Current Cathodic Protection Rectifiers: Insights
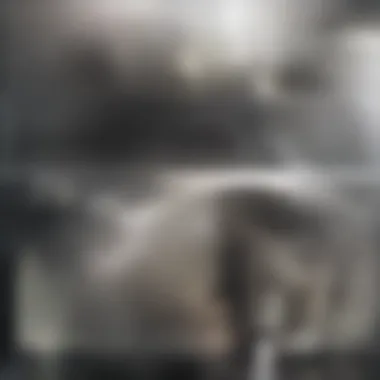

Intro
Corrosion is a pervasive issue in various industries, leading to significant economic losses and safety risks. Current cathodic protection rectifiers play a critical role in mitigating this problem. By providing an impressed current, these rectifiers enhance the effectiveness of cathodic protection systems, preserving the integrity of critical assets exposed to harsh environments. This article aims to delve into their functionality, application, benefits, and challenges in optimizing performance.
Key Findings
Major Results
Impressed current cathodic protection rectifiers serve as vital components in corrosion management systems. Their primary function is to generate a controllable direct current that flows into the ground or immersed structures to counteract corrosion. The technology shows remarkable efficacy across various sectors such as oil and gas, marine, and infrastructure. Studies indicate that the proper application and maintenance of these rectifiers can significantly extend the lifespan of assets, reducing maintenance costs.
Discussion of Findings
The implementation of current rectifiers presents advantages beyond mere corrosion protection. Enhanced safety and reduced liability issues are notable benefits attributed to effective cathodic protection systems. Additionally, there is a growing emphasis on optimizing rectifier performance by focusing on aspects such as power output stability and energy efficiency. Understanding the nuanced behavior of these systems under different environmental conditions is crucial for ensuring their effectiveness.
Methodology
Research Design
In this article, qualitative and quantitative research methods were applied to gather insights about current cathodic protection rectifiers. An extensive literature review formed the backbone of the research design, offering foundational knowledge and identifying gaps for further exploration.
Data Collection Methods
Data was collected from various credible sources including academic journals, industry reports, and case studies focusing on cathodic protection technologies. Interviews with industry professionals also provided valuable perspectives on real-world implementations and challenges.
Challenges and Considerations
Despite their advantages, the optimization of rectifier performance presents several challenges. External factors such as soil resistivity, temperature fluctuations, and current distribution complicate the effectiveness of cathodic protection. Furthermore, the proper sizing and placement of rectifiers remain critical to achieve desired outcomes. Understanding these challenges is essential for professionals involved in corrosion management and rectifier optimization.
"The effectiveness of cathodic protection is impacted by many variables. Addressing these is key to maintaining optimal performance."
- Industry Expert
Epilogue
Current cathodic protection rectifiers are indispensable in maintaining the integrity of structures vulnerable to corrosion. As industries continue to grapple with corrosion-related issues, investing in optimized cathodic protection systems will prove beneficial. Exploring the intricacies of rectifier functionality and performance can empower professionals to enact more effective corrosion management strategies.
Understanding Cathodic Protection
Cathodic protection is a crucial method that prevents corrosion in metals, especially those exposed to moisture and electrolytic environments. Understanding this concept is essential for professionals engaged in various industries where metal structures are prevalent. The core idea revolves around electrochemical processes that mitigate metal deterioration. By employing cathodic protection, significant financial savings can be achieved over time. The technology ensures longevity in equipment, structures, and pipelines.
A key benefit of being knowledgeable about cathodic protection includes the ability to select appropriate systems and components. This understanding translates to better decision-making in project planning and maintenance strategies. The effective implementation brings not only safety but also enhances operational reliability in areas like petrochemical facilities and marine constructions.
Individuals dealing with asset management should consider various factors including setup costs, maintenance protocols, and the specific environment in which a system will operate. Recognizing the complexities of cathodic protection helps in optimizing performance and extending the life expectancy of essential metal assets.
Principles of Cathodic Protection
The fundamental principles of cathodic protection hinge on two primary methods: galvanic and impressed current cathodic protection. Each method operates under the electrochemical principle where a sacrificial anode or an external power source is used to prevent corrosion. Essentially, these systems work by creating a mechanism where the metallic structure becomes the cathode in a corrosion process, thus halting the damaging reactions.
Types of Cathodic Protection Systems
Galvanic Cathodic Protection
Galvanic cathodic protection employs sacrificial anodes made from more reactive metals such as zinc or magnesium. When these anodes are connected to the metal structure, they corrode instead of the structure, providing an effective protective layer. This method is particularly advantageous because it does not require an external power source, making it a practical choice for many applications.
However, its effectiveness diminishes in environments with high resistivity. This limits the choice of where galvanic systems can be deployed. The simplicity and low maintenance requirements of galvanic protection contribute to its appeal, hence making it a popular option in smaller applications or where installation costs need minimizing.
Impressed Current Cathodic Protection
Impressed current cathodic protection systems utilize a direct current source to impose a protective charge on the metal surface. This method is especially effective for large structures or pipelines where the risks of corrosion are heightened. Its key characteristic is the capability to control the output, allowing for adjustments based on environmental conditions.
While impressed current systems may incur higher initial costs due to equipment and installation needs, they offer long-term advantages. They are useful in diverse settings, including offshore platforms and underground pipelines. A unique feature is the ability to maintain consistently low corrosion rates, which is vital for the integrity of critical infrastructure. Nevertheless, they do require more frequent monitoring and maintenance to ensure reliable operation.
Impressed Current Cathodic Protection Overview
Impressed Current Cathodic Protection (ICCP) is an essential technology designed to mitigate corrosion in various structures. Corrosion often leads to significant financial losses and operational disruptions. By ensuring that metallic surfaces are protected from corrosive environments, ICCP systems play a vital role in the longevity and reliability of critical infrastructure. Understanding the components and mechanisms of ICCP is crucial for professionals engaged in corrosion management and related fields.
Key Components of the System
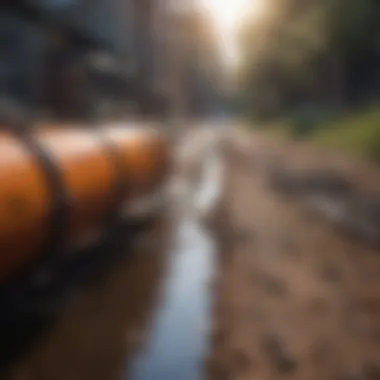
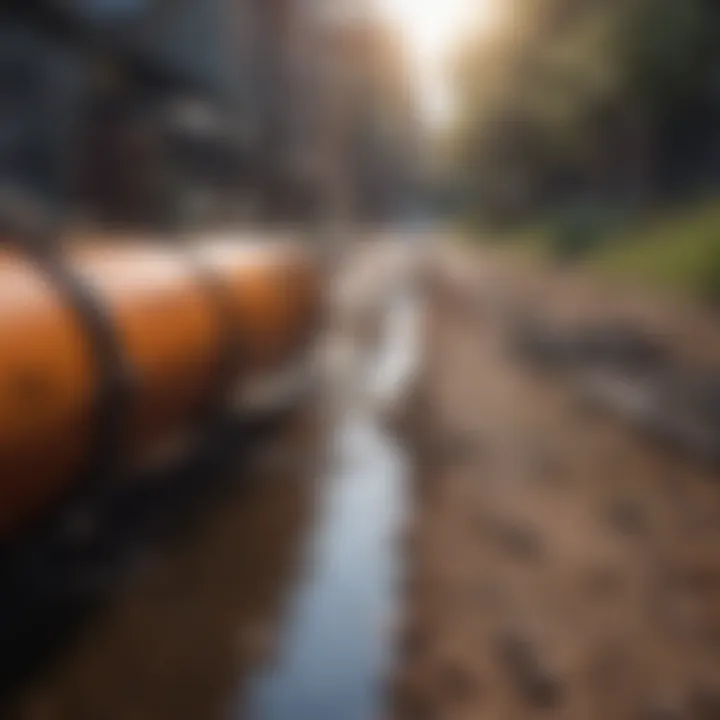
Rectifiers
Rectifiers are a fundamental component of the impressed current cathodic protection system. They convert alternating current (AC) from the power supply into direct current (DC), which is necessary for effective cathodic protection. One key characteristic of rectifiers is their ability to manage high voltage output, making them suitable for extensive systems that require significant power.
The benefit of using rectifiers lies in their control and stability. They allow precise regulation of current and voltage, which ensures effective corrosion protection. Additionally, rectifiers can be monitored and adjusted remotely, providing operational ease. However, they can be costly to install and may require specialized maintenance.
Anodes
Anodes serve as positive electrodes that are critical in cathodic protection systems. They provide a pathway for the electric current to flow through the structure being protected. A significant feature of anodes is their materials, which often include titanium, graphite, or mixed metal oxides. The choice of material directly impacts the performance and lifespan of the system.
Anodes offer the benefit of high efficiency and long life when properly selected and maintained. However, they can suffer from issues such as depletion over time, which may necessitate replacement. The impact of anodes on the overall system performance is substantial, making their selection an important consideration in ICCP design.
Reference Electrodes
Reference electrodes are pivotal in measuring the potential difference in the system. They provide real-time feedback on the effectiveness of the cathodic protection being delivered. One essential characteristic of reference electrodes is their stability; they must maintain a constant potential over time to provide accurate readings.
Reference electrodes are beneficial due to their role in ensuring optimal current distribution within the system. They allow operators to monitor performance and adjust settings proactively, enhancing reliability. Nonetheless, they can be sensitive to environmental changes, which might affect their accuracy. Thus, careful installation and calibration is essential for effective system operation.
Mechanism of Operation
Power Supply Dynamics
Power supply dynamics in ICCP systems refer to how electrical energy is utilized to drive cathodic protection. The dynamics are crucial because they affect how well the system functions in various environmental conditions. A characteristic feature of power supply dynamics is the ability to adjust output based on the load and environmental factors.
Using sophisticated power conversion techniques, ICCP systems can ensure that adequate power is provided to the anodes. This adaptability is beneficial; it helps in achieving optimal protection levels. However, fluctuations in power availability can lead to inconsistent performance, requiring monitoring to maintain stability.
Current Distribution
Current distribution is vital in ensuring that all areas of a structure receive adequate protection. The effective management of current flow can prevent localized corrosion, which can cause severe damage over time. A key characteristic of current distribution is its ability to adapt based on the orientation and surface area of the protected structure.
The advantages of proper current distribution include enhanced protection and reduced maintenance costs. However, achieving uniform distribution in complex geometries can be challenging. Any uneven distribution can lead to areas of weakness, underscoring the need for careful design and implementation in set up processes.
Functionality of Impressed Current Cathodic Protection Rectifiers
Understanding the functionality of impressed current cathodic protection rectifiers is crucial for maintaining the integrity of structures exposed to corrosive environments. These rectifiers play a significant role in the overall performance and efficiency of cathodic protection systems. By converting alternating current into direct current, they enable effective corrosion prevention. This process ensures that structures such as pipelines and marine vessels remain protected.
Rectification Process
AC to Conversion
AC to DC conversion is a fundamental aspect of impressed current cathodic protection systems. This process transforms alternating current, which is commonly available in most electrical grids, into direct current. Direct current is essential for effective cathodic protection, as it can be precisely directed to the anodes that exhibit corrosion.
The key characteristic of AC to DC conversion is its ability to offer a consistent supply of current. This consistency is a beneficial trait because it ensures that the cathodic protection system operates effectively without fluctuations that could lead to insufficient protection. Additionally, AC to DC conversion technology allows for various methods, such as silicon-controlled rectifiers, enhancing reliability.
A unique feature of AC to DC conversion is its adaptability to different power sources and requirements. This aspect can be advantageous, especially when designing systems for diverse applications. However, initial costs associated with the converters and the requirement for regular maintenance of these systems can be seen as disadvantages.
Voltage Regulation
Voltage regulation in impressed current cathodic protection rectifiers also holds substantial importance. This aspect involves maintaining specific voltage levels across the system, ensuring that proper current flows to the protection zone. Voltage regulation is vital for adapting to varying environmental conditions that affect the resistance at the anodes.
One key characteristic of voltage regulation is its role in preventing over-protection and under-protection scenarios, which can damage the structure or lead to ineffectiveness in corrosion control. This regulation is a popular choice due to its precision in maintaining system integrity over time.
A unique feature of voltage regulation is its feedback mechanism, which allows for real-time monitoring and adjustment based on the conditions. This can favor proper operational performance. Nevertheless, reliance on this mechanism may involve complexity in installation and calibration, requiring expert knowledge to maximize efficiency.
Control Mechanisms
Control mechanisms are critical for ensuring optimal performance of cathodic protection rectifiers. These ensure that the systems function within desired parameters, adapting to changing conditions effectively.
Automated Controls
Automated controls are a significant advancement in the management of cathodic protection systems. They facilitate ongoing monitoring and adjustments without the need for human intervention. This automation contributes to efficiency, enabling quicker responses to variations in current requirements.
The key characteristic of automated controls is their ability to provide data logging and reporting, which enhances maintenance practices. Thus, automated controls are a beneficial component as they offer an improved understanding of system performance over time.
A unique feature of automated systems is their integration with smart technologies. This can improve decision-making processes when managing corrosion risks. However, the reliance on technology also introduces vulnerability to failures if systems are not maintained properly.
Manual Adjustments
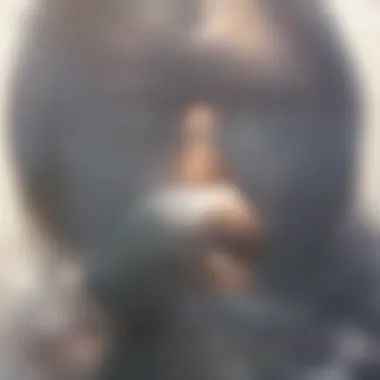
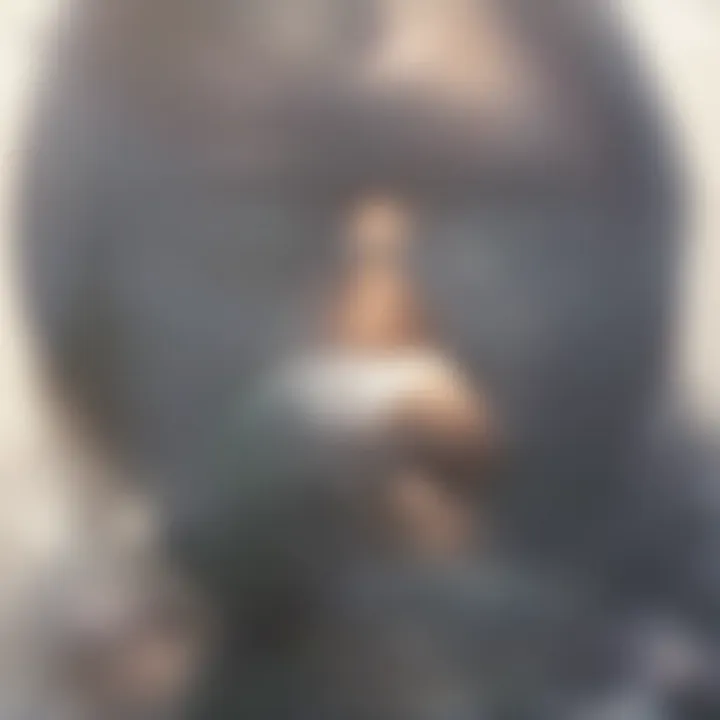
Manual adjustments remain a crucial aspect of managing impressed current cathodic protection systems. These adjustments are valuable for operators who need to make specific changes based on direct observations or unique circumstances affecting the cathodic protection measures.
A key characteristic of manual adjustments is their responsiveness, as they can be implemented quickly based on immediate concerns. This makes them a beneficial choice, particularly in environments where conditions can change rapidly.
A unique feature of manual adjustments is their direct involvement of human operators. This factor can provide specific insights based on experience. However, potential disadvantages include the risk of human error and the need for regular operator training to ensure effective decision-making.
Conclusion: Understanding both the rectification process and control mechanisms allows stakeholders to optimize cathodic protection rectifiers, ultimately enabling efficient corrosion prevention practices across various industries.
Applications of Impressed Current Cathodic Protection Rectifiers
The use of impressed current cathodic protection (ICCP) rectifiers is vital in several industries, primarily for preventing corrosion that can threaten the integrity of critical infrastructure. These applications span multiple sectors, each requiring tailored approaches to meet specific challenges. By exploring various contexts where ICCP rectifiers are applied, one can appreciate the nuances of their operation and the benefits that accrue from their use.
Use in Petrochemical Industries
The petrochemical industry is particularly susceptible to corrosion due to the harsh environments in which pipelines and tanks operate. Impressed current cathodic protection rectifiers protect these assets by providing a consistent flow of current that inhibits the electrochemical reactions that cause corrosion. The high demands of petroleum transport require reliable solutions to prevent leaks and ensure safety.
- Protection against Atmospheric Corrosion: Refineries often deal with vapors and other corrosive agents. Cathodic protection using ICCP ensures that structures are not adversely affected.
- Reducing Maintenance Costs: By implementing effective cathodic protection systems, companies can significantly reduce the frequency of maintenance interventions, translating to savings over time.
- Longevity of Equipment: Equipment longevity is crucial in keeping operations running smoothly and avoiding costly shutdowns. ICCP rectifiers extend the life of tanks and pipelines by reducing the rate of degradation.
Marine Structures
Marine structures, such as piers, ships, and offshore platforms, face a unique set of challenges, primarily due to the continuous exposure to saltwater. The application of ICCP rectifiers in this domain is critical for several reasons:
- Enhanced Protection: The oceanic environment accelerates corrosion rates. ICCP systems help mitigate this effect effectively, ensuring the structural integrity of the marine installations.
- Safety Assurance: Protecting marine structures from corrosion also assures safety for workers and the environment. An effective rectifier system reduces the risk of failure due to erosion.
- Environmental Compliance: Many regions have strict regulations concerning the environmental impact of corrosion. ICCP helps in maintaining compliance by preventing leaks and spills.
Underground Pipelines
Underground pipelines are essential for transporting energy resources but they are also prone to corrosion caused by soil electrochemistry. The role of ICCP rectifiers in this application cannot be overstated. Their benefits include:
- Continuous Monitoring: Many ICCP systems are now equipped with remote monitoring technologies. This capability allows for real-time assessment of system performance and corrosion rates.
- Adaptability: Different soil types require adaptable protection strategies. ICCP rectifiers can be adjusted to account for variances in soil resistivity.
- Reduced Product Loss: By preventing corrosion, the rectifiers help in reducing product loss, which is a critical factor in ensuring that the transport of gas and oil remains efficient and cost-effective.
Conclusion:
In each of these applications, the role of impressed current cathodic protection rectifiers is not only to prevent corrosion but also to ensure compliance with safety regulations and enhance the overall operational efficiency of critical infrastructure. Attention to detail in monitoring and maintenance can optimize these systems, making them a fundamental aspect of asset management in various industries.
Benefits of Impressed Current Cathodic Protection Rectifiers
Impressed current cathodic protection rectifiers play a critical role in corrosion control across various industries. Their utility stretches from enhancing the lifespan of assets to ensuring operational efficiency. Specifically, these rectifiers convert alternating current (AC) from power sources into direct current (DC) that is essential for effective cathodic protection. Understanding the benefits of these systems allows industries to prevent corrosion-related damage, reduce maintenance costs, and contribute to sustainability efforts.
Enhanced Asset Longevity
The primary benefit of impressed current cathodic protection rectifiers is the enhancement of asset longevity. Corrosion can significantly shorten the lifespan of infrastructure. When properly operated, these rectifiers provide a continuous flow of current that protects structures such as pipelines, tanks, and marine vessels. By creating an electrochemical environment, they inhibit the electrochemical reactions that cause corrosion.
Advanced materials used in rectifiers, such as titanium or graphite, also function to increase their effectiveness and longevity. This means assets are not only preserved for longer periods but are also safeguarded against potential failures, which can have catastrophic implications.
Cost Efficiency
Another paramount advantage is the cost efficiency that impressed current cathodic protection rectifiers bring. An effective cathodic protection system can save substantial amounts of money over time. By reducing corrosion-related damage, companies can avoid significant repair costs and extend the replacement cycles of critical components. This cost-saving extends beyond immediate repairs; it includes reduced downtime and associated loss of production, further protecting the financial health of an organization.
In many scenarios, the initial investment in a robust rectifier system is outweighed by the savings realized through lower operational costs. By prioritizing corrosion protection, organizations can allocate resources more effectively, enabling them to invest in growth rather than maintenance.
Operational Reliability
Operational reliability is another key benefit provided by impressed current cathodic protection rectifiers. These systems operate continuously and consistently, provided that regular maintenance practices are followed. They are designed to monitor current output effectively and can adjust according to specific operational requirements.
The integration of automated control systems enhances performance. Such systems can detect discrepancies in cathodic protection levels and initiate corrective actions before any significant damage occurs.
Effective cathodic protection is not just about prevention; it's about sustaining operational integrity.
Additionally, the use of high-quality materials and components ensures that corrosion protection remains intact even in harsh environmental conditions. This reliability translates into fewer operational disruptions, making impressed current cathodic protection rectifiers invaluable in industries where infrastructure is critical.
In summary, the benefits of impressed current cathodic protection rectifiers cannot be understated. They enhance asset longevity, drive cost efficiency, and ensure operational reliability. For industries facing the challenges of corrosion, these rectifiers provide a comprehensive solution that contributes to overall sustainability and profitability.
Challenges in Implementing Impressed Current Cathodic Protection
Implementing impressed current cathodic protection (ICCP) systems presents several challenges that must be addressed for effective corrosion prevention. Understanding these challenges is essential for professionals and researchers in the field, as it allows for better planning and execution of ICCP projects. Addressing the initial investment costs, maintenance requirements, and environmental considerations can significantly impact the performance and longevity of cathodic protection systems.
Initial Investment Costs
One of the primary hurdles in adopting ICCP systems is the initial investment costs. These costs are not just limited to the purchase of rectifiers and anodes, but extend to comprehensive installation expenses, site assessments, and the potentially lengthy commissioning process. High-quality equipment, while crucial for effective cathodic protection, can be expensive, necessitating careful budget planning. Moreover, the necessity for skilled labor during installation further raises financial implications.
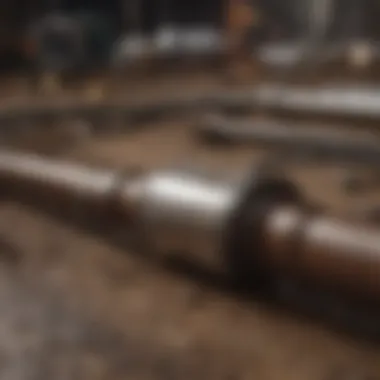
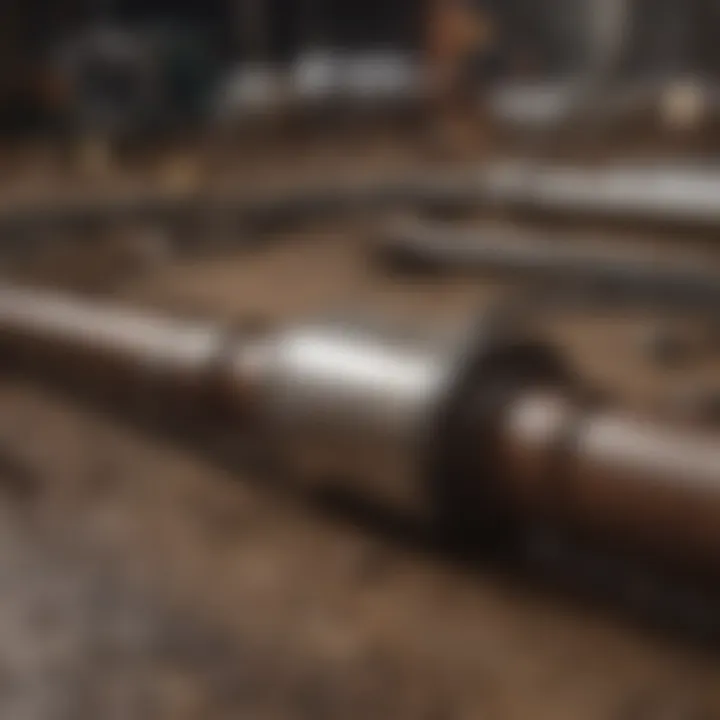
Organizations must evaluate the potential return on investment by weighing the costs against the long-term benefits. Effective ICCP can prevent costly corrosion damage to assets, saving significant future expenditure. Still, the upfront financial commitment remains a pivotal factor that can deter businesses from pursuing this technology.
Maintenance Requirements
Another challenge associated with ICCP systems involves ongoing maintenance requirements. Regular monitoring and periodic maintenance are vital to ensure that the system operates optimally. This can be resource-intensive. Technicians must routinely inspect rectifiers and anodes, check for any signs of malfunction, and conduct necessary repairs.
The complexity of ICCP systems means that maintenance should ideally be performed by skilled personnel who understand the intricacies involved. Neglecting these maintenance needs can lead to system failures, resulting in inadequate corrosion protection, which can be both damaging and costly. Organizations must allocate sufficient resources and commit to training personnel to manage maintenance effectively.
Environmental Considerations
Environmental considerations cannot be overlooked when implementing ICCP systems. The materials used in cathodic protection can have ecological implications. For instance, selecting anodes that do not leach toxic substances into the environment is essential to avoid negative impacts on local ecosystems.
Moreover, the placement of ICCP systems often intersects with regulations concerning environmental protection. Compliance with these regulations can require additional administrative efforts and potentially influence the design of the system. Understanding and navigating these regulations is crucial for successful implementation.
Overall, addressing the challenges associated with the implementation of impressed current cathodic protection is vital. Organizations must approach these elements with a thorough understanding and proactive strategies to ensure long-term system efficacy and environmental stewardship.
Best Practices for Rectifier Use
In the realm of impressed current cathodic protection rectifiers, adherence to best practices is vital. Proper implementation ensures longevity and operational efficiency. The significance of these practices extends beyond installation; it impacts ongoing protection against corrosion. Consistency in maintenance and careful adjustment techniques are essential to uphold the rectifier's performance and effectiveness.
Regular Monitoring and Maintenance
Regular monitoring and maintenance are crucial aspects of rectifier management. Operators must frequently check for any deviations in output voltage and current. Consistent oversight helps to identify issues early, saving time and resources in the long run. For instance, irregular readings might indicate degradation of anodes or even potential faults in the rectifier itself.
The maintenance schedule should be comprehensive and documented. This includes:
- Checking connections for corrosion or looseness.
- Verifying the integrity of anodes and reference electrodes.
- Testing the rectifier's performance metrics regularly.
Beyond mere checks, routine maintenance allows for adjustments that align operation with environmental conditions. For example, if a site experiences higher moisture levels than expected, adjustments might be needed in current output to ensure adequate protection. This proactive approach minimizes risks and enhances the longevity of cathodic systems.
Calibration and Adjustment Techniques
Calibration and adjustment are essential for the effectiveness of cathodic protection systems. A properly calibrated rectifier optimizes its output to meet the specific needs of the structures it protects. This process involves aligning the output current and voltage settings according to the parameters established during the design phase.
Effective techniques for calibration include:
- Utilizing calibrated reference electrodes to denote accurate readings.
- Adjusting rectifier settings based on environmental changes and observed data.
Operators should have a clear understanding of the system's dynamics. Frequent adjustments may be necessary in response to fluctuations in soil resistivity or changes in the surrounding environment. Implementing a systematic approach to calibration ensures that the cathodic protection remains effective. Inadequate calibration can lead to either overprotection, causing material stress, or underprotection, resulting in corrosion. Thus, maintaining an optimal operating condition is key for functionality.
"Optimal performance hinges on a careful synthesis of monitoring, maintenance, calibration, and adjustment techniques."
Future Trends in Cathodic Protection Technologies
The realm of cathodic protection is evolving, and understanding the future trends in this technology is paramount for stakeholders involved in corrosion management. These trends pertain not only to enhancing materials but also to the integration of smart technologies, which can vastly improve system efficiency and performance. The insights covered in this section provide a nuanced perspective on the direction in which cathodic protection technologies are heading, helping professionals to adapt and optimize their strategies for asset preservation in challenging environments.
Advancements in Materials
Recent advancements in materials used for cathodic protection systems are notable. Innovations such as high-performance anode materials are becoming more prevalent. These materials are engineered to resist corrosion and extend the life of the anodes, thereby enhancing overall system functionality. Many experts emphasize the shift from traditional materials to composite materials that exhibit superior longevity.
Moreover, nano-coatings are gaining traction as a means of protecting metal surfaces effectively. These coatings improve the corrosion resistance and can significantly reduce maintenance costs. The importance of research into environmentally friendly materials cannot be overstated, especially as industries work towards sustainability goals. As these materials become more widely implemented, their long-term benefits can have profound implications regarding operational efficiency and ecological impact.
Integration with Smart Technologies
Another significant trend is the integration of smart technologies into cathodic protection systems. This approach harnesses sensor technologies that provide real-time data regarding system performance. Such integration allows for the continuous monitoring of cathodic protection levels, identifying issues before they escalate.
These technologies often employ data analytics to predict potential failures, facilitating proactive maintenance. Automated controls can adjust output levels based on environmental factors, which ultimately enhances the system efficiency. The implementation of smart systems leads to reduced operational costs and improved asset management.
Epilogue and Considerations
The topic of cathodic protection systems and their implementation is of utmost importance in industries where metal structures face corrosion challenges. An effective implementation of impressed current cathodic protection rectifiers plays a critical role in safeguarding infrastructures and prolonging their operational life. This section will summarize key points and provide final insights on the significance of these systems.
Summary of Key Points
- Understanding Cathodic Protection: It involves preventing corrosion through electrochemical means, which is vital for structures such as pipelines, tanks, and maritime assets.
- Impressed Current Rectifiers: These are central components that enable the efficient functioning of cathodic protection systems by converting alternating current (AC) to direct current (DC) and regulating voltage output.
- Applications: Industries such as petrochemicals, marine, and transportation heavily rely on these rectifiers to protect critical assets against electrochemical degradation.
- Benefits: Enhanced asset longevity, cost efficiency, and operational reliability are notable outcomes of effectively functioning rectifiers that help organizations avoid costly repairs and replacements over time.
- Challenges: Initial costs of installation and necessary regular maintenance may pose hurdles. Environmental factors must also be taken into account when designing and implementing these systems.
Final Thoughts on Cathodic Protection Systems
Cathodic protection systems, particularly those utilizing impressed current rectifiers, offer significant advantages in combating corrosion. As industries evolve and face increasingly aggressive environmental conditions, the importance of these protective measures cannot be overstated. Continuous advancements in technology, materials, and integration with smart systems will shape future trends, optimizing protection methods. The complexities surrounding initial investments and maintenance should be balanced against long-term benefits, which ultimately lead to greater asset preservation and reliability.
"Investing in corrosion prevention strategies is a proactive measure that yields long-term dividends in the protection of critical assets."
In summary, cathodic protection systems are not just a necessary utility; they represent a strategic approach to asset management and sustainability in industries where corrosion is a persistent threat. Understanding the implications of their performance is essential for any professional navigating the challenges of corrosion management.