upon heating. In today's material science landscape, understanding thermoset polymers is crucial for various applications, from automotive components to electronics.
This article will dissect thermoset polymers, emphasizing their chemical structure, properties, processing methods, and applications. In doing so, it will clarify the fundamental differences between thermosetting and thermoplastic polymers. We will also cover recent advancements in thermoset technology, showcasing their role in pushing the boundaries of materials engineering.
Key Findings
Major Results
- Chemical Structure: Thermoset polymers possess a cross-linked network of polymer chains. This intricate structure imparts superior mechanical properties and heat resistance, making them ideal for high-stress applications.
- Processing Methods: Common processing techniques for thermosets include compression molding, transfer molding, and resin infusion. Each method has its own advantages concerning production efficiency and material properties.
- Applications: Industries utilizing thermoset polymers are diverse, including aerospace, automotive, and construction. Their ability to withstand high temperatures and maintain structural integrity under stress makes them invaluable in these sectors.
- Recent Advancements: Innovations in thermoset materials have led to the development of bio-based thermosets and improved recyclability, laying the groundwork for a more sustainable future in materials science.
Discussion of Findings
The findings highlight the significance of thermoset polymers in various industries. For instance, the aerospace sector relies heavily on their lightweight yet durable nature. Meanwhile, advancements in sustainability in thermoset development could reduce environmental impact, signifying a step forward in responsible manufacturing practices. Understanding these polymers' unique properties and ongoing advancements is crucial for professionals and academics in materials science.
"Thermoset polymers are not just materials; they are fundamental to modern engineering, offering solutions where traditional materials fall short."
Methodology
Research Design
This examination employed a qualitative research design, focusing on comprehensive reviews of existing literature and case studies. This method ensures a deep understanding of thermoset polymers, allowing for an analysis of their chemical structures, properties, and applications.
Data Collection Methods
Data was gathered from peer-reviewed journals, technical reports, and industry publications. The analysis incorporated insights from recent advancements in technology and application-focused research to provide a current perspective on thermoset polymers.
By structuring this information clearly, we aim to illuminate the complexities and vital role thermoset polymers play in contemporary material science.
Prologue to Thermoset Polymers
Thermoset polymers hold a pivotal position in materials engineering, characterized by their unique properties and applications. As their name suggests, thermosets are polymers that undergo a chemical change when cured, resulting in a rigid structure that is not re-moldable. This feature distinguishes them from other polymer types, particularly thermoplastics.
Definition and Characteristics
Thermoset polymers are formed through a process known as curing or cross-linking, where polymer chains create extensive networks. This process effectively eliminates flexibility in the material, leading to high-temperature resistance and exceptional strength. Common examples of thermoset polymers include epoxy resins, polyester resins, and phenolic resins.
The primary characteristics of thermoset polymers can be summarized as follows:
- Thermal Stability: They exhibit excellent heat resistance, making them suitable for high-temperature applications.
- Mechanical Strength: These materials retain their mechanical properties over time and under stress, which makes them ideal for demanding environments.
- Chemical Resistance: Thermosets have good resistance to solvents and chemicals, thus prolonging their lifespan in harsh operating conditions.
Comparison with Thermoplastic Polymers
Understanding the differences between thermoset and thermoplastic polymers is crucial for selecting the right material for specific applications. Unlike thermosets, thermoplastic polymers can be reheated and reshaped without undergoing a chemical change. This characteristic enables greater flexibility, but comes with reduced rigidity and heat resistance compared to thermosets.
Thermoplastics are typically easier to process since they can be melted and molded multiple times, while thermosets require a curing process that makes them permanent once formed. Here are a few chief compare points:
- Reprocessability: Thermoplastics can be reprocessed, thermosets cannot.
- Heat Resistance: Thermosets generally outperform thermoplastics at high temperatures.
- Applications: Thermosets are majorly used in situations where durability is paramount, such as in aerospace and automotive industries.
This foundational understanding of thermoset polymers provides a framework for exploring their chemical structures, properties, and varied applications. This examination underscores their significance in industrial practices, driving advancements in technology and material science.
Chemical Structure of Thermoset Polymers
Understanding the chemical structure of thermoset polymers is fundamental for grasping their unique properties and applications. Thermoset polymers are characterized by their cross-linked structure, which defines not only their mechanical and thermal stability but also their permanence when cured. This section will elaborate on different cross-linking mechanisms involved in crafting these materials and will discuss the distinct types of thermoset resins that are commonly used.
Cross-Linking Mechanisms
Cross-linking is a critical mechanism in the formation of thermoset polymers. It involves creating bonds between polymer chains, resulting in a three-dimensional network. This network structure is what gives thermoset polymers their rigidity and thermal stability. The cross-linking process can occur through different mechanisms, including condensation, addition, and free-radical mechanisms.
- Condensation Cross-Linking: This involves the reaction of monomers that results in the release of small molecules, often water. This method is typical in phenolic resins and offers moderate to high strength after curing.
- Addition Cross-Linking: In this approach, reactive groups (such as isocyanates or epoxides) react with functional groups on another polymer chain. This type of cross-linking is notable for epoxy resins, and is known for producing superior mechanical performance.
- Free-Radical Mechanisms: This involves the initiation of a chemical reaction in which free radicals add to unsaturated bonds leading to cross-linking. This mechanism is common in many thermosetting applications, particularly with polyester resins.
These cross-linking mechanisms contribute to the characteristics that make thermoset polymers suitable for various applications.
Types of Thermoset Resins
Several types of thermoset resins are important in the study of polymer chemistry. Each type possesses unique properties and applications, thus influencing the choice of resin for particular uses.
Epoxy Resins
Epoxy resins are known for their excellent adhesive properties and superior chemical resistance. This resin has gained popularity in applications ranging from coatings to structural adhesives. One of the key characteristics is their hardness after curing. This makes epoxy an ideal choice for demanding applications like aerospace and automotive sectors.
A unique feature of epoxy resins is their outstanding adhesion to various substrates, including metals and plastics. However, they can be sensitive to high temperatures, which can limit their use in extreme environments.
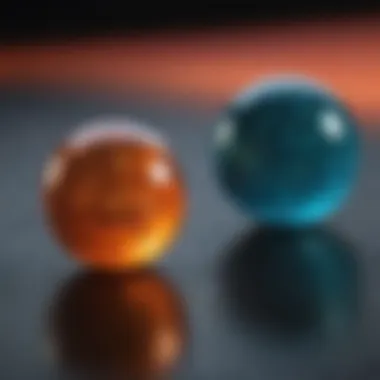

Polyester Resins
Polyester resins are widely used and valued for their versatility and cost-effectiveness. They are commonly used in applications that require good mechanical properties and resistance to moisture. Polyester resins are especially favored in the production of fiberglass composites.
A noteworthy aspect of polyester resins is their relatively lower curing time compared to other thermosetting materials; however, they may not have the same adhesion properties as epoxy. This can sometimes limit their use in specific high-performance applications.
Phenolic Resins
Phenolic resins are distinguished by their high thermal stability and flame resistance. They are often utilized in applications where fire resistance is a requirement, such as in electrical insulation and kitchen equipment. A significant feature of phenolic resins is their ability to withstand high temperatures without degradation.
On the downside, the curing process can be longer and more complex, which can increase manufacturing costs. The material can also be more brittle compared to other thermoset resins, making it less suitable for applications requiring flexibility.
In summary, the chemical structure of thermoset polymers, defined primarily by their cross-linking mechanisms and resin types, highlights their suitability across various industries. Each resin type offers distinct advantages and limitations, making the choice of resin crucial for specific applications.
Properties of Thermoset Polymers
The properties of thermoset polymers are essential to understand their functionality, applications, and limitations. Generally, these materials are known for their excellent thermal stability, mechanical performance, and chemical resistance. These properties make them suitable for a wide range of applications across various industries. It is crucial to consider these characteristics when selecting materials for specific uses, as they directly impact product performance and durability.
Thermal Stability and Resistance
Thermal stability is a defining property of thermoset polymers. They maintain structural integrity even when exposed to high temperatures. This quality results from their crosslinked chemical structure, which prevents them from melting or softening under heat. As a result, thermoset polymers are often used in applications where heat resistance is necessary, such as automotive engine components and electronic housings.
Thermal resistance is essential in various sectors because failures due to heat can lead to significant safety concerns and financial losses. Understanding how thermoset polymers withstand high temperature can aid engineers and developers in designing products that last and perform consistently.
Mechanical Properties
Mechanical properties refer to how materials react to external forces. Thermoset polymers generally exhibit high mechanical strength, making them suitable for structural applications. The most notable mechanical properties of thermoset polymers include tensile strength, flexural strength, and impact resistance.
Tensile Strength
Tensile strength is the maximum stress that a material can withstand while being stretched or pulled before failing. This property is significant because it indicates how well a thermoset polymer can perform under tension. High tensile strength contributes to the overall robustness of engineered parts.
The key characteristic of tensile strength is its role in determining how materials will behave in service. A material with high tensile strength is preferable in applications where load-bearing is critical, such as in structural components and machinery. However, the disadvantage of highly rigid thermoset polymers can be their susceptibility to brittle fracture under extreme stress, which can limit their applications in highly dynamic environments.
Flexural Strength
Flexural strength is the ability of a material to resist deformation under load. This property is particularly crucial for applications where bending or flexing may occur. Thick or thick sections of thermoset polymers usually exhibit higher flexural strength.
Flexural strength is a beneficial choice as it ensures that materials do not yield or break easily during use. When designing parts that require strength under bending loads, thermoset polymers' flexural properties are often considered vital. Nevertheless, too much rigidity can lead to issues in applications that require some flexibility, thus posing a challenge during design.
Impact Resistance
Impact resistance refers to how well a material can withstand sudden forces or shocks. In industries such as aerospace or automotive, this property is crucial. Thermoset polymers that exhibit high impact resistance can prevent catastrophic failures during operation.
The distinct feature of impact resistance is its ability to absorb energy without fracturing. This benefit makes thermoset polymers an excellent choice in products exposed to dynamic stress. However, if the polymer is too rigid, it might not absorb enough energy, leading to failure under exceptionally severe impacts. Thus, a balance must be struck in design for optimal performance.
Electrical Properties
Electrical properties of thermoset polymers are also worth noting, particularly their insulative qualities. These materials often serve as excellent electrical insulators, preventing current flow. This is essential in electronic devices to maintain safety and performance. The inherent characteristics of thermoset materials help them avoid breakdown under high voltages, allowing them to be widely used in electrical applications.
Chemical Resistance
Chemical resistance defines the ability of thermoset polymers to withstand degradation from various chemical agents. Many thermoset polymers are formulated to resist acids, bases, and solvents. This property is vital for applications in environments involved with harsh chemicals, such as oil and gas or manufacturing sectors. The evolution of these resistant materials enhances their durability and lifespan in critical applications, making them favorable in industrial applications.
Manufacturing Processes for Thermoset Polymers
Manufacturing processes for thermoset polymers play a critical role in their overall functionality and performance. Understanding these methods is essential for engineers and designers who wish to optimize the use of thermosetting materials in various applications. Thermoset polymers are characterized by their irreversible curing process, which results in a hard and inflexible material. This quality leads to several benefits, including enhanced thermal stability and chemical resistance. However, the manufacturing processes involved can be complex, requiring careful consideration of various factors such as material selection, economic viability, and environmental impact.
Among the notable manufacturing techniques, casting and molding, compression molding, resin transfer molding, and filament winding stand out for their versatility and effectiveness in producing high-quality thermoset products.
Casting and Molding Techniques
Casting and molding techniques are the foundations of thermoset polymer manufacturing. These processes involve shaping liquid thermoset resins into solid forms. Casting uses a mold to create intricate designs, while molding provides a quick method for high-volume production. The choice of technique often hinges on the desired attributes of the final product.
"The simplicity of casting allows for detailed designs, while the rapid production capabilities of molding make it ideal for large-scale applications."
These methods ensure the performance characteristics of thermosets are realized—offering high strength and toughness once cured.
Compression Molding
Compression molding is particularly advantageous for producing thermoset parts. In this method, material is placed into a heated mold, which is then closed and pressure is applied. The heat initiates the curing process, transforming the material into its final form. This technique is cost-effective due to its ability to produce large quantities with minimal waste. Moreover, it allows for consistent thickness and uniform properties throughout the product. This method is commonly used in manufacturing automotive components and electrical equipment.
Resin Transfer Molding
Resin transfer molding (RTM) involves injecting liquid thermoset resin into a mold containing pre-placed fiber reinforcement. This technique combines the best attributes of both molding and composites, resulting in lightweight, strong parts. The process is conducive to complex geometries and reduces the risk of dry spots in the composite material. RTM is increasingly applied in industries such as aerospace and sports equipment, where performance requirements demand high strength-to-weight ratios.
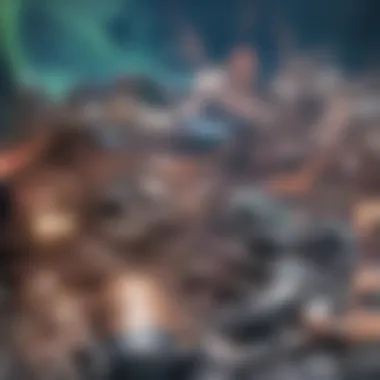
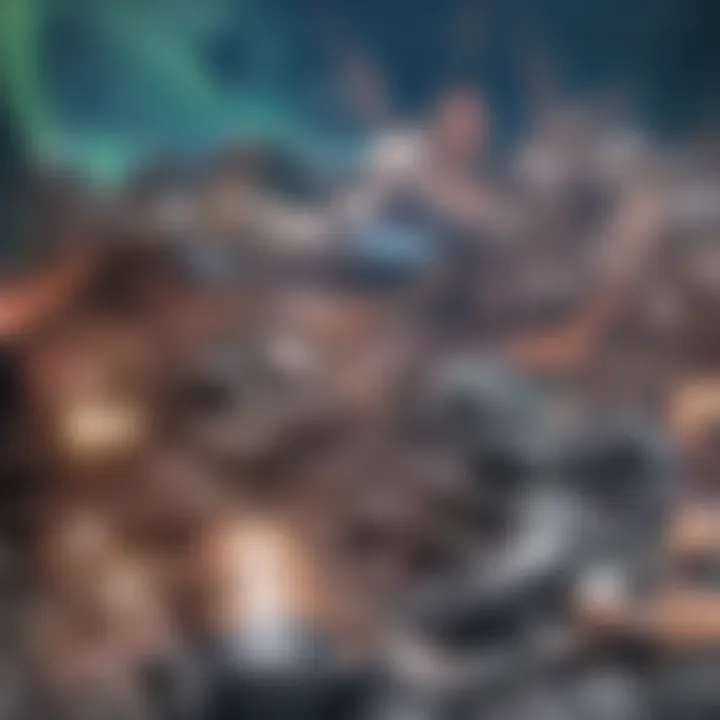
Filament Winding
Filament winding is a specialized manufacturing process used for producing hollow thermoset structures like tubes and tanks. In this process, continuous fiber strands are wound around a mandrel in a pre-determined pattern. The fibers are then coated with a thermoset resin that hardens upon curing, resulting in a composite structure with high tensile and compressive strength. Applications of filament winding are prevalent in the aerospace and automotive sectors, where lightweight and high-strength materials are essential.
Applications of Thermoset Polymers
Thermoset polymers are pivotal in various industries due to their unique properties, which make them suitable for demanding applications. In this section, we will delve into the significance of thermoset polymers across multiple sectors, emphasizing their benefits and considerations. These materials are integral in developing products that require durability, heat resistance, and structural strength.
Automotive Industry
In the automotive sector, thermoset polymers play a vital role in ensuring vehicle performance, safety, and longevity. They are commonly used in components like bumpers, dashboards, and electrical housings. The resins provide high strength-to-weight ratios, aiding in fuel efficiency without sacrificing safety.
Additionally, their ability to withstand high temperatures makes them ideal for engine components and under-the-hood applications. Manufacturers favor these materials because they can be molded into complex shapes that fit precise design specifications. Overall, the adoption of thermoset polymers in automotive engineering has led to lighter and more efficient vehicles.
Aerospace Applications
The aerospace industry relies heavily on thermoset polymers for their excellent strength, thermal stability, and resistance to environmental factors. Components such as aircraft interiors, structural parts, and composites used in wings or fuselage often utilize these materials. This reliability is essential in an industry where every gram matters, directly affecting fuel consumption and performance.
Thermoset composites are designed to endure harsh conditions, including extreme temperatures and mechanical stresses. These properties are crucial in maintaining the safety and effectiveness of aerospace applications.
Electrical and Electronics
In the electrical and electronics field, thermoset polymers are essential for insulating materials, circuit boards, and enclosures. Their dielectric properties ensure efficient insulation, making them suitable for high-voltage environments. Additionally, thermosets exhibit minimal thermal expansion, which is critical for maintaining dimensional stability in electronic components.
Furthermore, they offer resistance to chemical exposure and moisture, safeguarding electronic devices in various environments. The use of thermoset polymers in electronics enhances the durability and longevity of devices, which is a significant advantage in today's technology-driven world.
Construction Materials
Thermoset polymers are widely used in construction materials due to their durability and versatility. Products such as adhesives, sealants, and composite panels benefit from the resilient nature of these polymers. They can withstand weathering, UV radiation, and mechanical wear, making them ideal for both residential and commercial applications.
Furthermore, their ability to be molded into specific shapes facilitates design freedom in architectural projects. This characteristic allows for innovative solutions in building components, contributing to aesthetic appeal while ensuring structural integrity.
Consumer Products
In the realm of consumer goods, thermoset polymers find uses in items ranging from kitchenware to sporting equipment. Their strength and heat resistance are valuable properties in products that experience regular wear and tear. For example, cookware made from thermoset materials can endure high temperatures without deforming or releasing harmful substances.
Additionally, the customization options available with thermoset polymers enable manufacturers to create unique designs and functional features. The flexibility and performance of these materials ensure that they remain a staple in creating reliable consumer products.
"The diverse applications of thermoset polymers reveal their integral role in modern manufacturing across industries."
Advantages of Thermoset Polymers
The field of materials science values thermoset polymers for their distinct advantages. These benefits make them an essential choice for various applications. Understanding why thermoset polymers are favored provides insight into their roles in modern manufacturing and design. Below, we explore the key benefits: high durability and strength, formability and design flexibility, and cost-effectiveness in mass production.
High Durability and Strength
One of the most significant advantages of thermoset polymers is their high durability and strength. These materials exhibit impressive mechanical properties. When thermosetting resins cure, they undergo a chemical reaction that leads to a hardening process. This process creates cross-linked structures that enhance their resistance to deformation and wear. As a result, thermoset polymers can withstand harsh conditions, including high temperatures and corrosive environments.
"Thermoset polymers can endure challenging conditions that would degrade other materials, particularly thermoplastics."
This durability makes them ideal for industries that require reliability and longevity, like automotive and aerospace. Components made from thermoset materials show a remarkable resistance to environmental factors such as moisture and UV radiation. This property contributes to their longevity in applications like outdoor equipment and structural components.
Formability and Design Flexibility
Thermoset polymers also offer formability and design flexibility. Thermosetting resins can be molded into complex shapes before curing. This characteristic allows engineers and designers to create intricate components that meet specific needs without compromising structural integrity. For example, the resin transfer molding process enables the production of lightweight, high-strength parts for various applications, ranging from household products to industrial machinery.
Moreover, thermosets can accommodate a variety of fillers and reinforcements. This adaptability allows for customization to achieve desired properties, such as increased thermal or electrical resistance. Having this freedom in material design enhances the capabilities of product development across numerous domains.
Cost-Effectiveness in Mass Production
In the context of mass production, thermoset polymers demonstrate cost-effectiveness. Due to their high processing efficiency, manufacturers benefit from reduced cycle times and operational costs. Once the thermosetting resin is cured, the final product is not only durable but also requires less post-processing compared to other materials, which may need additional treatments or coatings.
Additionally, the raw materials for thermoset polymers can often be sourced at a lower cost than alternatives. This affordability in sourcing contributes to their overall economic viability, making them a popular choice in industries that prioritize cost reduction without sacrificing quality.
Limitations of Thermoset Polymers
Understanding the limitations of thermoset polymers is essential when studying their application and performance. While they present impressive advantages, these materials also have specific drawbacks that need consideration. This section will explore three main limitations: brittleness of materials, recycling challenges, and limited repair options. Each of these aspects influences their usability in various industries.
Brittleness of Materials
One of the primary limitations of thermoset polymers is their inherent brittleness. Unlike thermoplastics, which exhibit ductility and can deform under stress, thermoset polymers tend to fracture rather than bend. This brittleness arises from their tightly cross-linked structure, providing strength but reducing flexibility. Depending on the formulation and processing methods, this brittleness can lead to failures in applications demanding high impact resistance.
Implications of Brittleness:
- Application Limitations: Certain sectors, such as automotive or aerospace, require materials that can withstand mechanical stresses. The brittleness of thermosets can restrict their use in high-impact regions.
- Design Constraints: Engineers must consider these properties when designing components, often necessitating additional reinforcements or protective features.


Recycling Challenges
The recycling of thermoset polymers is another significant concern. Unlike thermoplastic materials, which can be remelted and reshaped, thermosets undergo a curing process that creates a permanent structure. This cross-linking makes recycling difficult, if not impossible, through traditional methods. The inability to repurpose these materials leads to increased waste and environmental issues, as discarded thermoset products often end up in landfills.
Recycling Considerations:
- Resource Waste: Valuable materials are lost when thermosets cannot be recycled, creating a need for more raw materials.
- Environmental Impact: The disposal of non-recyclable waste contributes to pollution and resource depletion, raising sustainability concerns in modern manufacturing.
"The challenges of recycling thermoset plastics force industries to rethink waste management strategies and emphasize sustainability."
Limited Repair Options
Thermoset polymers also present limited repair options once they have been damaged. When thermoset materials break, traditional methods such as welding or chemical bonding used effectively on thermoplastics may not work. This limitation is particularly critical in high-cost applications where repairs are necessary, like aerospace or high-performance equipment. Often, components may need to be replaced entirely, leading to increased costs and resource consumption.
Repair Limitations:
- Economic Implications: The inability to repair can lead to higher maintenance costs over the life cycle of the product as whole components must be replaced.
- Operational Downtime: Industries heavily using thermosets may experience longer downtimes while waiting for replacements, impacting productivity and efficiency.
In summary, while thermoset polymers have advantageous properties, understanding their limitations is crucial for industry stakeholders. Awareness about brittleness, recycling challenges, and repair issues can guide material selection and application in engineering processes.
Innovative Developments in Thermoset Technology
Innovative developments in thermoset technology are changing the landscape of material science. This focus on new techniques and materials not only increases the efficiency of product manufacturing, but also addresses environmental and performance concerns. The shift towards sustainability, smart functionalities, and advanced composites signifies a robust evolution in the way thermoset polymers are perceived and utilized.
Sustainable Materials and Bio-Based Resins
Sustainability is a pressing issue in today's world. The increasing awareness of environmental degradation prompts researchers to explore sustainable materials in polymer production. Bio-based resins leverage renewable resources, leading to a reduction in dependency on fossil fuels. These resins can be derived from various biomass sources, such as corn, soy, and other plant-based materials.
A significant advantage of utilizing sustainable materials is the lower carbon footprint they offer. For instance, bio-based epoxy resins maintain comparable properties to traditional petroleum-derived options while being less harmful to the ecosystem. Furthermore, the adoption of these materials can meet consumer demands for greener products.
Challenges remain, including cost and availability of raw materials. However, the potential benefits clearly underscore the importance of continual research in this domain.
Smart Thermoset Polymers
Smart thermoset polymers represent another exciting advancement. These materials possess the ability to respond to external stimuli, such as heat, light, or electricity. Their incorporation into various applications can lead to improved performance and functionality. For example, thermoset polymers can be engineered to change shape or properties upon exposure to temperature, making them suitable for self-healing applications.
This adaptability opens new avenues in fields like aerospace and automotive design, where reliability and performance are critical. The inclusion of smart functionalities culminates in enhanced safety features and increased product longevity. Nonetheless, the complexity of smart material development requires extensive research and rigorous testing.
Nanocomposites in Thermosetting Resins
Nanocomposites are another innovative approach being integrated into thermosetting resins. By incorporating nanoscale fillers such as clay, carbon nanotubes, or graphene, these composites demonstrate significantly enhanced properties. Improvements include increased strength, thermal stability, barrier properties, and resistance to wear.
For example, the addition of nanomaterials can enhance the overall mechanical performance of epoxy resins, making them more suitable for extreme conditions. Moreover, nanocomposites can facilitate lighter products without sacrificing strength, which is crucial for industries like automotive and aerospace.
However, the dispersion and compatibility of nanoparticles in thermoset matrices can pose challenges. Proper processing techniques and formulation are necessary to achieve the desired performance without compromising workability.
The advancements in thermoset technology have the potential to shape a sustainable and smarter future for materials science, offering vast opportunities for efficiency and innovation.
Future Outlook for Thermoset Polymers
The future outlook for thermoset polymers is a vital aspect of material science and engineering today. These materials are known for their durability, heat resistance, and chemical stability. As industries evolve and demand new materials for specialized applications, the development and innovation surrounding thermoset polymers will play a significant role. This section will evaluate current market trends, sector projections, and the exciting potential for interdisciplinary research.
Market Trends and Projections
The market for thermoset polymers has shown consistent growth over the past few years. Leading sectors, particularly automotive, aerospace and electronics, continue to drive demand. Here are some notable trends that illustrate the current direction of thermoset polymers:
- Increasing Demand for Lightweight Materials: With a global shift towards fuel efficiency and sustainability, there is a rising trend for lightweight composites. Thermoset polymers can provide strength without adding excessive weight, making them ideal for automotive and aerospace industries.
- Sustainability Initiatives: Many companies are now focused on producing sustainable materials. Expanded interest in bio-based resins is driving innovations that align with environmental standards. Many manufacturers are integrating recycling processes to lessen waste production in their thermoset applications.
- Technological Advancements: Advancements in manufacturing technology, like 3D printing, have encouraged innovation within the thermoset polymer market. New fabrication techniques allow for more complex designs and structures that were previously unattainable.
Projections indicate that the thermoset polymer market will continue to flourish in the coming years, with estimates of significant annual growth rates. These materials will remain at the forefront of engineering solutions.
Potential for Interdisciplinary Research
Interdisciplinary research holds immense potential in advancing the field of thermoset polymers. The collaboration among various scientific disciplines can foster new insights and innovations. Here are a few important areas where such research can contribute:
- Material Chemistry: Understanding the molecular properties of thermosetting resins can lead to the formulation of new materials with tailored characteristics. This includes enhancing thermal resistance or improving mechanical properties.
- Nanotechnology: The integration of nanomaterials can enhance the performance of traditional thermoset polymers. By embedding nanoscale materials into polymers, researchers aim to improve properties like toughness, conductivity, and flame resistance.
- Environmental Science: Innovations in developing eco-friendly thermosetting materials should be prioritized. Research focused on biodegradable thermosets or those derived from renewable resources supports sustainability goals.
Finale
The conclusion of this article underscores the pivotal role that thermoset polymers play in various sectors. This closing section encapsulates the key insights that have been explored throughout the article. The importance of thermoset polymers lies not only in their distinct chemical properties but also in their practical applications across diverse industries. These materials provide high strength, durability, and resistance to various environmental factors, making them indispensable in environments that demand reliable performance.
Summary of Key Points
In summarizing the discussions, several critical points emerge:
- Definition and Characteristics: Thermoset polymers are irreversible materials, characterized by a cross-linked structure that provides them with unique mechanical properties.
- Manufacturing Techniques: The processes including compression molding and resin transfer molding are essential for producing complex shapes and components.
- Applications: Their use spans multiple industries, from automotive to aerospace, highlighting their versatility.
- Advantages and Limitations: While they offer benefits such as durability, they do have limitations regarding recyclability and brittleness, which can impact their long-term usage.
- Innovative Developments: Recent advancements showcase a trend towards sustainability with bio-based resins and the integration of smart materials.
Final Thoughts on Thermoset Polymers
Considering the trajectory of material science, thermoset polymers are positioned as vital components in the future of engineering and manufacturing. Their unique properties make them suitable for an array of applications, driving innovation across technology and product design. The ongoing research and development in this field suggest a powerful potential for integrating these materials into new applications, particularly where high performance in demanding conditions is necessary.
Understanding thermoset polymers equips researchers, students, and industry professionals with the necessary knowledge to leverage these materials effectively. As sustainability becomes a growing concern, the development of eco-friendlier options within thermoset technology will likely reshape their market and roles in future innovations. As such, addressing both the advantages and limitations will be essential for making informed decisions in material selection and application.