Comprehensive Guide to CNC Machining Principles
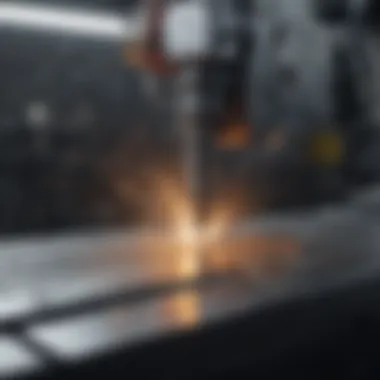
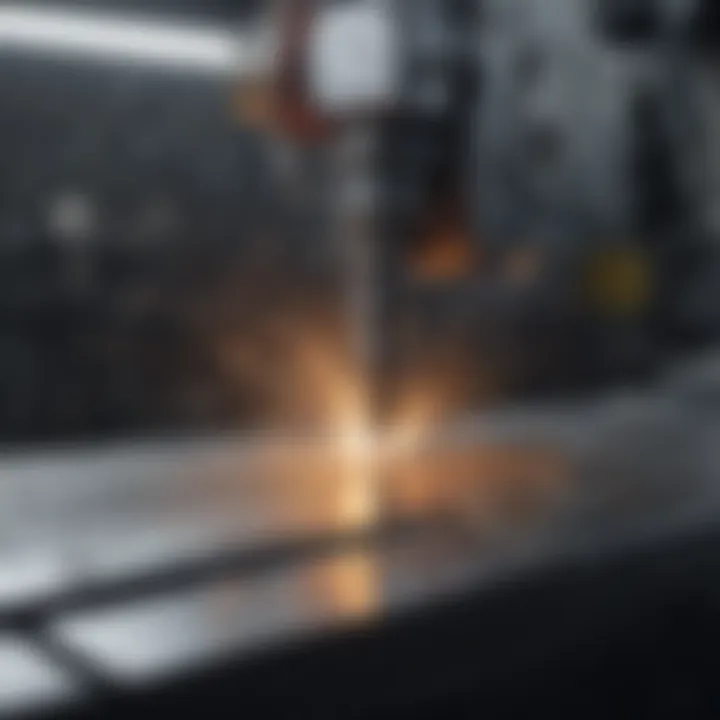
Intro
Computer Numerical Control (CNC) machining has revolutionized the manufacturing sector in recent decades. It combines precision, efficiency, and automation, leading to enhanced productivity across various industries. With its origins tracing back to the 1950s, CNC machining employs computer-generated commands to control machine tools. This approach not only streamlines the manufacturing process but also improves the quality and repeatability of produced parts.
As we explore CNC machining, this article will highlight its fundamental principles, the mechanics behind the technology, and its vast array of applications. The continuous advancements in this field have made it crucial for professionals and students to understand the core aspects surrounding CNC technology.
Key Findings
CNC machining is characterized by several significant observations:
- Precision and Accuracy: CNC machines offer remarkable precision, often achieving tolerances within a few microns. This precision is vital for sectors where even minor deviations can result in major failures.
- Automation and Productivity: Automation in CNC machining leads to higher productivity rates. Machines can run for extended periods without human intervention, thus reducing the time required for production.
- Flexibility: CNC systems can be reprogrammed easily, enabling manufacturers to switch between different production tasks without significant downtime.
- Complex Design Capabilities: The technology allows for the production of complex shapes and designs that traditional machining methods struggle to achieve.
Major Results
The results derived from similarly conducted studies and analyses indicate that:
- Reduction in Manufacturing Costs: The precision of CNC machining reduces waste and materials, thus lowering overall costs.
- Enhanced Worker Safety: Automation reduces the risks associated with manual machining processes.
- Increased Customization: As companies continue to shift towards personalized products, CNC machines are invaluable in creating custom parts quickly and effectively.
Discussion of Findings
The findings demonstrate that the impact of CNC machining extends far beyond mere productivity. It reshapes how products are designed, produced, and delivered. Integration of various software and programming languages facilitates better design-to-production transitions, leading to enhanced market responsiveness.
Moreover, with continuous advancements like additive manufacturing also influencing CNC technologies, it is pertinent to examine how these changes affect the landscape of precision manufacturing.
Methodology
Research Design
This article synthesizes peer-reviewed studies, technical articles, and industry reports. The emphasis is on reviewing empirical research regarding the effectiveness of CNC machining in modern manufacturing. Direct case studies are also referenced to underline practical implementations of CNC in various sectors.
Data Collection Methods
Data for this exploration was gathered through:
- Analysis of industry reports from sources such as the National Institute of Standards and Technology.
- Literature review from academic journals focusing on manufacturing technology and developments.
- Surveys conducted with professionals who actively engage with CNC technology in their workflows.
Intro to CNC Machining
Computer Numerical Control (CNC) machining has transformed the landscape of manufacturing. Understanding CNC machining is crucial for recognizing how modern industries operate and innovate. CNC machining involves the use of computers to control machine tools. This integration allows for automation, precision, and efficiency in producing parts and products.
The significance of this technology can be observed across various sectors. From aerospace to medical devices, CNC machining provides the ability to produce intricate components with remarkable accuracy. The benefits are substantial; CNC machines can work continuously, allowing for higher production rates without sacrificing quality.
In this article, we explore the core aspects of CNC machining to provide insights into its relevance and implications. The journey begins with the history and development of CNC technology, shedding light on how it has reached its current state. In understanding its evolution, one can appreciate the advancements it has enabled in manufacturing processes today.
Definition and Evolution of CNC Technology
CNC technology refers to the automated control of machining tools via computer systems. This approach allows precise manipulation of tools based on pre-programmed computer codes. At its core, G-code, a type of programming language, serves as the primary method for instructing CNC machines.
The evolution of CNC technology began in the 1940s. Early forms of numerical control relied on punched tape and mechanical systems to direct tools. The transition to computerized systems occurred in the 1960s. This shift marked a pivotal moment, enabling more complex designs and a greater range of machine capabilities.
As we look at the advancements over the decades, several key milestones emerge:
- Introduction of CAD/CAM: The integration of Computer-Aided Design (CAD) and Computer-Aided Manufacturing (CAM) revolutionized design processes, making it easier to create elaborate designs that can be directly translated into machine instructions.
- Software Developments: Improvements in software capabilities have led to better simulations and optimization, allowing engineers to test designs virtually before physical production.
- Machine Enhancements: CNC machines have grown more sophisticated, incorporating multi-axis functionality that allows for more complex shapes and cuts, catering to diverse industries.
"CNC machining represents a leap towards precision engineering, making it integral to modern manufacturing practices."
Overall, the definition and evolution of CNC technology underscore its importance in today’s industrial landscape. Understanding this evolution is crucial for comprehending the current capabilities and future potential of CNC machining.
Fundamentals of CNC Operations
Understanding CNC operations is critical to grasping how modern manufacturing techniques have advanced. This section breaks down the essential elements that form the backbone of CNC technology and explains their significance. Mastering these fundamentals can lead to greater efficiency, precision, and innovation within various industrial applications.
Core Components of CNC Machines
CNC machines consist of several core components that work together to achieve high levels of accuracy and repeatability. Understanding these parts is vital for anyone looking to engage with CNC technology.
- Control Unit: This component acts as the brain of the CNC machine. It interprets the G-code and translates it into movements that the machine must execute.
- Drive Mechanisms: These are essential for the operational functionality. They convert the data from the control unit into precise movements, often involving motors or servos.
- Feedback System: This system ensures that the machine is performing according to the programmed commands. It typically includes sensors and encoders to provide real-time data about the position and speed of the machine.
- Cutting Tools: The choice of cutting tools affects the quality and speed of the machining process. Different tools are employed based on material properties and desired outcomes.
- Workpiece Table: This part holds the material to be machined securely in place. It's crucial that this component allows for flexibility and stability in various machining operations.
- Software Interface: The software enables operators to program CNC machines effectively. User-friendly interfaces simplify the complex nature of CNC programming.
Each of these components plays a significant role in ensuring smooth and precise operations. Understanding how they interact allows for optimization in CNC production processes.
The Role of G-code in CNC Programming
G-code is the programming language used to control CNC machines. Knowing its significance is essential for anyone involved in CNC operations.
- Foundation of CNC Programming: G-code commands define every action a CNC machine must take. It instructs the machine on movements, speed adjustments, and tool changes.
- Simplicity and Flexibility: G-code is relatively straightforward to learn and use. Although it requires attention to detail, the fundamentals can be grasped quickly, allowing operators to create effective machine programs efficiently.
- Comprehensive Command Set: G-code includes commands for various tasks such as positioning (G00), linear interpolation (G01), and circular interpolation (G02/G03). Familiarity with these commands enhances programming capabilities.
- Error Minimization: Properly written G-code reduces the chances of errors during machining. It allows for smoother production cycles and ultimately leads to better quality results.
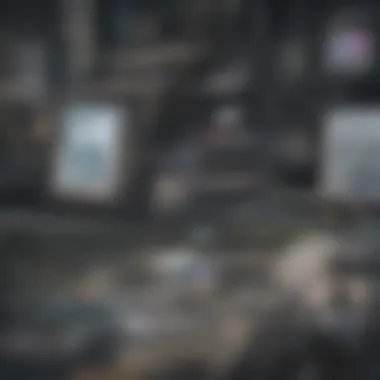
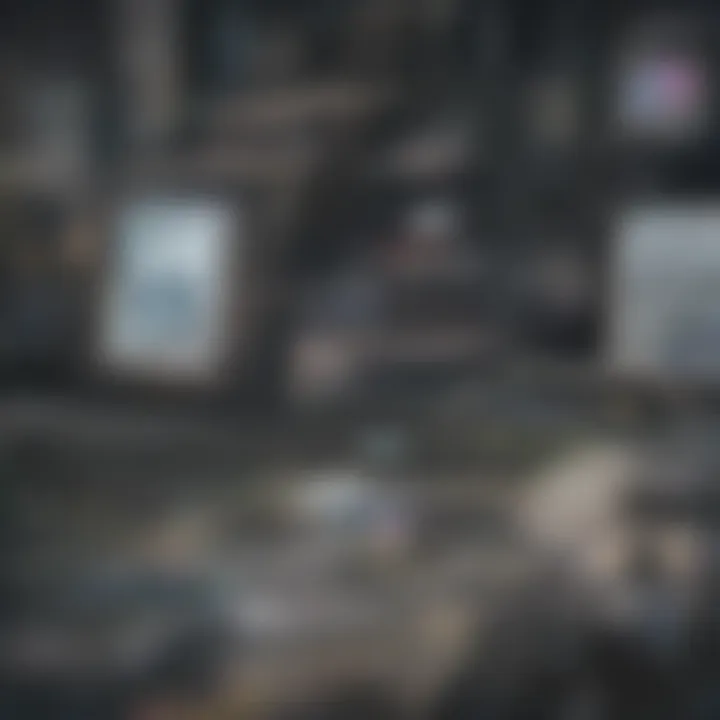
"The efficiency of CNC machining is heavily reliant on the precise programming and operation of its core components, making knowledge of G-code indispensable."
In summary, mastering the fundamentals of CNC operations provides a solid foundation for individuals interested in advanced manufacturing technologies, paving the way for innovation, efficiency, and superior quality in production.
Types of CNC Machines
CNC machines serve various purposes in manufacturing, and understanding the types is crucial. Each machine has specific capabilities, uses, and benefits, making them suitable for different applications. Knowing these types helps users choose the right equipment for their needs, which can significantly impact production quality and efficiency.
CNC Milling Machines
CNC milling machines are versatile and widely used in the manufacturing sector. They operate by rotating a cutting tool against the material. This process allows for precise cutting, shaping, and drilling of a range of materials, including metals and plastics.
Key benefits of CNC mills include:
- High precision: They can produce complex shapes and designs with remarkable accuracy.
- Versatility: These machines are adaptable for different tasks, from simple operations to intricate components.
- Automation: Reduces manual labor, enabling faster production speeds.
Users often consider the size and capabilities when selecting a milling machine. Options range from small desktop models to large industrial machines.
CNC Lathes
CNC lathes specialize in shaping materials by rotating them against a fixed cutting tool. They are primarily used to create cylindrical parts, such as shafts, pins, and fittings.
Benefits of CNC lathes include:
- Efficiency: They can produce many identical pieces quickly.
- Smooth finishes: CNC lathes result in high-quality surface finishes with less need for further machining.
- Ease of use: Once programmed, they can run autonomously, reducing human error and increasing productivity.
Consideration of workpiece size and material is vital in selecting an appropriate CNC lathe.
CNC Routers
CNC routers are specialized for cutting softer materials like wood, plastic, and some metals. They function similarly to milling machines but are typically designed for flat sheet materials.
The importance of CNC routers lies in:
- Customization: They can create unique designs with high precision.
- Production speed: Effective for both small and large production runs.
- Cost-effectiveness: More affordable than some other CNC machines, especially for woodworking industries.
Common applications include signage, cabinetry, and artistic projects, which makes them popular in many workshops.
CNC Plasma Cutters
The CNC plasma cutter uses a high-velocity jet of ionized gas, or plasma, to cut through conductive materials like steel and aluminum.
They are notable for:
- Speed: Plasma cutters are fast, allowing for rapid cutting of thick materials.
- Cost-efficiency: Cheaper than laser cutters, making them accessible for many manufacturers.
- Accuracy: They provide a level of precision suitable for various applications from automotive to decorative metalwork.
Understanding voltage and amperage requirements is important for optimal operation.
3D CNC Printers
3D CNC printers create three-dimensional objects by adding material layer by layer. This technology is increasingly important in various industries, from prototyping to final production runs.
Advantages include:
- Design freedom: They allow for complex geometries that traditional methods may struggle to produce.
- Material variety: A range of materials can be used, from plastics to metals and composites.
- Reduction of waste: Additive manufacturing minimizes scrap material compared to subtractive techniques.
In summary, CNC machines significantly impact production methods and outcomes. Selecting the right type is essential for achieving specific manufacturing goals.
CNC Machining Process
The CNC machining process is a vital aspect of the broader CNC landscape. It encompasses the various stages involved in transforming raw materials into finished products. Understanding this process is crucial for those who aim for efficiency, quality, and precision in manufacturing. With the advent of technology, CNC machining has evolved, allowing for improved outcomes in virtually every industry, from aerospace to consumer goods.
Setting Up a CNC Machine
Setting up a CNC machine is a critical step that requires precision and knowledge. Proper setup includes several essential elements:
- Calibration: Machines must be calibrated to ensure they perform as designed. This involves aligning the cutting tool and setting the reference points.
- Choosing the Right Tool: Different tasks require different cutting tools. Selecting the right one is vital for achieving the desired outcome.
- Loading Programs: Once the setup is complete, the next step is loading the CNC program. This might involve G-code or other programming languages dependent on the machine.
This setup phase lays the foundation for a successful machining operation. Neglecting any of these steps can lead to poor results, wasted materials, and increased costs. Every decision made during setup is significant and can affect final product quality.
Material Selection and Preparation
The choice of material significantly influences the machining process. Several considerations must be taken into account:
- Material Properties: Understanding the properties of materials, such as hardness, tensile strength, and machinability, is crucial. Materials vary widely in how they respond to cutting tools, requiring different approaches.
- Preparation Techniques: Properly preparing materials sometimes involves cutting them to size or applying specific treatments. Improper preparation can lead to difficulties during machining and affect the final result.
- Cost Implications: Material selection often involves balancing quality and costs. Choosing high-quality material may lead to better products but higher expenses.
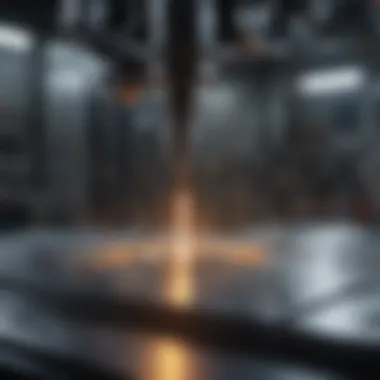
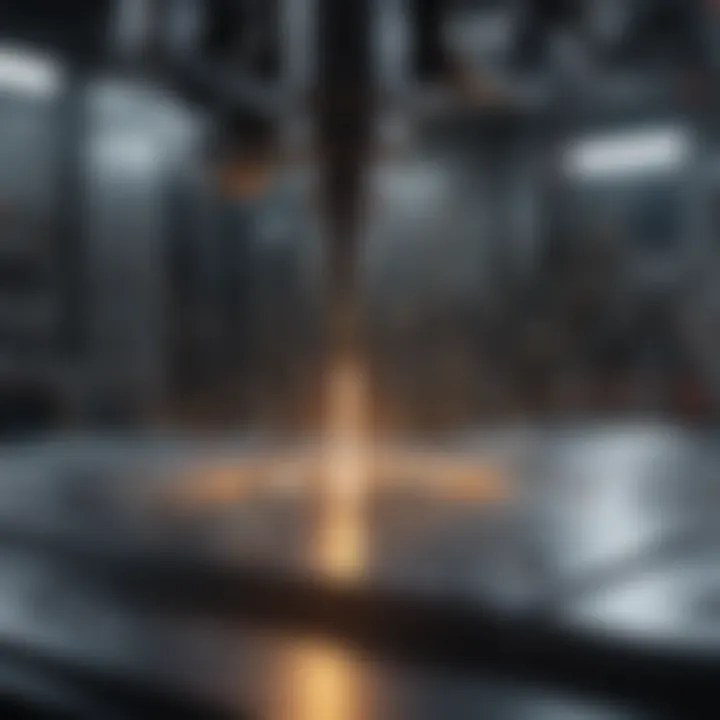
Selecting the right material and preparing it adequately are essential for optimizing machining processes and achieving desired specifications.
Cutting and Finishing Techniques
Cutting and finishing are the heart of CNC machining. Each technique has its specific applications and advantages:
- Cutting Techniques: Various cutting methods exist, such as turning, milling, and drilling. Each technique is suited to specific tasks and materials.
- Finishing Techniques: After the primary cutting process, finishing techniques like sanding or polishing may be required. These steps ensure the final product meets aesthetic and functional requirements.
- Tool Management: Maintaining tools and selecting the appropriate cutting speeds and feeds are vital.
These techniques combined contribute to the precision and quality characteristic of CNC machining. The overall efficiency of the process depends greatly on the skill involved in these techniques.
"The success of CNC machining relies heavily on meticulous processes—setup, material handling, and cutting techniques are all crucial stages that demand attention to detail."
The CNC machining process is a series of careful steps leading from raw material to finished product. Understanding each part can help enhance quality and efficiency in production.
Advantages of CNC Machining
CNC machining stands out in the realm of manufacturing due to its numerous advantages that contribute to better quality and efficiency. Understanding these benefits aids not only industry professionals but also students and researchers in grasping the significance of CNC technology in modern practices. This section will delve into increased precision and consistency, efficiency in production, and reduction of human error.
Increased Precision and Consistency
One of the foremost advantages of CNC machining is its ability to deliver exceptional precision. CNC machines operate through computer numerical control, which allows for exact measurements and movements. This laser focus on detail results in components that meet stringent tolerances. A small error in measurement could lead to significant downstream issues in assemblies or frameworks, which is crucial in fields like aerospace or medical device manufacturing.
Key Aspects of Precision:
- Tight Tolerances: CNC machining can achieve tolerances ranging from +/- 0.001 inches to +/-.0001 inches, depending on the machine and tooling.
- Repeatability: Once a program is set in the CNC machine, it can produce identical pieces with minimal variance. This repeatability is vital in production runs where uniformity is key.
- Quality Control: Many CNC machines include automated checks, ensuring quality through constant monitoring. This utilization of technology underscores the commitment to maintaining high standards throughout the manufacturing process.
"Precision in CNC machining is not just a benefit; it's a requirement in industries where minute discrepancies can have dire consequences."
Efficiency in Production
CNC machines enhance production efficiency considerably. These machines can operate continuously, often improving the output rates beyond what manual machining can achieve. The automation aspect of CNC allows for fast setup and changeover times, making it feasible to complete jobs quicker than conventional methods.
Efficiency Factors Include:
- Reduced Setup Times: Unlike traditional methods, changing from one part design to another can occur swiftly through reprogramming, reducing the setup times dramatically.
- High-Speed Operations: Modern CNC machines are equipped to operate at high speeds, which translates to quicker cycle times. This capability directly influences productivity and, consequently, profitability.
- 24/7 Manufacturing: Many CNC machines can operate autonomously, meaning that companies can run their machines overnight, maximizing utilization without the need for manual oversight.
Reduction of Human Error
Human error is a substantial concern in the manufacturing process, leading to inefficiencies and additional costs. CNC machining significantly reduces these errors, primarily through its automated processes. This minimization also serves to improve overall workplace safety, another critical consideration in manufacturing environments.
Implications of Reduced Human Error:
- Accuracy in Processes: Automation ensures that the tasks are performed the same way every time, eliminating variability introduced by human hands.
- Higher Reliability: Automated quality checks built into CNC process reduce the opportunity for errors to slip through unnoticed.
- Training and Ongoing Education: While CNC operation requires skilled operators, the demand for training focuses more on programming and machine maintenance rather than manual machining skills. This shift can help reduce on-the-job errors significantly.
In summary, the advantages of CNC machining reconfigure how industries approach precision, efficiency, and error reduction. As technology continues to evolve, these benefits will likely expand, further solidifying the role of CNC machining in manufacturing environments.
Challenges and Limitations of CNC Machining
Understanding the challenges and limitations of CNC machining is critical. As companies strive for precision and efficiency, they also face various barriers that can hinder the implementation and effectiveness of CNC systems. This section will examine these challenges, providing insights into important issues that stakeholders must consider.
High Initial Investment Costs
When a business decides to invest in CNC machining, the initial costs can be considerable. CNC machines, especially those that are advanced with high capabilities, carry hefty price tags. This includes not only the purchase of the machinery itself but also the costs associated with installation and setup. In addition, software licensing and training for operators add to the financial burden. For smaller businesses or startups, these costs can be prohibitive, leading to potential financial strain.
Despite the long-term benefits of precision and efficiency, the upfront investment can deter some from fully embracing CNC technology. However, it is essential to view this as a long-term investment, where potential savings in labor and material waste may offset the initial expenditure over time.
Skill Requirements for Operation
The complexity of CNC machines demands a level of skill that goes beyond basic mechanical knowledge. CNC machinists must understand both the operation of the machine and the programming involved. G-code is the universal language for controlling CNC machinery, and it requires proficiency for effective programming and troubleshooting. Not everyone can be trained instantly to operate these machines.
Furthermore, operators need to adapt to new technologies swiftly, as the field of CNC machining continues to evolve with advancements in automation and artificial intelligence. Companies often must invest in ongoing training to ensure their workforce is qualified, which can add to operational challenges.
Maintenance and Repair Concerns
Regular maintenance is vital to keep CNC machines running smoothly. These machineries are generally reliable, but like any mechanical system, they can malfunction. Issues may arise from wear and tear, requiring timely repairs. The cost of maintenance can accumulate, especially if parts need to be replaced regularly.
Moreover, finding skilled technicians who can perform these repairs effectively might be challenging. Some companies may resort to outsourcing technical support, which could lead to extended downtime and production delays. Implementing a preventive maintenance program can help mitigate these risks, but it involves additional planning and resource allocation.
In the world of CNC machining, addressing challenges is necessary to maximize return on investment and maintain production efficacy.
Applications of CNC Machining
CNC machining is a cornerstone technology in modern manufacturing. Its applications span various industries, making it essential for professionals and students studying advanced production techniques. The ability to automate and precisely control machining processes allows for higher efficiency and quality in production. This section explores the significant areas of application, highlighting critical insights into their specific requirements and implications.
Manufacturing Industries
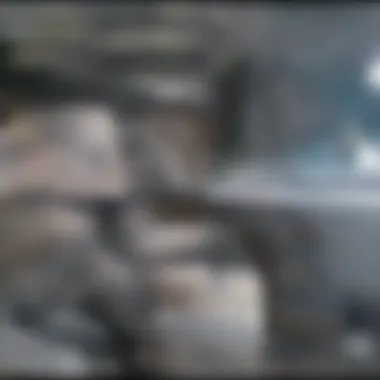
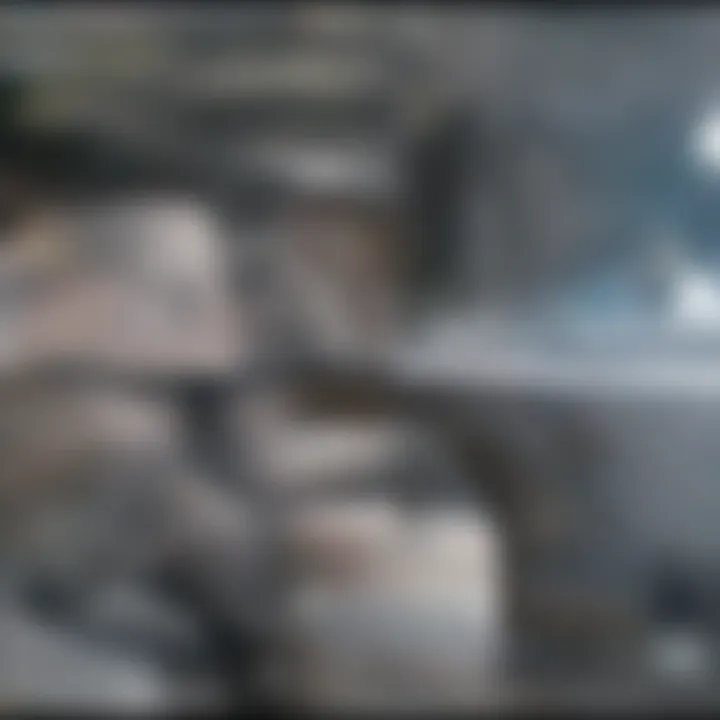
CNC machining has revolutionized the manufacturing sector. It is utilized across multiple industries, including metals, plastics, and composites. The adaptability of CNC machines supports numerous manufacturing processes such as turning, milling, and drilling. The ability to produce complex shapes and maintain high precision makes CNC machining invaluable. Companies can easily transition from one product to another without extensive retooling, which saves time and costs.
Benefits of CNC Machining in Manufacturing Industries:
- High precision and repeatability
- Reduced waste of materials
- Increased speed of production
- Better safety conditions compared to manual machining
Aerospace and Automotive
The aerospace and automotive sectors leverage CNC machining due to their stringent quality standards. Precision is critical in these industries, where components must meet rigorous safety and operational specifications. CNC machines allow for the production of intricate parts, such as turbine blades and engine components, that are essential for performance and safety.
In aerospace, lightweight and durable materials, like titanium and aluminum alloys, are increasingly common. CNC machining excels in handling these materials, producing parts that fit precisely while maintaining structural integrity. Similarly, in the automotive industry, CNC technology facilitates mass production of high-quality components with minimal lead times.
"CNC machines enable manufacturers to produce complex geometries with a level of accuracy unattainable through manual methods."
Medical Devices and Components
The demand for precision in the medical field is unparalleled. Medical devices and their components require an extreme level of accuracy to ensure patient safety and device efficacy. CNC machining meets these demands. It enables the production of surgical tools, implants, and diagnostic equipment with exceptional precision and reproducibility.
Manufacturers often work with biocompatible materials, such as stainless steel and specific polymers, made possible through CNC processes. The technology allows for rapid prototyping, essential in the fast-paced development cycles in the medical field. As regulations grow more stringent, the adoption of CNC machining becomes not just a choice but a necessity for quality assurance in medical device manufacturing.
Future Trends in CNC Machining
The realm of CNC machining is continuously evolving. As technology progresses, new trends emerge that reshape the landscape of manufacturing. Understanding these trends is critical for industry stakeholders. They dictate not only advancements in production but also influence the way businesses strategize and adapt.
Integration with Automation and AI
The integration of automation and Artificial Intelligence (AI) is one of the most significant trends in CNC machining. Automation enhances efficiency and reduces human error. AI, in particular, brings a new level of sophistication. It can optimize the machining process by analyzing data in real-time, predicting tool wear, and adjusting operations accordingly. This minimizes downtime and maximizes output.
Moreover, AI can facilitate predictive maintenance techniques. By monitoring machine conditions, it can foresee possible failures before they happen. As a result, companies experience less disruption in their operations. The combined effect of automation and AI leads to enhanced productivity, crucial for remaining competitive in the market.
Advances in Materials and Techniques
Material science is advancing rapidly. CNC machining is not exempt from these significant developments. New materials—lightweight alloys, composites, and advanced plastics—are becoming more prevalent. These materials offer unique properties that cater to specific industry requirements. For instance, aerospace and automotive sectors are increasingly relying on lighter materials to improve fuel efficiency and performance.
Additionally, techniques such as additive manufacturing are gaining traction. This approach blends traditional CNC processes with 3D printing capabilities. The result is an expanded range of possibilities for designers and engineers. By utilizing advanced materials and techniques, companies can produce parts that are not only stronger but also more complex in design.
The Rise of Customization and On-Demand Manufacturing
Customization is becoming more prominent in CNC machining. Consumers demand products tailored to their specifications. This shift toward personalized manufacturing is forcing companies to adapt their production methods. On-demand manufacturing—producing items as they are needed rather than in large batches—is part of this trend.
This model reduces waste and inventory costs. It also allows for quicker responses to market changes. CNC machines equipped with advanced software can produce customized parts efficiently. As a result, businesses can maintain flexibility and meet customer needs effectively.
Ending
In this article, the importance of Computer Numerical Control (CNC) machining has been addressed thoroughly. CNC technology plays a critical role in modern manufacturing, allowing for increased precision and efficiency. Through automated processes, CNC machines streamline production, minimize human error, and maintain consistent quality across batches. These advantages confer a competitive edge to businesses that adopt and implement CNC solutions.
The relevance of understanding CNC machining extends beyond just operational efficiency; it also involves comprehending the implications of emerging technologies. With advancements in automation and artificial intelligence integrating into CNC practices, professionals can expect significant shifts in how machining processes are conceived and executed. This highlights the necessity for continued education and adeptness in handling new tools and techniques.
Moreover, one must consider the challenges associated with CNC machining. While equipment may boast outstanding technological capabilities, the initial investment remains a critical barrier. Organizations must weigh long-term benefits against upfront costs. Skilled personnel are also vital, as proficient machine operation and programming are fundamental to leverage CNC's full potential.
As the demand for customized solutions increases, CNC machining will adapt, embracing on-demand manufacturing trends. Companies must stay alert to the evolving landscape to capitalize on new opportunities.
"Future technological evolution will likely redefine what CNC machining can achieve, necessitating a knowledgeable workforce and adaptable strategies."
In summary, the discussion within this article underscores that while CNC machining offers significant benefits, it is also pivotal to recognize the associated costs and skill requirements. As the landscape continues to evolve, staying aware of trends, research, and developments will be crucial for all professionals involved in this field.
Summary of Key Points
- CNC machining enhances precision and efficiency in manufacturing.
- The integration of AI and automation is reshaping the industry.
- Security and investment considerations are crucial for organizations.
- Skilled personnel are necessary to operate and program CNC systems effectively.
- The future of CNC machining trends towards customization and on-demand solutions.
Implications for Future Research and Development
The future holds significant potential for CNC machining as new technologies emerge. The synergy of CNC machines with advanced materials and smart manufacturing systems could revolutionize the production landscape.
- Exploration of AI: Continued research into artificial intelligence and machine learning applications can enhance operational efficiency. With smart programming and predictive maintenance, the reliability of CNC systems may improve.
- Sustainable Practices: As environmental concerns rise, exploring eco-friendly materials and processes within CNC manufacturing will become increasingly vital. Members of the industry should invest in sustainable approaches.
- Customization Needs: Future studies might focus on manufacturing processes that can quickly adapt to consumer demands for unique products. As customization grows in popularity, CNC technology will need to accommodate these shifts efficiently.
- Job Market Evolution: The role of workers will also change, requiring higher skill levels in programming and robotics to maximize CNC operations. Examining workforce development strategies is essential.
Significance of References
The references serve several critical functions in this article:
- Establishing Authority: Citing reputable sources reinforces the assertions made. When readers see citations from respected institutions or journals, they gain confidence in the presented data.
- Facilitating Research: The list of references also acts as a roadmap for further study. Readers who wish to expand their knowledge can explore the materials listed, enriching their understanding of the subject.
- Supporting Claims: Each reference provides substantiation for the technical claims about CNC technology and its applications. This is especially vital in a technical field where precision and accuracy are paramount.
- Credibility Enhancement: By including a range of sources, the article showcases a well-rounded perspective, indicating that the information is synthesized from diverse inputs rather than a narrow viewpoint.
Considerations for Effective Referencing
When compiling references, several considerations should be taken into account:
- Relevancy: Only include sources that directly contribute to the topic at hand. Irrelevant or tangential citations may distract or confuse readers.
- Currency: The rapid evolution of CNC technology necessitates that references are as up-to-date as possible. Older sources might provide historical context but should be supplemented with recent studies that reflect current advancements.
- Diversity of Sources: A mix of academic papers, industry reports, and credible online resources enhances the richness of references. This variety offers a holistic view of CNC machining, touching on multiple aspects such as its theoretical underpinnings, practical applications, and future trends.
The End
In summary, the references section not only offers validation but also enriches the content of the article. It bridges knowledge gaps for readers, facilitating informed discussions on the intricacies of CNC machining. As researchers and professionals engage with this material, the references stand as a testament to the article's scholarly rigor and relevance in the evolving landscape of manufacturing technology.