Comprehensive Analysis of Gear Drives: Principles & Trends
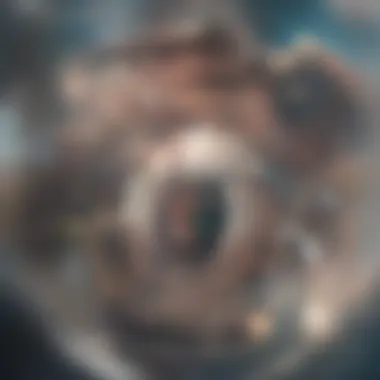
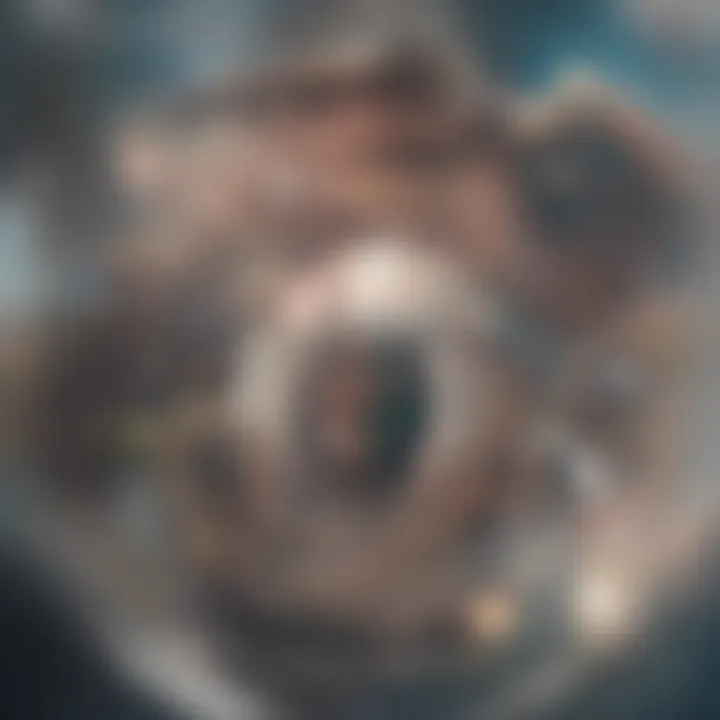
Intro
Gear drives are essential components in various mechanical systems, enabling efficient power transmission and torque multiplication. This article will provide a thorough understanding of gear drives, focusing on their principles of operation, diverse applications in different industries, advantages and disadvantages, and the latest trends in technology. The examination will appeal to engineers, researchers, educators, and industry professionals who seek a comprehensive view of gear systems.
Beneath the surface, gear drives feature complexities that warrant an in-depth exploration. Fundamental principles such as gear ratios, types of gearing, and design considerations affect performance and efficiency. Additionally, the applications in sectors ranging from automotive to manufacturing reveal the versatility of these systems. As technology evolves, understanding the future trends in gear drive development becomes crucial for innovation and improved performance in engineering solutions.
An accurate analysis includes well-grounded information about materials, design innovations, and maintenance practices that ensure longevity and efficiency of gear systems. The objective of this article will be to meld technical details with practical applications, thus providing value to our discerning readership.
Prologue to Gear Drives
Understanding gear drives is crucial in the field of mechanical engineering and related applications. Gear drives are integral components that facilitate the transmission of power and motion in a variety of machines. They serve to modify the torque and speed of rotating shafts, making them vital in numerous industrial contexts.
The efficiency and functionality of machines often rest upon the design and implementation of gear drives. Their ability to connect different mechanical elements ensures that energy is transmitted smoothly and effectively. Furthermore, gear drives play a significant role in enhancing the performance of devices in sectors such as automotive, aerospace, and manufacturing.
Definition and Purpose
Gear drives are mechanical devices that transmit rotational motion and power between shafts using gears. They convert input speed and torque into output speed and torque, allowing machines to operate effectively. The primary purpose of gear drives is to adjust the speed and torque levels to meet the requirements of specific tasks, thereby optimizing performance.
Gear drives can be classified based on torque, speed, and direction of rotation, catering to various applications. They can either increase torque and decrease speed or vice versa, depending on the gear ratio. This adaptability is essential for multiple functions, from simple machines to complex industrial systems.
History of Gear Drives
The history of gear drives dates back thousands of years. Evidence suggests that gears were used in ancient Greek and Roman devices. They were initially used in simple machines for lifting heavy objects and for water mills.
As time progressed, the design and manufacturing of gears evolved significantly. The invention of the gear-cutting machine in the late 18th century marked a turning point in producing precise gears, leading to the complex gear systems we see today.
The Industrial Revolution further propelled the development of gear drives, with innovations in materials and manufacturing processes providing the foundation for modern applications. Advances such as computer-aided design (CAD) and CNC machining have enabled the production of highly accurate and efficient gear drives. Today, gear drives are ubiquitous in various machinery, illustrating their enduring importance in mechanical engineering.
Basic Principles of Gear Transmission
Understanding the basic principles of gear transmission is crucial for anyone working with mechanical systems. Gear drives are fundamental components in many engineering applications, playing a pivotal role in transferring power and motion effectively. The principles underlying gear transmission influence performance metrics such as torque, speed, and overall system efficiency. By grasping these concepts, engineers can make informed decisions about design choices that align with specific operational requirements.
Fundamentals of Torque and Speed
Torque and speed are two of the primary metrics to consider in gear systems. Torque can be defined as the measure of rotational force being applied, while speed indicates how quickly something is rotating. An essential aspect of gear drives is the relationship between these two factors. When gears are paired, the torque applied to one gear affects the speed of the connected gear and vice versa. It is important to note that gear ratios significantly determine how these elements interact. A higher gear ratio often results in increased torque but decreased speed, while a lower ratio allows for higher speeds at the cost of torque.
Types of Gear Teeth
Gear teeth standards play an integral role in how gears function. Each type of gear tooth is designed for specific applications and offers distinct characteristics.
Spur Gears
Spur gears are one of the most common types of gear teeth. They have straight teeth and are mounted parallel to the shaft. The primary advantage of spur gears is their simplicity, which allows for efficient power transmission. They are well-suited for applications requiring high-speed rotation but are less effective at high loads due to the likelihood of wear and tear. Because of their straightforward manufacturing process and cost-effectiveness, they remain a popular choice in various mechanical assemblies.
Helical Gears
Helical gears have teeth that are cut at an angle to the axis of rotation. This configuration allows for smoother engagement between gears, which leads to quieter operation. They are often used in applications where load capacity and efficiency are critical. However, the angled teeth may introduce axial thrust, potentially requiring additional support mechanisms. Despite this, their capacity for handling heavy loads and high speeds makes them favorable in many industries.
Bevel Gears
Bevel gears are unique in that they allow for power transmission between shafts that intersect at an angle, commonly set at 90 degrees. This orientation makes them advantageous in applications that require directional change. The key characteristic of bevel gears is their ability to maintain efficiency across varying angles. However, they do require precision in manufacturing, which can increase costs compared to straight-cut gears.
Worm Gears
Worm gears are notable for their distinctive design, consisting of a worm (a screw-like gear) that meshes with a worm wheel (similar to a regular gear). This configuration allows for significant reduction in speed and increase in torque. It is widely used for applications requiring a high gear ratio in a compact space. However, the typical drawback of worm gears is their lower efficiency, as a large amount of power may be lost to friction.
In summary, understanding the various types of gear teeth and their implications is essential for optimizing gear drive performance. Each type has its own merits and limitations, and the choice of gear system should align with specific application needs.
Classifications of Gear Drives
In the realm of gear drives, classifications serve as a fundamental framework for understanding different gear systems and their functionalities. Each classification illuminates unique attributes and operational principles that can align with specific application needs. Understanding these classifications can significantly enhance the design, function, and efficiency of various mechanical systems. Recognizing the distinctions among different gear drive types enables engineers and technicians to make informed decisions in selecting the appropriate system for a particular task.
Straight vs. Reduction Gear Drives
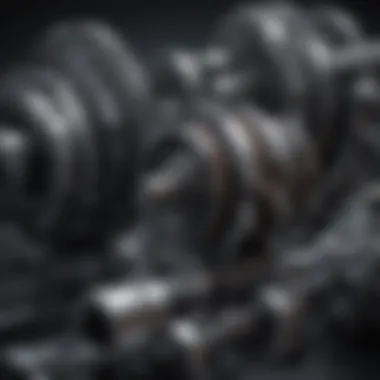
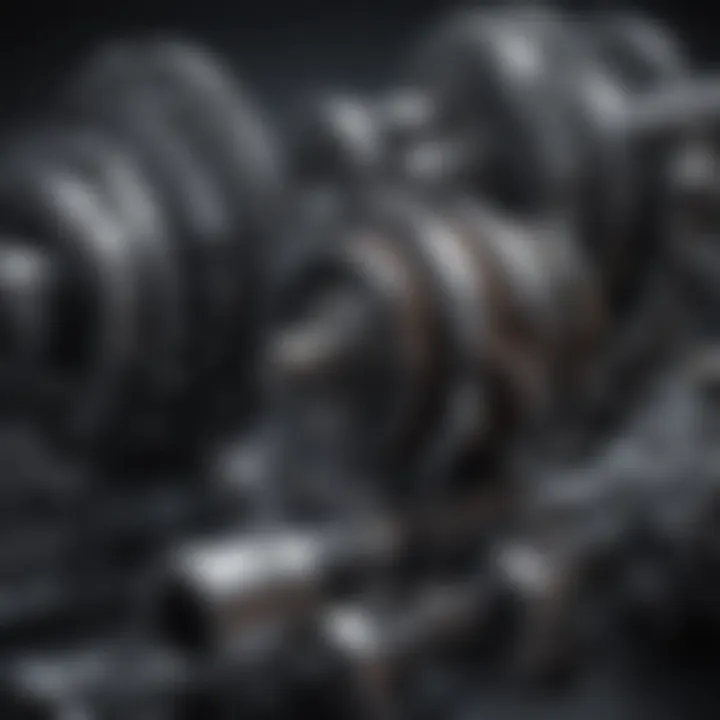
Straight gear drives typically refer to systems that aim for direct transmission of power, maintaining a 1:1 ratio without altering speed or torque. They are commonly utilized in scenarios that require the mechanical input speed to equal the output speed. By contrast, reduction gear drives modify the output speed, decreasing it while simultaneously increasing the torque available at the output shaft. This characteristic makes reduction gear drives pivotal in applications involving heavy machinery, where higher torque is essential for efficient performance.
Considerations when choosing between straight and reduction gear drives include:
- Efficiency needs: Straight gear drives may be favored when high efficiency is necessary, while reduction drives are better for torque applications.
- Space constraints: Reduction gear drives can occupy more space due to additional components.
- Cost implications: Generally, reduction gear drives may entail higher initial costs due to their complexity.
Epicyclic Gear Drives
Epicyclic gear drives, often recognized for their compact design, employ a unique arrangement where one or more gears rotate around a central gear. This configuration allows for high power density and a wide range of gear ratios within a compact size. The designs are advantageous for applications that require space savings and efficiency is paramount.
Key elements include the following:
- Mechanical Advantage: Epicyclic systems typically offer a mechanical advantage by placing multiple gears on the same axis.
- Load Distribution: They can distribute loads more evenly across gears, improving the lifespan and reliability of the system.
- Applications: Commonly found in automatic transmissions in vehicles, they offer smooth and efficient gear shifting.
Planetary Gear Drives
Planetary gear drives are a subset of epicyclic drives. They consist of a central sun gear, planet gears that orbit the sun gear, and an outer ring gear. This arrangement allows for efficient torque transfer and high performance. The versatility of planetary gears makes them suitable in applications where space and efficiency are critical considerations.
Factors to evaluate when dealing with planetary gear drives include:
- Backlash Control: These systems can be designed with minimal backlash, enhancing precision in motion.
- Durability: The multi-faceted arrangement equally distributes stresses, which can result in longer operational life.
- Deployment: They are used in robotics, aerospace, and automotive applications where reliability and compactness are crucial.
In summary, understanding the classifications of gear drives, from straight to reduction gear drives, and delving into the specifics of epicyclic and planetary systems allows for enhanced selection of gear systems tailored to various applications. This knowledge can greatly influence the performance, efficiency, and practicality of mechanical assemblies.
Applications of Gear Drives
The significance of gear drives within various sectors cannot be understated. Gear drives provide multiple advantages, such as efficient power transmission, compact design, and adaptability. Their applications span across industries, enabling machinery and systems to operate with optimal performance. By examining the specific domains where gear drives are applied, one can appreciate their essential role in modern technology and engineering.
Industrial Applications
In industrial settings, gear drives are crucial in manufacturing processes. They power conveyor systems, pumps, and compressors. These drives can transform the high-speed rotations from motors into the necessary lower-speed, high-torque output. This transformation is vital. It ensures that heavy materials are moved effectively.
Common gear types in this sector include helical and spur gears. These types are selected based on load requirements, efficiency, and space constraints. Moreover, gear drives enable automation, enhancing productivity and precision in processes.
Transportation
Transportation systems heavily rely on gear drives for efficient energy transfer. Automotive vehicles use gear drives in their transmissions. This ensures effective control over speed and torque. In trains, gear drives help in accelerating and decelerating safely.
The precision of gear ratios in these applications significantly impacts fuel efficiency and performance. Electric vehicles also utilize gear drives to optimize energy consumption. The transition toward electric mobility highlights the importance of gear drives in future transportation technologies.
Robotics and Automation
Robotics and automation represent a rapidly growing area where gear drives are indispensable. In robotic arms and automated manufacturing cells, gear drives provide the articulation necessary for precise movement and control.
The adaptability of gear drives allows designers to customize systems based on the robotic application's requirements. Gear drives help in scaling down motor output thus increasing work efficiency. They also contribute to the reduction of weight, which is critical in robotic systems that may need to move quickly.
Renewable Energy Systems
Gear drives play a pivotal role in renewable energy systems, especially in wind turbines. In this setting, they convert the variable rotational speed of turbine blades into a consistent output for generators.
The design and material selection of these gear systems are vital. They must endure various stressors while maintaining efficiency. As the push for sustainable energy increases, innovations in gear drive technology need to keep pace.
"The integration of advanced gear drive systems in renewable sectors can significantly improve overall efficiency and reliability."
The advancements in gear design may greatly influence future energy systems. Overall, the continuous evolution of gear drives is essential for enhancing efficiency and effectiveness across these sectors.
Advantages and Disadvantages of Gear Drives
Understanding the advantages and disadvantages of gear drives is essential for engineers and industry practitioners. This section aims to provide a balanced view of the benefits and considerations that come with using gear drives in various applications. Gear drives are significant in many mechanical systems, as they contribute to performance, reliability, and efficiency. However, they are not without downsides that require careful evaluation.
High Efficiency
Gear drives are known for their high efficiency in transmitting power. They can achieve efficiencies of 90% to 98% under optimal conditions. This is important for minimizing energy loss during transmission, which can lead to reduced operational costs and enhanced performance. The reduction in energy consumption becomes increasingly critical in environments aiming for sustainability.
Factors that contribute to the high efficiency include:
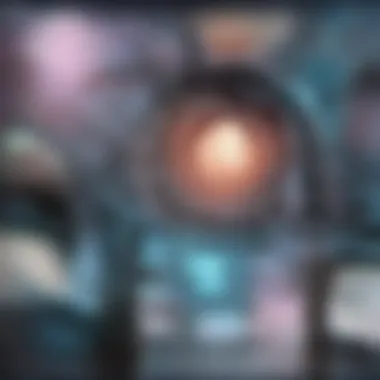
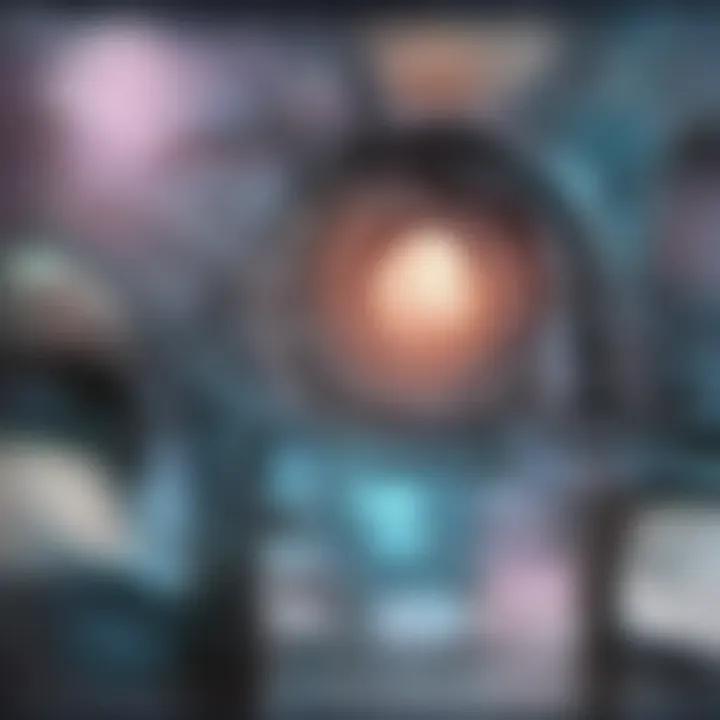
- Minimal slippage: Direct contact between gear teeth leads to effective torque transmission.
- Low friction: Well-lubricated gears can operate at lower friction levels, preserving energy during operation.
- Precision design: Gear fabrication techniques provide accuracy, essential for maintaining operational efficiency.
The gains from high efficiency can tip the scale when choosing power transmission systems, especially in applications demanding reliability and performance.
Compact Design
Another notable advantage of gear drives is their compact design. Compared to belt and chain systems, gear drives occupy less space and provide a more straightforward arrangement. This compactness allows engineers to create smaller, more efficient machines without compromising performance.
Some reasons behind the compact design of gear drives are:
- Integration flexibility: Gears can be arranged in various configurations, fitting into tight spaces.
- Lower weight per unit power: Gear systems can produce high output in a lighter frame, addressing weight concerns in automotive and aerospace applications.
- Simplified installation: Compact gear drives are often easier to install, allowing for faster implementation in machinery.
Wear and Tear Considerations
While gear drives present several advantages, the wear and tear associated with them is a critical consideration. Constant engagement and movement lead to inevitable wear over time. This can degrade performance, create operational noise, and require maintenance. Various factors can influence wear, such as:
- Material properties: Different materials exhibit varying resistance to wear. Selecting appropriate materials can mitigate some issues.
- Operating conditions: Temperature fluctuations, lubrication quality, and external contamination influence the wear rate.
- Design flaws: Improper design or installation can lead to premature wear of gears.
Attention to wear and tear will optimize the lifespan of gear drives and maintain operational efficiency.
Noise and Vibration Issues
Gear drives can generate noise and vibration due to the nature of their operation. These issues often arise from:
- Interaction of gear teeth: The meshing process can create vibrations and resulting noise, which may be undesirable in certain applications, such as automotive and industrial machinery.
- Imbalance: If gears are not properly balanced, they can lead to increased vibrations, affecting overall performance.
- Wear and misalignment: Over time, wear and misalignment of gears can exacerbate noise problems and may necessitate intervention.
Mitigating noise and vibration can involve better design, correction of misalignment, and proper lubrication practices.
"When designing a gear drive system, consideration of both benefits and potential drawbacks is crucial for achieving optimal performance."
Design Considerations for Gear Drives
Design considerations are at the core of effective gear drive functionality. Proper design ensures the optimal performance of gear systems and addresses various operational challenges. This section explores the critical elements involved in design considerations for gear drives, focusing on material selection, load capacity and strength, and lubrication and cooling strategies. Each aspect plays a significant role in enhancing overall efficiency, durability, and reliability in the application of gear drives.
Material Selection
Material selection is a fundamental aspect of gear drive design. The choice of material affects the strength, wear resistance, and overall performance of the gear system. Typically, steel and cast iron are common materials due to their high strength and durability.
When considering materials, it is essential to analyze the following factors:
- Load requirements: The material must withstand the operational forces during the gearβs life cycle.
- Environmental conditions: Materials must be selected based on exposure to factors such as moisture, temperature, and corrosive elements.
- Manufacturing capabilities: The material should be compatible with available manufacturing processes, such as forging or machining.
Using advanced materials, like titanium or composite materials, can offer benefits. They often provide lighter mass and enhanced performance characteristics but can be more expensive.
Load Capacity and Strength
Load capacity and strength are critical factors impacting the design of gear drives. A gear drive must be capable of handling the anticipated load without failing. Understanding the forces involved ensures that the gear design meets operational demands.
Key elements include:
- Torque considerations: The gear must transmit the required torque efficiently.
- Stress analysis: Application of theoretical principles to predict how the gear will behave under provided loads. This may involve factors like bending stress and tooth shear.
- Safety margins: Incorporating safety factors into design helps accommodate unexpected overload situations.
Designers often use simulation techniques to visualize the load distribution on gears. This predictive capability informs adjustments in design to enhance performance.
Lubrication and Cooling
Lubrication and cooling are vital to maintaining the performance of gear drives. Adequate lubrication minimizes friction and wear, prolonging the lifecycle of the gear system. It also plays a role in heat dissipation, as excessive heat can compromise gear integrity and efficiency.
Important points to consider include:
- Type of lubrication: Manufacturers can choose between oil, grease, or dry lubrication depending on operational requirements. Each type presents distinct advantages and disadvantages.
- Cooling systems: In applications where high loads and speeds occur, additional cooling systems may be necessary. Utilizing forced air or liquid cooling can mitigate heat build-up.
- Regular maintenance: Implementing a routine maintenance schedule for checking lubricant levels can prevent premature wear and gear failure.
"Proper lubrication practices significantly extend the lifespan of gear systems, ensuring reliability in operations."
Maintenance of Gear Drives

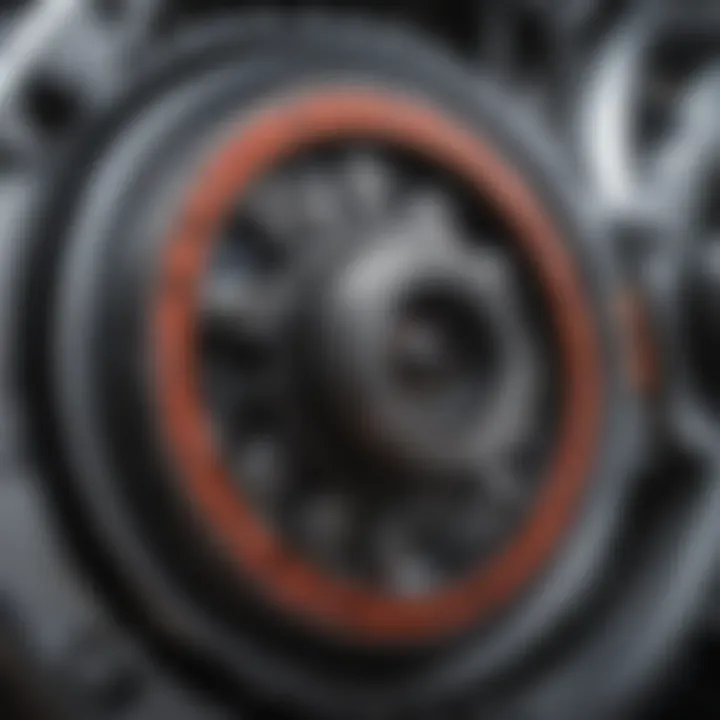
The maintenance of gear drives is a crucial aspect that can significantly affect their performance and lifespan. Regular maintenance ensures that these systems operate efficiently while minimizing the risk of breakdowns. By focusing on the key components of maintenance, engineers and technicians can enhance reliability and reduce downtime. This section delves into three primary aspects of maintenance: routine inspections, lubrication practices, and common failure modes.
Routine Inspections
Routine inspections are essential for early detection of potential issues in gear drives. By assessing the condition of the gears and related components regularly, one can identify wear and tear before it results in significant failures. Inspections should be performed as part of a scheduled maintenance plan. The main elements to check during these inspections include:
- Visual Examination: Look for signs of oil leaks, abnormal wear patterns, or any noise that deviates from normal operation.
- Gear Alignment: Ensure that gears are properly aligned to prevent unnecessary load and stress.
- Play and Backlash: Measure the play and backlash to detect misalignment or deterioration.
Implementing an effective inspection routine can decrease repair costs and contribute to longer equipment life. By investing time in regular checks, companies can minimize unexpected downtimes and service interruptions.
Lubrication Practices
Lubrication is pivotal in ensuring smooth operation of gear drives. It reduces friction, minimizes wear, and dissipates heat generated during operation. Proper lubrication practices include:
- Selection of Appropriate Lubricants: Different types of gear drives require specific lubricants. Choosing the right grade and type is critical.
- Regular Lubrication: Create a timeline for re-lubricating equipment based on operating conditions and manufacturer recommendations.
- Monitoring Lubricant Condition: Keep track of the lubricant's age and condition. Contaminated or degraded lubricant can cause damage rather than prevent it.
Understanding lubrication practices and applying them diligently helps in maintaining the performance and extending the lifetime of gear drives. A well-lubricated system is less prone to wear and can operate under heavier loads.
Common Failure Modes
Understanding common failure modes in gear drives is vital for implementing effective maintenance strategies. Some of the common issues include:
- Tooth Fracture: Results from excessive loads or material defects, leading to gear tooth failure.
- Bearings Failure: Insufficient lubrication or misalignment can result in bearing damage, creating operational disruptions.
- Gear Tooth Wear: Gradual degradation of gear teeth due to contact stresses, dirt, or poor lubrication.
- Overheating: Can result from inadequate cooling or lubrication, leading to significant long-term damage.
Awareness of these potential failure modes allows maintenance teams to implement proactive measures, further enhancing system reliability.
"Regular maintenance not only prolongs the life of gear drives but also ensures optimal performance and reduces the risk of costly downtime."
Future Trends in Gear Drive Technology
The evolution of gear drive technology is crucial for enhancing mechanical efficiency and productivity across various industries. Understanding the potential future trends is essential for engineers and industry professionals. These trends include the integration of digital technologies, sustainable design practices, and advanced material utilization. Each of these trends holds significance in addressing contemporary engineering challenges and improving the lifespan, reliability, and performance of gear systems.
Smart Gear Drives
Smart gear drives represent a paradigm shift in how gear systems are monitored and controlled. By incorporating sensors and IoT technology, these drives allow for real-time data collection and analysis. The benefits of smart gear drives include:
- Predictive Maintenance: Continuous monitoring enables early detection of potential failures, reducing downtime and maintenance costs.
- Enhanced Performance: Real-time feedback can optimize performance, adjusting parameters such as torque and speed, ensuring the system operates efficiently.
- Integration with Industry 4.0: Smart gear drives fit within the larger framework of smart manufacturing, promoting automation and interoperability of machinery.
The trend towards smarter gear drives is likely to increase, driven by the need to improve operational efficiency and reduce operational risks.
Sustainability in Gear Design
Sustainability has become a central theme in engineering. Gear design must now prioritize environmental impact while maintaining performance. Key considerations in this area include:
- Material Selection: Using recyclable and environmentally friendly materials can minimize waste and promote sustainability.
- Energy Efficiency: Developing gear systems that reduce energy consumption can contribute significantly to carbon footprint reductions.
- Lifecycle Analysis: Designing for durability and efficiency throughout the product lifecycle not only benefits the environment but also reduces costs associated with material consumption.
As organizations face more stringent environmental regulations and consumer demand for sustainable products, gear designs will likely evolve to meet these challenges.
Advanced Materials and Manufacturing Techniques
Advancements in materials and manufacturing techniques are shaping the future landscape of gear drives. Innovations in material science have introduced lightweight yet strong materials such as composite materials and advanced alloys. These materials offer:
- Increased Strength-to-Weight Ratio: Lighter gear drives can lead to improved efficiency and performance in various applications.
- Improved Wear Resistance: Advanced materials can withstand harsher operating conditions, extending the lifespan of gear systems.
- Additive Manufacturing: Techniques such as 3D printing allow for more complex designs that were previously unachievable. This not only reduces waste but also can lead to rapid prototyping and design customization.
Closure
In concluding this comprehensive analysis of gear drives, it is essential to reflect on the significance and impact of this technology on various industries. Gear drives play a crucial role in ensuring mechanical efficiency and reliability in systems ranging from simple machines to complex automated processes. Understanding the design, maintenance, and future trends of gear drives equips engineers and industry professionals with the knowledge to optimize their applications. This article has aimed to dissect many aspects of gear drives, showcasing the versatility and importance they hold.
One of the key benefits of understanding gear drives is the ability to select the right type for specific applications. It is vital in industries such as automotive, aerospace, and renewable energy, where precision and reliability are non-negotiable. By considering the advantages and disadvantages presented, professionals can make informed decisions that will enhance operational efficiency and sustainability.
Additionally, the exploration of innovative designs and materials opens new avenues for advancements in gear technology. Future trends indicate a movement toward smarter gear drives, integrating IoT capabilities that can facilitate real-time monitoring and adjustments for optimal performance. Moreover, sustainability in design processes is becoming a critical focus as industries strive to minimize their environmental impact.
In summary, the information presented throughout this article emphasizes the need for robust knowledge around gear drives, their applications, and their future developments. This will ensure that professionals can keep pace with technological advancements, enhancing productivity in their respective fields.
Key Takeaways
- Significance of Gear Drives: Gear drives are vital for efficiency and reliability in machinery across various industries.
- Application Context: Understanding different types of gear drives helps in selecting the best option for specific applications.
- Innovation and Sustainability: Future trends point towards smarter designs and sustainable practices.
- Informed Decisions: Knowledge about the advantages and disadvantages aids in making informed decisions that enhance operational efficiency.
"Innovations in gear drive technology not only improve efficiency but also pave the way for sustainable advancements in engineering."
By keeping these points in mind, students, researchers, educators, and professionals can better appreciate the complexities of gear drives and apply this knowledge practically.