Insights into Blowing Injection Moulding Techniques
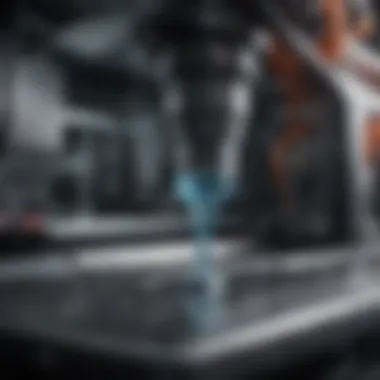
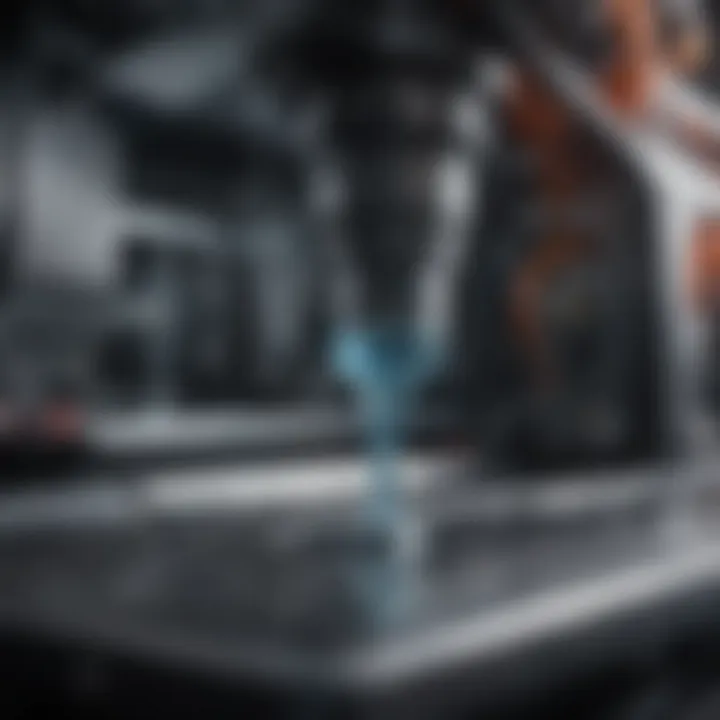
Intro
Blowing injection moulding is a manufacturing technique that has gained attention for its unique ability to produce hollow plastic components efficiently. The integration of injection moulding and blow moulding allows for better design flexibility and cost-effective production processes. In a world increasingly focused on optimizing manufacturing methods, understanding blowing injection moulding becomes crucial.
The process stands out for its versatility, applicable in various industries such as automotive, packaging, and consumer goods. Its capacity to create complex shapes and sizes while maintaining the integrity of the material presents a significant advantage over traditional methods. As technology advances, innovations in machinery and material selection continue to shape this sector, impacting environmental considerations and sustainability.
In this article, we will explore the intricate details surrounding blowing injection moulding. We will highlight key findings from current research, delve into methodology, and consider applications, machinery, and environmental implications. This comprehensive guide aims to provide valuable insights for students, researchers, and professionals navigating this specialized manufacturing technique.
Key Findings
Major Results
The investigation into blowing injection moulding has revealed several important findings. First, the process combination allows for reducing waste and energy consumption, making it environmentally friendly compared to other manufacturing processes. Efficiency is enhanced particularly in terms of cycle time and production volume.
The integration of efficiency and versatility in blowing injection moulding positions it as a forward-thinking solution in plastic manufacturing.
Following the analysis of various studies, we also found that the choice of materials plays a critical role in the quality and durability of the products. Many manufacturers are now exploring bioplastics and recycled materials, which benefits the industry and mitigates environmental impact. Furthermore, advancements in technology have led to the development of smarter machinery that optimizes the production process.
Discussion of Findings
The findings discussed shed light on advancements made in blowing injection moulding technology. The reduced carbon footprint achieved through improved energy efficiency suggests a strong correlation between manufacturing methods and sustainable production. As more companies prioritize environmental sustainability, the adoption of blowing injection moulding is expected to increase.
On the material front, the growing interest in bioplastics indicates a shift in consumer preferences towards eco-friendly products. This change not only aligns with market demands but also encourages manufacturers to rethink their material choices, leading to a positive outlook for recycling initiatives.
Ultimately, the continuous development in machinery and techniques poses a challenge for companies to adapt swiftly to remain competitive. The balance between innovation and traditional practices is crucial in harnessing the full potential of blowing injection moulding.
Methodology
Research Design
The research surrounding blowing injection moulding employs a qualitative approach, utilizing case studies and expert interviews to gather data. This design allows for an in-depth exploration of practices within the industry and provides insights from experienced professionals who understand the nuances of the process.
Data Collection Methods
Data collection methods include:
- Interviews: Engaging with professionals in the field to learn their experiences and perspectives.
- Literature Review: Analyzing existing studies and reports published on blowing injection moulding to identify trends and key developments.
- Surveys: Distributing questionnaires to gather quantitative data from various manufacturing companies regarding practices and preferences.
These methods contribute to a comprehensive understanding of blowing injection moulding, highlighting its significance and the ongoing evolution in the field. This synthesis of information will underscore the importance of this manufacturing technique in today's industry.
Preamble to Blowing Injection Moulding
Blowing injection moulding is a critical manufacturing process that blends the advantageous traits of both blowing and injection moulding techniques. This method stands out for its ability to produce hollow plastic objects efficiently, such as bottles and containers, positioning it as a cornerstone in various industries. Understanding this process is essential for students, researchers, and professionals, as it not only bolsters manufacturing capabilities but also addresses emerging needs in material science and sustainability.
The relevance of blowing injection moulding extends beyond mere production efficiency. It plays a significant role in economic development and environmental practices. This section will cover foundational aspects and historical development, creating a framework for appreciating its value in modern manufacturing.
Definition and Overview
Blowing injection moulding can be defined as a process that incorporates the principles of injection moulding and blow moulding. In this method, molten plastic is injected into a mould and then air is blown into the molten material to expand it into hollow shapes. This technique allows for the creation of intricate designs that maintain optimal strength and weight.
The primary benefits of blowing injection moulding include cost-effectiveness, versatility in design, and a high rate of production. These features make it an attractive option for producing large quantities of thin-walled containers and other hollow products. The integration of advanced control systems has also enhanced precision, making it suitable for applications that require stringent quality specifications.
Historical Development
The origins of blowing injection moulding can be traced back to the mid-20th century when the demand for plastic products began to rise dramatically. The integration of the blowing process with injection methods emerged as a response to the need for more efficient manufacturing techniques. Initially, it was implemented primarily for bottle production, but as technology advanced, it expanded into other areas, including medical and industrial applications.
Over the decades, several innovations have taken place in machinery and materials, significantly enhancing the capabilities of blowing injection moulding. Developments such as improved heating and cooling systems, software-controlled processes, and sophisticated mould designs have transformed the landscape of production.
Today, blowing injection moulding is recognized globally, with various manufacturers adopting it to maximize quality and efficiency. Its impact on various sectors underscores its importance, and continued research and development promise to unlock even greater capabilities.
Fundamental Principles of Blowing Injection Moulding
The principles behind blowing injection moulding are essential for understanding how this manufacturing process operates. This section lays the groundwork for grasping the mechanics and flow of materials within the system. A solid comprehension of these principles is vital not just for engineers and designers, but also for anyone interested in mass production of hollow plastic products. The synergy of injection and blow moulding techniques amplifies efficacy, allowing for enhanced customization and efficiency in production.
Process Mechanism
The process mechanism in blowing injection moulding involves several distinct steps that are crucial for successfully creating hollow parts. First, the moulding begins with the heating of thermoplastic materials, which are typically in the form of pellets. This material is then transferred to the injection unit where it gets melted and injected into a specially designed mould.
Once injected, air is introduced into the molten plastic within the mould, causing the material to expand and take the shape of the cavity. This dual action of injection followed by blowing is what sets blowing injection moulding apart. The core features of this process mechanism can be summarized as follows:
- Heating: Efficient heating of the material is critical for proper injection and expansion.
- Injection: Fast injection into the mould ensures swift and uniform filling.
- Blowing: Controlled introduction of air creates the necessary hollow structure.
- Cooling and Solidification: The mould is cooled to solidify the shape before extraction.
This meticulous sequence demonstrates how the integration of multiple processes results in the production of high-quality hollow components.
Material Flow Dynamics
Understanding material flow dynamics in blowing injection moulding is essential for optimizing production efficiency. The behaviour of the material as it flows and expands within the mould directly impacts the final quality of the product.
Key factors influencing material flow include:
- Viscosity: The viscosity of melted plastic affects how easily it can be injected and how uniformly it fills the mould. Higher viscosity may lead to incomplete filling.
- Temperature: Maintaining the right temperature is important. If the material is too hot, it may degrade; if too cool, it may not flow well.
- Pressure: The injection pressure must be controlled to ensure that the material fills all mould areas without causing defects.
- Material Composition: Different plastics have unique flow characteristics, impacting the overall process.
Maintaining a smooth and efficient material flow is critical for producing high-quality moulded parts. Manufacturers often employ simulations and feedback systems to monitor these dynamics closely, allowing for adjustments in real time. Additionally, thorough testing and iterating on parameters can lead to improvements in the overall production process.
Key Components of Blowing Injection Moulding Machines
In the realm of blowing injection moulding, understanding the machinery's key components is essential. This knowledge not only enhances productivity but also allows for better quality control and efficiency in production. The integration of different units ensures a seamless manufacturing process, which is vital for producing hollow plastic products.
Injection Unit
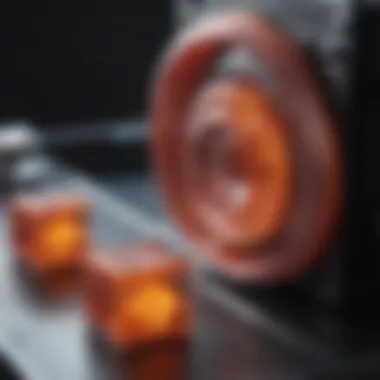
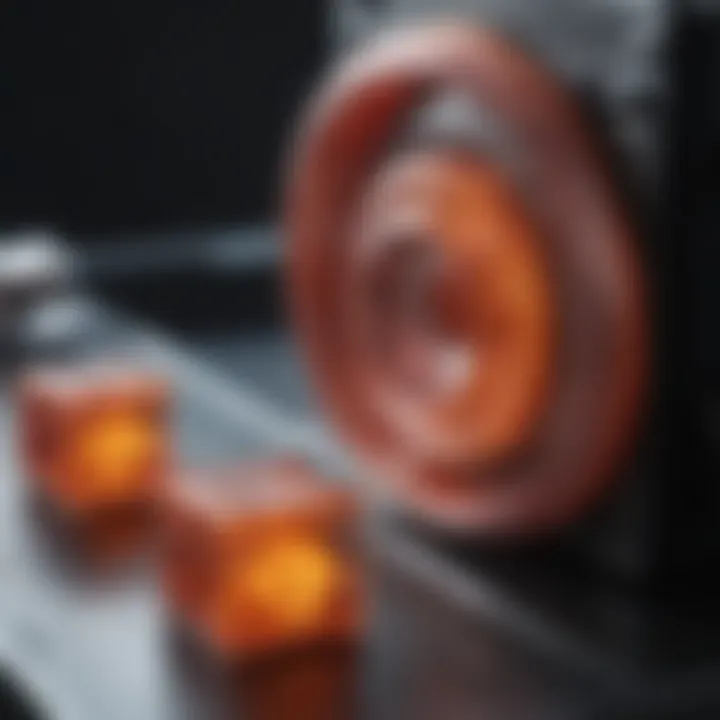
The injection unit serves as the heart of the blowing injection moulding machine. It is responsible for melting and injecting the polymer material into the mould. This component uses a screw or a plunger mechanism to transport the resin. During this process, the polymer is heated to a specific temperature that turns it into a malleable state. Then, the molten polymer is injected into the pre-formed mould, where it begins to take shape.
Accurate control over the injection parameters, such as temperature and pressure, impacts the final product's quality significantly. A well-calibrated injection unit ensures uniform material distribution, reducing defects and improving overall consistency.
Blowing Unit
Following the injection process, the blowing unit plays a crucial role in shaping the hollow structure of the final product. This unit introduces air into the injected polymer, expanding it against the inner walls of the mould. The pressure applied during the blowing process determines the thickness and surface finish of the part.
Considering different factors like the blowing pressure and cooling time is vital, as they can affect the mechanical properties of the final product. A robust blowing unit is essential for achieving precise dimensions and structural integrity, enabling complex designs not easily achievable through conventional methods.
Mould Design
Mould design stands as one of the most critical considerations in the entire process of blowing injection moulding. An effective mould design must facilitate smooth material flow and even cooling. It accounts for factors like wall thickness, part geometry, and material shrinkage during cooling.
Additionally, the choice of materials for the mould construction impacts durability and maintenance costs. Common materials include aluminum and steel, each offering unique benefits. Furthermore, the design should incorporate features for easy ejection of products once formed, thus minimizing production downtime.
In summary, the injection unit, blowing unit, and mould design are integral to the operation of blowing injection moulding machines. Understanding these components allows for better optimization and innovation in producing advanced plastic products.
Materials Used in Blowing Injection Moulding
Materials are at the core of blowing injection moulding as they determine not only the quality and durability of the final products but also influence the efficiency of the overall manufacturing process. The proper selection of materials affects production timelines, cost, and functionality of the items produced. The most commonly used materials in this process include various types of polymers, which are critical for achieving the desired properties in the final products. Understanding the fundamental aspects of materials involved is essential for anyone engaged in this field, including students, researchers, and professionals.
Polymer Selection Criteria
When selecting polymers for blowing injection moulding, various criteria must be evaluated. Here are some key factors:
- Mechanical Properties: The strength, flexibility, and durability of the polymer significantly impact the performance of the final product. Applications may require polymers to withstand certain mechanical stresses.
- Processing Conditions: Each polymer has specific processing temperatures and conditions. Understanding how a polymer behaves in the blowing and injection phases is vital. A polymer that degrades easily at high temperatures may not be suitable.
- Thermal Resistance: The ability of a polymer to maintain its properties under a specified temperature range is crucial, especially in applications where temperature fluctuation is common.
- Chemical Resistance: Some products may be exposed to harsh chemicals. A polymer's resistance to these chemicals can be a deciding factor.
- Cost Efficiency: While some polymers may offer superior properties, their cost can be prohibitive. A balance between performance and cost needs to be determined for production feasibility.
In summary, the choice of polymer should align with the desired properties of the final product while maintaining cost-effectiveness and process compatibility.
Additives and Fillers
The use of additives and fillers in blowing injection moulding serves several important functions. These materials enhance the performance of the main polymer, allowing for the customization of properties to meet specific needs. Key considerations include:
- Fillers: Fillers such as calcium carbonate or talc can be added to improve the strength and stiffness of products. They can also reduce material costs by replacing a portion of the polymer.
- Colorants: Dyes and pigments allow for product color customization, making the end products more appealing to consumers without complicating the manufacturing process.
- Stabilizers: These additives target environmental degradation factors such as UV radiation or oxidative stress. They prolong the lifespan of the final products.
- Impact Modifiers: Certain additives improve the product's toughness and impact resistance, essential for products exposed to rigorous use.
- Processing Aids: These include anti-adhesion agents and lubricants that enhance process efficiency and product quality during the moulding operations.
The careful selection of additives and fillers can lead to improved product performance and satisfaction in the end-use applications. Thus, they play an integral role in the blowing injection moulding process.
Applications of Blowing Injection Moulding
The applications of blowing injection moulding are diverse and significant in modern manufacturing. This technique's ability to produce hollow components efficiently makes it indispensable in various industries. Understanding these applications helps appreciate the relevance and potential of this manufacturing process. Here, we will explore specific sectors such as consumer goods, industrial products, and medical devices.
Consumer Goods
In the realm of consumer products, blowing injection moulding offers remarkable advantages. It facilitates the production of items that require lightweight yet durable characteristics. Common products include containers, toys, and packaging materials. The versatility of blowing injection moulding allows for a wide range of shapes and sizes, meeting varying consumer demands.
The consumer market often emphasizes aesthetics and functionality. Therefore, blowing injection moulding enables manufacturers to integrate designs that appeal to consumers while ensuring durability. Additionally, the use of different polymers can enhance the product's quality, leading to better performance in everyday use.
Industrial Products
Blowing injection moulding is equally critical in the production of industrial products. This method is employed to create various containers, tanks, and parts used in machinery. The industrial sector values robustness and resistance to environmental factors, and blowing injection moulding meets these specifications effectively.
Applications in this area also include creating parts that must withstand high-stress conditions. Using specific materials can enhance thermal and chemical resistance, which is paramount for industrial use. Besides, the efficiency in mass production helps companies meet large-scale demands without compromising on quality.
Medical Devices
The medical sector has unique requirements for components, and blowing injection moulding plays a vital role here. This technique is applied in the manufacturing of items such as bottles for pharmaceuticals or intricate components for medical devices. Quality, precision, and safety are the utmost priorities in medical applications, making this moulding process highly relevant.
Blowing injection moulding ensures compliance with stringent regulations in healthcare. Materials used in this context often require biocompatibility and resistance to sterilization processes. As such, selecting suitable polymers is crucial, and advancements in the field continue to support innovation in medical technology.
"Blowing injection moulding provides cost-efficient solutions across various industries, demonstrating its versatility and adaptability in meeting distinct application needs."
As we can see, blowing injection moulding serves multiple crucial roles across different sectors. Its ability to create hollow plastic components efficiently addresses the specific needs of each industry, making it a versatile and valuable manufacturing process.
Comparative Analysis with Other Moulding Techniques
In the domain of plastic manufacturing, various moulding techniques exist, each with its distinct procedures and applications. The analysis of blowing injection moulding in relation to other methods such as blow moulding and injection moulding is crucial. This examination underscores the unique advantages and limitations of blowing injection moulding. Understanding these comparisons helps professionals in selecting the most appropriate method for a specific production need.
Blow Moulding
Blow moulding primarily focuses on forming hollow plastic parts. This method uses air pressure to inflate a heated plastic tube, turning it into a hollow shape when it cools. The process is effective for producing containers, such as bottles or tanks, that require a simple hollow geometry. However, blow moulding does not allow for intricate designs or complex features on the moulded part.
- Strengths of Blow Moulding:
- Limitations of Blow Moulding:
- Simplicity: Relatively uncomplicated process for producing hollow items.
- High Production Rates: Capable of producing large quantities quickly.
- Design Constraints: Lacks the capacity for precision and detail in intricate designs.
- Material Restrictions: Typically limited to certain types of thermoplastics suitable for the process.
Blowing injection moulding offers a more versatile approach. It combines injection moulding’s ability to create complex shapes with the blowing process’s efficiency for hollow items, thus enabling the production of sophisticated designs.
Injection Moulding
Injection moulding is a dominant technique in the plastics industry for items that require precision and detailed geometries. The process involves heating plastic, injecting it into a mould, and allowing it to cool and solidify. This method excels in producing high-accuracy components.
- Strengths of Injection Moulding:
- Limitations of Injection Moulding:
- High Detail and Precision: Capable of creating complex shapes with tight tolerances.
- Material Versatility: Compatible with a wide range of thermoplastics and thermosets.
- Production Speed: Slower compared to blow moulding in specific applications due to cooling times.
- Higher Initial Costs: Significant investments required for mould creation.
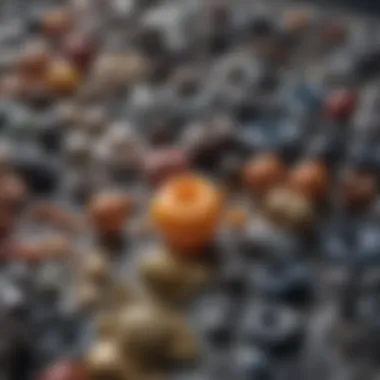
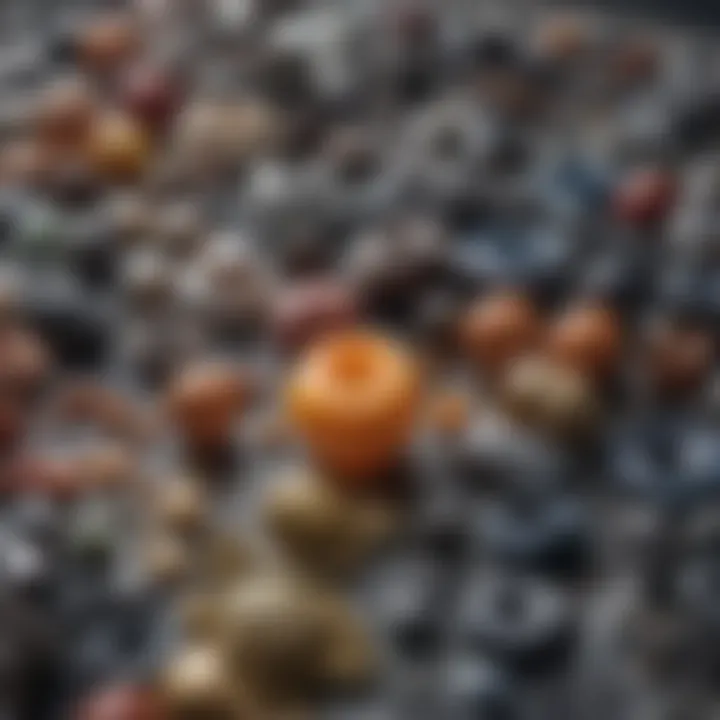
Blowing injection moulding sits between these two methods. It employs the detail-oriented precision of injection moulding while maintaining the production speed for hollow shapes of blow moulding. Through this process, manufacturers can achieve a balance of speed, cost-effectiveness, and design complexity that neither traditional blow moulding nor injection moulding alone can deliver.
Advantages of Blowing Injection Moulding
The advantages of blowing injection moulding are critical to understanding its role in modern manufacturing. This section seeks to clarify the benefits that make this process increasingly popular among companies that produce plastic items. From cost considerations to rapid production, these advantages highlight why professionals are drawn to this technique.
Cost Efficiency
Cost efficiency is a primary consideration for manufacturers in any sector. Blowing injection moulding combines the strengths of injection and blow moulding to optimize resource usage. The ability to create complex hollow forms with minimal waste is particularly noteworthy.
- Material usage: The process often requires less material compared to other methods. This is due to the fact that blowing injection moulding produces thin walls effectively, reducing the amount of raw materials needed.
- Operational expenses: With modern machines capable of higher output levels, the ongoing costs associated with production can decrease significantly. This is beneficial for both large-scale and smaller operations. The upfront investment in high-quality blowing injection moulding machines may yield long-term savings through efficiency improvements.
- Lower energy consumption: This manufacturing process can also lead to lower energy costs. The machines generally require less time to heat the materials than traditional injection moulding methods, reducing energy expenditure.
Due to these factors, the technique presents an attractive option for businesses aiming to reduce costs while maintaining quality.
Production Speed
Production speed is another key advantage of blowing injection moulding. In an age where time to market is paramount, the speed of the blowing injection moulding process fits well with tight deadlines.
- Rapid cycle times: Machines can complete production cycles quickly, allowing for high-volume outputs in a shorter period. This is both beneficial for meeting customer demands and for scaling operations efficiently.
- Streamlined processes: The integrated nature of blowing injection moulding means that fewer separate steps are needed in the manufacturing process. This reduces the potential for delays and errors, leading to a smoother operation overall.
- Flexibility in design: The ability to adapt designs swiftly without substantial downtime can lead to quicker updates to products. For companies facing changing market needs, this capability is essential.
Overall, the combined influence of cost efficiency and production speed makes blowing injection moulding an advantageous choice for many manufacturers in the plastic industry. As companies look for ways to enhance their operations, these factors should not be overlooked.
Challenges in Blowing Injection Moulding
The blowing injection moulding process holds promise for producing hollow plastic components efficiently. However, it is not without its hurdles. Understanding the challenges in this field is crucial as it influences design decisions, material selection, and overall production quality. By addressing these specific elements, manufacturers can enhance productivity and ensure product durability while reducing wastage.
Material Limitations
One of the primary challenges in blowing injection moulding is the selection of suitable materials. Not all polymers can withstand the complexity of the process. Key limitations include:
- Thermal Properties: Many polymers have specific thermal thresholds. If these are exceeded, the material may degrade or lose its mechanical integrity during the moulding process. A consistent temperature is essential.
- Viscosity Levels: The flow characteristics of materials determine their suitability. High viscosity materials may not flow well in the injection phase. This could lead to incomplete filling of moulds.
- Brittleness: Some materials may become brittle when cooled too rapidly. As a result, products can fracture during demoulding or use.
- Additives Compatibility: Incorporating additives can sometimes create an adverse reaction within the polymer matrix, leading to inconsistencies in the final product.
These material limitations necessitate extensive testing and evaluation, ensuring the chosen polymers align with the desired application. Many manufacturers must invest time in research to find materials that can effectively balance durability and flexibility.
Technical Constraints
Technical constraints encompass several aspects of the machinery and processes involved in blowing injection moulding. These may create barriers to achieving optimal productivity. Common technical challenges include:
- Machine Calibration: Precision in machine setup is crucial. Any misalignment can lead to inefficiencies in the blowing and injection phases. Regular maintenance and calibration are essential for consistent output.
- Mould Design Complications: Designing an efficient mould that ensures proper cooling and flow is complex. Poor designs can cause uniformity issues in the product, ultimately affecting quality.
- Cycle Time Management: The balance between speed and quality can be challenging. Reducing cycle time might compromise the integrity of the moulded product. This necessitates careful timing and monitoring of each stage in the process.
- Scalability Issues: As production demands grow, scaling operations without compromising quality becomes difficult. Adjustments in machinery or practices may lead to disruption and quality variances.
Addressing these technical constraints requires a deep understanding of both the machinery involved and the materials being used. Continuous innovation and adaptation are vital to overcoming these hurdles effectively.
Future Trends in Blowing Injection Moulding
The landscape of blowing injection moulding is evolving due to advancements in technology and growing environmental consciousness. Understanding future trends is crucial for industry stakeholders as it shapes innovation and market dynamics. Companies that adapt to these trends can optimize production, enhance product quality, and achieve sustainability.
Technological Innovations
Technological advancements play a pivotal role in the future of blowing injection moulding. Several innovations are expected to transform this field substantially:
- Automation and Robotics: The integration of robotics into machinery streamlines operations. Automated systems increase precision, reduce human error, and elevate safety during the production process. The use of robotics in loading materials and handling products will enhance production efficiency.
- Smart Manufacturing: With the rise of Industry 4.0, smart manufacturing techniques are being adopted. Machines equipped with IoT technology allow real-time monitoring of processes and performance metrics. Predictive maintenance can minimize downtime by identifying potential issues before they occur.
- Improved Simulation Software: Advanced simulation software enhances design and testing processes. Engineers can visualize the moulding process and predict potential problems without physical prototypes. This not only reduces material waste, but also accelerates product development.
These advancements make the production process more efficient and sustainable in the long term, which will likely become a standard in blowing injection moulding.
Sustainability Initiatives
Environmental concerns are paramount in today’s manufacturing landscape. The blowing injection moulding sector is adopting sustainability initiatives to mitigate its environmental footprint. Some key considerations include:
- Material Recyclability: Manufacturers are increasingly using materials that are more easily recyclable. Integrating recycled plastics into the production process helps conserve resources and reduce waste. This aligns with global efforts to promote a circular economy.
- Energy Efficiency: New machines are designed to consume less energy. Implementing energy-efficient technologies reduces operational costs and contributes to lower carbon emissions. Companies are encouraged to pursue certifications recognizing energy-efficient practices.
- Reducing Emissions: Companies are striving to minimize their emissions during production. This includes improving the ventilation systems in factories and optimizing manufacturing processes. These changes can significantly reduce overall environmental impact.
- Sustainable Supply Chains: Emphasis on ethical sourcing of materials is growing. More manufacturers are focusing on sourcing raw materials from sustainable and certified suppliers, ensuring that environmental standards are met throughout the supply chain.
"Sustainability is not just a trend; it's the future direction in manufacturing. Failure to adopt these practices may lead to reduced market share and relevance."
By embracing these initiatives, the blowing injection moulding industry can ensure its longevity and adaptability in a rapidly changing world.
Environmental Implications of Blowing Injection Moulding
Understanding the environmental implications of blowing injection moulding is vital in today’s industrial landscape. As the world shifts towards sustainability, industries are compelled to consider the environmental impact of their operations. Blowing injection moulding, which produces hollow plastic products, is not exempt from these considerations. By focusing on waste management and resource utilization, this section highlights how this moulding technique can align with global sustainability goals.
Waste Management Strategies
Effective waste management strategies are essential in reducing the environmental footprint of blowing injection moulding. Key strategies include:
- Material Recovery: Striving to recover and reuse scrap materials can significantly reduce waste. Many manufacturers implement systems to collect and process off-cuts, thereby minimizing material loss.
- Recycling Programs: Establishing recycling protocols encourages the return of defective or obsolete products. This helps in converting waste back into usable material, promoting a circular economy.
- Technology Upgrades: Investing in advanced machinery that allows for better precision can decrease waste during production. Enhanced efficiency leads to less material being discarded.
The challenge remains in ensuring that these strategies are not only adopted but embedded into the culture of the organization. Companies must commit to continuous improvement in waste management to achieve notable environmental benefits.
Life Cycle Assessment
A life cycle assessment (LCA) is a crucial method to analyze the environmental impact of blowing injection moulding. It provides a comprehensive evaluation from raw material extraction to the end of a product's life. The components of LCA in this context include:
- Raw Material Extraction: Assessing the environmental cost of extracting materials used in blowing injection moulding is the first step. This includes the carbon footprint and resource depletion associated with materials like polyethylene.
- Production Phase: Evaluating the energy usage and emissions during the manufacturing process is essential. Understanding where emissions occur and identifying ways to reduce them can lead to significant advancements in sustainability.
- Use Phase: The duration and manner in which a product is used also impacts its environmental footprint. Products designed for efficiency and durability tend to have lighter life cycle impacts.
- End-of-Life Disposal: Finally, analyzing how products are disposed of at the end of their lifecycle is critical. Effective strategies, such as biodegradability and recyclability, can significantly reduce the ecological impact.
Through rigorous LCAs, stakeholders can make informed decisions regarding materials and processes, enhancing the sustainability of blowing injection moulding operations. Overall, acknowledging these environmental considerations can lead to improved practices that are beneficial for the industry and the planet.
Quality Control in Blowing Injection Moulding
Quality control plays a crucial role in the blowing injection moulding process. It ensures that every product meets the industry standards and customer expectations. Maintaining high-quality output minimizes defects and maximizes efficiency. By implementing robust quality control measures, manufacturers can safeguard their reputation and ensure user satisfaction. In the context of blowing injection moulding, several specific elements come into focus.
Reliable quality control provides multiple benefits:
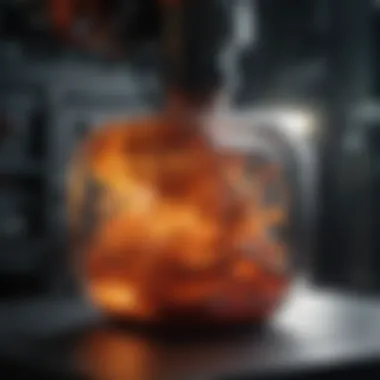
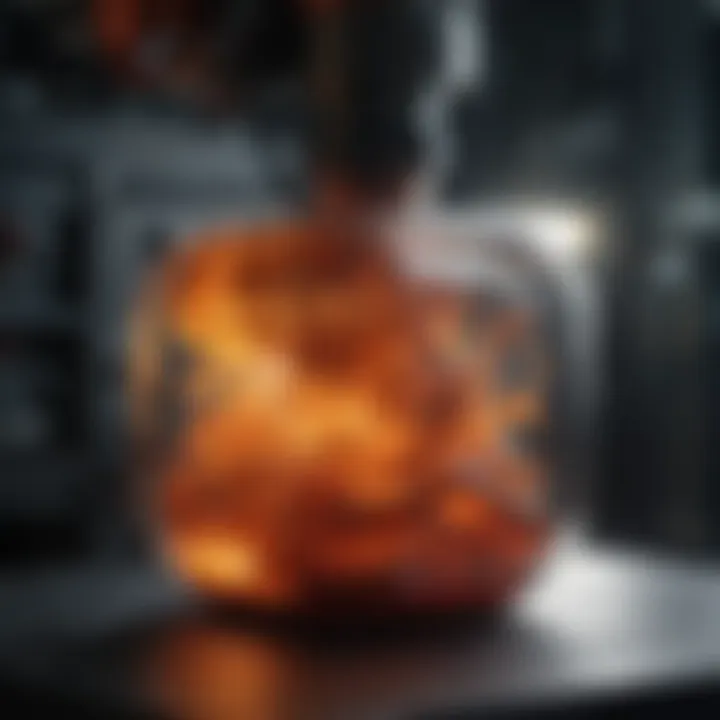
- Consistency: Ensures each product is uniform in size, shape, and quality.
- Defect Identification: Helps in early detection of issues, preventing extensive production of faulty items.
- Cost Savings: Reduces waste and rework costs, leading to better profitability.
Quality control also involves specific considerations tailored to the unique aspects of the blowing injection moulding process. Evaluating the machinery, monitoring material properties, and final product testing form the core of effective quality management.
Standard Testing Procedures
Standard testing procedures are essential to quality control in blowing injection moulding. These procedures help verify the performance and reliability of both the machinery and the final products. The following are common testing protocols:
- Material Testing: Ensures that raw materials meet the required specifications. Properties like tensile strength, flexibility, and thermal stability are assessed.
- Injection Cycle Monitoring: Examines the consistency of mould cycles to identify any variations that may lead to defects.
- End-Product Testing: Involves functional testing, where the finished products are checked for durability and performance under expected use conditions.
These testing processes are structured to provide clear insights into product viability, supporting the ongoing refinement of production techniques.
Defect Analysis
Defect analysis focuses on identifying root causes of issues that arise during the blowing injection moulding process. A systematic approach to analyzing defects can guide manufacturers in improving production outcomes. Key steps in defect analysis include:
- Data Collection: Gathering data on defective products, noting patterns or anomalies in the defects.
- Root Cause Identification: Using tools such as fishbone diagrams or failure mode effects analysis (FMEA) to determine the source of defects.
- Corrective Actions: Implementing changes based on analysis findings, which might involve adjusting machinery settings, improving training, or refining material choice.
By focusing on defect analysis, manufacturers can enhance the reliability and quality of their products. Furthermore, keeping a systematic record of defects and analysis results helps in developing a knowledge base for future productions, thus continuously improving the blowing injection moulding process.
Economic Considerations in the Industry
The economic factors in the blowing injection moulding industry play a vital role in shaping its growth and sustainability. Understanding these factors is crucial for industry stakeholders, including manufacturers, suppliers, and investors. This section examines market dynamics and investment opportunities, showing how they influence decision-making and strategic planning.
Market Dynamics
Market dynamics in the blowing injection moulding field are affected by supply and demand, competition, and technological advancements. The demand for lightweight and durable plastic products is increasing across various sectors. This includes automotive, consumer goods, and packaging. Such trends drive the growth of blowing injection moulding.
Additionally, manufacturers must stay competitive. They have to keep costs low while maintaining high quality. Factors like raw material prices, labor costs, and operational efficiency are key considerations that directly affect pricing strategies and profitability.
The rise of e-commerce also impacts market dynamics. Online shopping has increased the need for efficient packaging solutions, driving innovation in blowing injection moulding processes. Manufacturers must adapt quickly to changing consumer preferences and ensure their products meet market needs.
Market research is essential for understanding these trends. Regular analysis enables companies to anticipate market shifts and adjust their business models accordingly.
Investment Opportunities
The blowing injection moulding industry presents numerous investment opportunities. As demand rises, firms can invest in new technologies that improve efficiency and output quality. Automation and smart manufacturing technologies are areas where investments can lead to significant returns.
Furthermore, sustainability initiatives are gaining traction. Investors increasingly prefer companies that implement eco-friendly practices and materials. For example, investing in bio-based plastics or recycling technologies not only meets regulatory demands but also attracts environmentally conscious consumers. This shift creates a dual benefit of meeting market expectations while enhancing brand reputation.
- Key Areas for Investment:
- Technological advancements in machinery.
- Development of sustainable materials.
- Research and development initiatives.
Regulatory Framework Governing Blowing Injection Moulding
Understanding the regulatory framework surrounding blowing injection moulding is vital for several reasons. First, regulations ensure that the manufacturing processes meet safety and quality standards. This is especially important since the products produced can affect consumer safety and environmental sustainability. Compliance with these regulations can also enhance the manufacturer’s reputation, leading to increased consumer trust and potentially higher sales.
Industry Regulations
Industry regulations pertain to the established standards that govern the production and materials used in blowing injection moulding. Such regulations can vary depending on the geography of operation. In the United States, for example, the Occupational Safety and Health Administration (OSHA) provides guidelines to ensure workplace safety around potentially hazardous materials used in this process. Adhering to regulations like these not only protects workers but also minimizes the risk of accidents that can lead to costly downtime for manufacturers.
Furthermore, industry-specific bodies may set additional regulations, especially for sectors like medical devices. The Food and Drug Administration (FDA) regulates the use of certain materials in medical applications, imposing stringent controls over how these products are manufactured and tested. By adhering to such regulations, companies can protect consumers and their own interests.
Compliance Standards
Compliance standards are a set of benchmarks that manufacturers must meet to ensure that their products are safe and reliable. In blowing injection moulding, these standards encompass various aspects, including material properties, product design, and the manufacturing process itself.
Typically, compliance standards align with international norms, such as the International Organization for Standardization (ISO) regulations. For instance, ISO 9001 focuses on quality management systems to enhance customer satisfaction and ensure regulatory compliance. Meeting these standards often requires comprehensive documentation and traceability throughout the production process.
Meeting compliance standards also proves beneficial when accessing global markets. Many countries have strict import regulations, which can include proof of compliance with specific standards. Thus, manufacturers that prioritize compliance not only simplify their market entry but also solidify their standing as dependable producers.
Ultimately, regulatory frameworks offer a structured approach to ensure safety, quality, and environmental responsibility in blowing injection moulding, reflecting a commitment to excellence in production.
Case Studies in Blowing Injection Moulding
Case studies play a vital role in understanding blowing injection moulding. They provide real-world examples of how this technique is applied across various industries. By examining these cases, students, researchers, and professionals can gather insights into practical challenges, innovative solutions, and the overall effectiveness of this manufacturing method. Not only do case studies showcase successful applications, but they also highlight lessons that can be learned from projects that did not go as planned.
Successful Applications
Successful applications of blowing injection moulding demonstrate its versatility and efficiency. Various sectors have adopted this process for producing hollow plastic items. Here are some key examples:
- Beverage Containers: Companies like Coca-Cola and Pepsi use blowing injection moulding to create lightweight and durable PET bottles. This process reduces material usage while ensuring strength and rigidity, crucial for holding carbonated beverages.
- Automotive Parts: Automotive manufacturers employ blowing injection moulding for components such as fuel tanks and exterior panels. These parts benefit from the ability to form complex shapes and maintain structural integrity, contributing to vehicle safety and performance.
- Consumer Products: Brands like Procter & Gamble use this technique to manufacture bottles for household cleaning products. The lightweight nature of blown injection moulded containers helps reduce shipping costs and enhances user convenience.
Lessons Learned
From various case studies, several lessons emerge that are beneficial for professionals in the field:
- Material Selection: The choice of polymer significantly influences the outcome. Specific applications may require different materials. For instance, using high-density polyethylene (HDPE) for containers ensures durability, while using polystyrene may allow for finer detail in designs.
- Process Optimization: Many successful case studies emphasize the importance of optimizing process parameters. Factors such as temperature control and pressure settings play a crucial role in the quality of the final product. An iterative approach to refining these variables often yields higher precision and consistency.
- Sustainability Practices: Some companies have integrated sustainable practices into their production processes. Reusing materials or integrating bio-based resins not only reduces waste but also appeals to environmentally conscious consumers.
"Understanding past applications of blowing injection moulding allows us to refine our future strategies and innovate further."
Closure
The conclusion of this article is essential as it encapsulates the significant insights gained throughout the discussion on blowing injection moulding. Understanding blowing injection moulding is crucial for several reasons. First, this process not only merges the advantageous aspects of injection moulding and blow moulding but also offers a unique approach to creating hollow plastic products that are integral to various industries. The techniques discussed provide clarity on how these processes operate together, ensuring that manufacturers can find the most efficient solutions for their production needs.
Summary of Key Points
Throughout this article, we have highlighted multiple facets of blowing injection moulding.
- The fundamental principles underlying the process are essential for grasping its functionality.
- Material selection and understanding the dynamics of polymer behavior are vital for optimizing product quality.
- The diverse applications of this molding technique in consumer goods, industrial products, and medical devices demonstrate its versatility.
- Key advantages such as cost efficiency and heightened production speed are crucial for businesses looking to enhance their manufacturing capabilities.
- Additionally, challenges such as material limitations and technical constraints need to be addressed for continued innovations in the sector.
- The future trends indicate that technological advancements and sustainability initiatives will shape the landscape of blowing injection moulding.
The importance of these aspects cannot be overstated. They not only highlight the profitability of embracing this manufacturing technique but also suggest that organizations need to stay updated with regulatory frameworks and market dynamics to remain competitive.
Future Outlook
Looking ahead, the field of blowing injection moulding is likely to witness substantial growth and innovation.
- The technological innovations on the horizon suggest that automation and smart manufacturing processes will streamline operations, ultimately enhancing efficiency and product quality.
- Sustainability initiatives, driven by the increasing need to address environmental concerns, are expected to play a pivotal role in shaping manufacturing practices.
- Companies are likely to invest in bioplastics and recycled materials, pushing the industry toward more responsible production methods.