In-Depth Analysis of Gas Processors and Their Impact
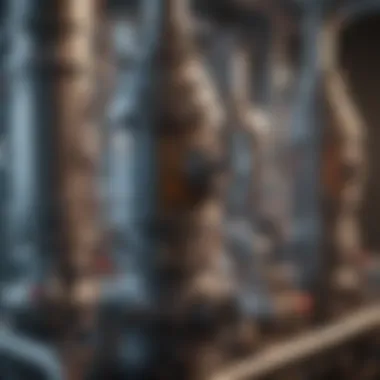
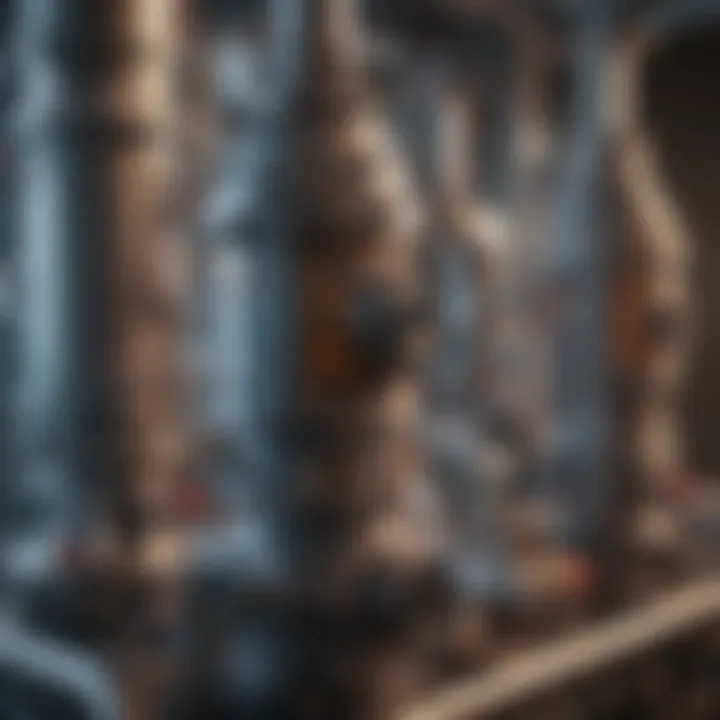
Intro
Gas processors are pivotal in the energy sector, facilitating the transformation and purification of gases for various applications. Through an intricate blend of technology and engineering, these systems handle the extraction of valuable components from gas streams, ensuring efficiency and sustainability in operations. Understanding gas processors encompasses several aspects, from their operational mechanisms to their implications for the environment and the economy.
As industries advance, the importance of optimizing gas processing becomes even more significant. This article aims to provide a thorough examination of gas processors, focusing on their mechanisms, recent advancements, and practical applications across different sectors. Such knowledge serves not only academic purposes but also aids professionals in making informed decisions within the field.
Key Findings
Major Results
- Gas processors serve a critical role in natural gas and petrochemical industries.
- Recent technological advancements have significantly improved efficiency and reduced emissions.
- There is a marked trend towards sustainability, with a focus on integrating renewable energy sources.
Understanding gas processors reveals a complex interplay between technology, efficiency, and environmental concerns. The future of gas processing is poised to evolve, incorporating innovative methods to increase recovery rates and minimize waste.
Discussion of Findings
The analysis indicates that the advancements in gas processing technologies are not only enhancing production but are also crucial to regulatory compliance. The reduction of carbon footprints continues to gain importance. As industries become more aware of their environmental impact, adopting sustainable practices becomes essential. Companies that innovate in this area will likely gain a competitive edge.
Methodology
Research Design
This article employs a qualitative research design, synthesizing information from various credible sources including academic journals, industry reports, and expert analyses. This approach allows for a comprehensive understanding of the mechanisms and technology behind gas processors.
Data Collection Methods
Research data was collected from a variety of methods including:
- Literature reviews of scholarly articles and publications
- Interviews with industry experts to provide first-hand insights
- Case studies of successful gas processing implementations
The integration of these data collection methods ensures the reliability and depth of the analysis presented in this article.
"Gas processing technology is advancing rapidly, and understanding its implications is crucial for future developments in energy efficiency."
Through an exploration of gas processors, this article aims to inform and educate students, researchers, and professionals, providing insights into the complex dynamics of the energy landscape.
Prelims to Gas Processing
Gas processing plays a critical role in the energy sector by ensuring that the gas extracted from the earth is refined and treated to meet specific quality standards required for various applications. Without effective gas processing mechanisms, the utility of natural gas as a clean, efficient energy source would be severely diminished. This section emphasizes the essential principles behind gas processing and its significance in facilitating energy efficiency and environmental protection.
Definition and Importance
Gas processing refers to the series of physical and chemical processes that treat raw natural gas to remove impurities, separate valuable components, and ensure compliance with industry specifications. This process is important for several reasons:
- Quality Enhancement: The primary goal is to improve the quality of the gas. Raw natural gas often contains impurities such as water vapor, carbon dioxide, and hydrogen sulfide. Eliminating these substances makes the gas suitable for commercial use.
- Maximize Yield: Well-implemented processing can maximize the yield of commercially valuable products. For example, processing can separate ethane from natural gas, which can be used as a feedstock in the petrochemical industry.
- Safety: Certain impurities can pose significant risks, potentially leading to failures in pipelines or combustion processes. Proper gas processing reduces these risks.
- Regulatory Compliance: Many regions impose stringent standards on the quality of gas. Effective processing ensures that the gas meets local regulations, facilitating smoother trade operations.
The importance of gas processing extends beyond immediate economic benefits; it also contributes to the overall sustainability of energy production.
Historical Background
Gas processing has evolved substantially since the late 19th century when natural gas was first utilized as an energy source. Initially, processing methods were rudimentary, focusing mainly on the removal of water and basic contaminants. As the demand for cleaner and more efficient energy sources grew, so did the technology involved in gas processing.
In the early 20th century, with the advent of commercial natural gas utilization, innovations such as absorption and adsorption methods emerged. By the mid-20th century, cryogenic processing methods were developed to separate ethane, propane, and butane from natural gas, adding significant value to extracted resources.
With increasing environmental awareness and regulatory pressure, advancements have accelerated, leading to the adoption of numerous sophisticated techniques today. Such techniques not only enhance gas quality but also minimize energy consumption and environmental impact.
In summary, the historical development of gas processing reflects an ongoing quest for efficiency, safety, and sustainability. As we continue into an era of rapid technological change and environmental awareness, understanding the principles of gas processing becomes increasingly vital.
Fundamentals of Gas Processing Technology
Gas processing technology is essential in the transformation of natural gas from a raw state into a marketable product. Understanding the foundational principles surrounding this technology is vital for anyone interested in the energy sector. It involves a series of processes designed to remove impurities and separate valuable hydrocarbons, which maximize the efficiency and minimize the environmental impact of gas production.
Basic Principles of Gas Processing
The principles of gas processing revolve around several key methodologies. At its core, gas processing entails separation and purification.
- Separation of Components: Gas processors must effectively separate various components, including methane, ethane, propane, and other heavier hydrocarbons. This process often utilizes physical and chemical methods, depending on the specific characteristics of the gas.
- Removal of Contaminants: Natural gas often contains water vapor, hydrogen sulfide, carbon dioxide, and other contaminants. The removal of these substances is critical, ensuring the gas meets quality specifications for transmission and sale. Technologies such as absorption and adsorption are typically employed for this purpose.
- Phase Behavior: Understanding the phase behavior of gases is crucial. At varying temperatures and pressures, components may exist in different states. Gas processors must account for these changes to optimize efficiency in separation.
- Thermodynamics: The principles of thermodynamics play a vital role in the efficiency of gas processing operations. Processes are designed to harness heat transfer and pressure variations to facilitate component separation and energy recovery.
Key Components of Gas Processors
The functionality of gas processors is largely attributed to specific components, each designed to fulfill critical roles.
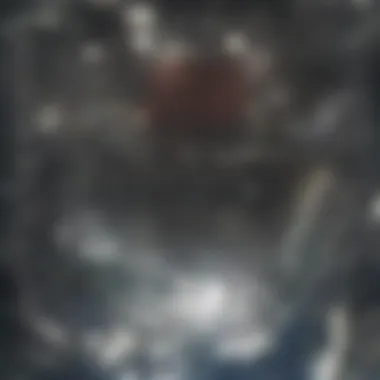
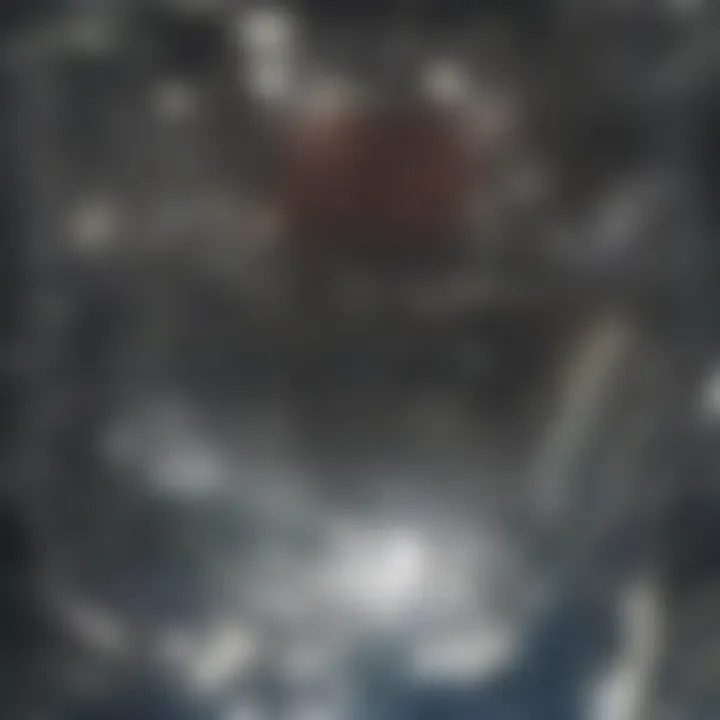
- Compressor: Increases the pressure of gas, allowing it to flow through the processing system efficiently. The design of compressors affects the overall energy consumption of the processing plant.
- Heat Exchanger: Transfers heat between different gas streams, optimizing thermal efficiency and enhancing the separation process.
- Absorbers: Utilized to remove acid gases, such as carbon dioxide and hydrogen sulfide, through chemical reactions with absorbent liquids.
- Strippers: Work in conjunction with absorbers to regenerate the absorbent solution, allowing the process to continue efficiently.
- Adsorbers: These units utilize solid materials to attract and capture undesired components, such as moisture and specific hydrocarbon fractions.
- Control Systems: Advanced control systems manage the operations of gas processing plants, ensuring safe and efficient processes while maximizing output.
Understanding these principles and components is crucial for evaluating the effectiveness of various gas processing technologies. It is also essential for identifying how innovation can improve efficiency and sustainability in the industry.
"The importance of gas processing can not be understated; it is fundamental to the viability of the natural gas market and its role in the transition to cleaner energy sources."
To sum it up, gas processing technology is grounded in principles that facilitate the effective separation and purification of natural gas. The key components of gas processors enhance this functionality, showcasing the intricate interplay of science and engineering in this essential field.
Types of Gas Processors
Gas processors play a crucial role in the energy industry by ensuring the effective treatment and conversion of natural gas into usable forms. Different types of gas processors are utilized depending on varying requirements, such as the composition of the gas stream, the desired end product, and specific operational conditions. Understanding these types is essential, as each has distinct mechanisms, benefits, and limitations that affect efficiency and cost.
Cryogenic Gas Processors
Cryogenic gas processors operate by lowering the temperature of natural gas to separate components based on their boiling points. This process allows for the efficient removal of heavy hydrocarbons, water, and other impurities. The main benefit of this type of processor is its ability to produce high-purity products, like liquefied natural gas (LNG), which can be easily transported. The efficiency of these processors often leads to reduced operational costs over time.
However, operating cryogenic systems requires significant energy input to achieve the low temperatures necessary for effective separation. Also, the complexity of these systems may require specialized training for staff, raising initial investment costs. The returns can be substantial when managed effectively, as cryogenic processors support many applications in both commercial and residential sectors.
Absorption Gas Processors
Absorption gas processors utilize a liquid solvent to remove specific components from the gas stream. In this process, the gas is passed through a liquid absorbent that selectively captures desired elements, such as carbon dioxide or hydrogen sulfide. The primary advantage of this technology lies in its simplicity and effectiveness for removing contaminants. This attributes to why absorption is a popular choice in many industries.
These processors are usually less energy-intensive compared to cryogenic systems. Additionally, they can be easily integrated into existing plants, minimizing disruption during upgrades or expansions. Despite these benefits, they may require frequent maintenance and can have higher operating costs due to solvent losses.
Adsorption Gas Processors
Adsorption gas processors work by allowing gas molecules to stick to the surface of solid materials, known as adsorbents. Common adsorbents include activated carbon and zeolites. This type of processing is often used for gas drying or for removing trace components from the gas stream. The key benefit here is the flexibility and capacity for customization, allowing for tailored solutions based on varying feed gas properties.
The effectiveness of adsorption is influenced by factors such as temperature, pressure, and the characteristics of the adsorbent. While these systems can be efficient, they are sensitive to operational conditions and may require regular regeneration or replacement of adsorbents to maintain performance. Proper management is essential to optimizing the life cycle of these processors.
"Understanding the unique properties and operations of different gas processors is key to optimizing gas treatment and ensuring operational efficiency."
Operational Mechanisms of Gas Processors
Understanding the operational mechanisms of gas processors is fundamental for comprehending how these systems effectively separate, purify, and transform gas streams. These mechanisms involve a combination of separating techniques and energy recovery methods. This section explores these elements in detail, highlighting their importance in ensuring that gas processors not only function efficiently but also meet the evolving demands of the energy sector.
Separation Techniques
Separation techniques are pivotal within gas processing, enabling the isolation of valuable components from raw gas mixtures. The most applied methods include:
- Cryogenic Distillation: Utilizes low temperatures to condense gases into liquids, allowing for the separation of different hydrocarbons and impurities.
- Absorption: Involves the removal of desired gases using liquid absorbents, which can selectively capture specific components such as carbon dioxide or hydrogen sulfide.
- Adsorption: This technique employs solid materials to adhere to certain gas molecules, thereby facilitating their separation based on size or chemical properties.
- Membrane Separation: Uses semi-permeable membranes to selectively allow certain gases to pass through, separating them from others based on multiple factors, such as molecular size or polarity.
These techniques play a crucial role in optimizing gas quality and purity, impacting downstream applications significantly. Higher purity levels enhance product value and minimize environmental harm, aligning gas processing operations with regulatory expectations.
Energy Recovery Systems
Energy recovery systems represent another important mechanism in gas processing. These systems are designed to capture and utilize the energy that would otherwise be wasted during processing. Key components of energy recovery systems include:
- Turboexpanders: Devices that convert the energy from high-pressure gas into mechanical energy, which can be used to generate electricity or drive compressors in the system.
- Heat Recovery Steam Generators (HRSG): These systems capture waste heat from the gas processing operation to produce steam, thus improving overall process efficiency.
- Thermal Oil Systems: These systems use heat exchangers to transfer heat away from the gas stream, leading to better thermal management.
Incorporating energy recovery systems leads to significant cost reductions and lower emissions. Efficient energy management not only improves the bottom line but also contributes to sustainability efforts in the industry.
The integration of effective separation techniques and energy recovery systems enables gas processors to maximize output while minimizing environmental impact.
In summary, the operational mechanisms of gas processors include both separation techniques and energy recovery systems, each playing a crucial role in gas processing efficiency and effectiveness. By investing in these technologies, operators can achieve higher purity levels and greater energy efficiency, essential factors in the competitive gas processing market.
Gas Processing in Energy Sector
Gas processing plays a pivotal role in the energy sector, serving as the bridge between raw natural gas extraction and its final utilization. The effectiveness of gas processing directly impacts the environmental sustainability of energy production, making it a critical area of interest for researchers and industry professionals. By ensuring the purity and quality of natural gas, gas processors enable the safe and efficient delivery of energy.
Role in Natural Gas Production
Natural gas is a prevalent source of energy globally. Its extraction and processing involve several steps, each enhanced by advanced gas processing technologies. The role of gas processing in natural gas production can be summarized in various contributions:
- Removal of Impurities: Natural gas typically contains water vapor, carbon dioxide, hydrogen sulfide, and other hydrocarbons. Gas processors apply separation techniques to eliminate these contaminants, enhancing gas quality and meeting pipeline specifications.
- Composition Adjustment: The energy content of natural gas can vary based on its composition. Processes such as fractionation allow for the tailoring of gas to specific energy standards, ensuring compatibility with end-user requirements.
- Efficiency in Extraction: Gas processing systems improve the overall efficiency of natural gas extraction. For example, the integration of absorption technology can increase the recovery rate of methane, allowing operators to maximize production output without incurring excessive costs.
The synergistic effect of effective gas processing leads to a more reliable energy supply and supports the transition toward cleaner fuel sources, especially in an era of increasing environmental regulation.
Integration with Downstream Processes
The integration of gas processing with downstream processes is a defining characteristic of modern energy supply chains. This integration ensures that natural gas is not only processed but also efficiently distributed and utilized across various applications. Key aspects of this integration include:
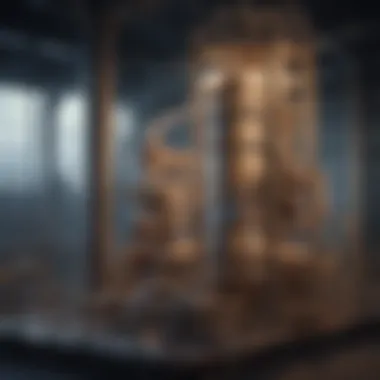
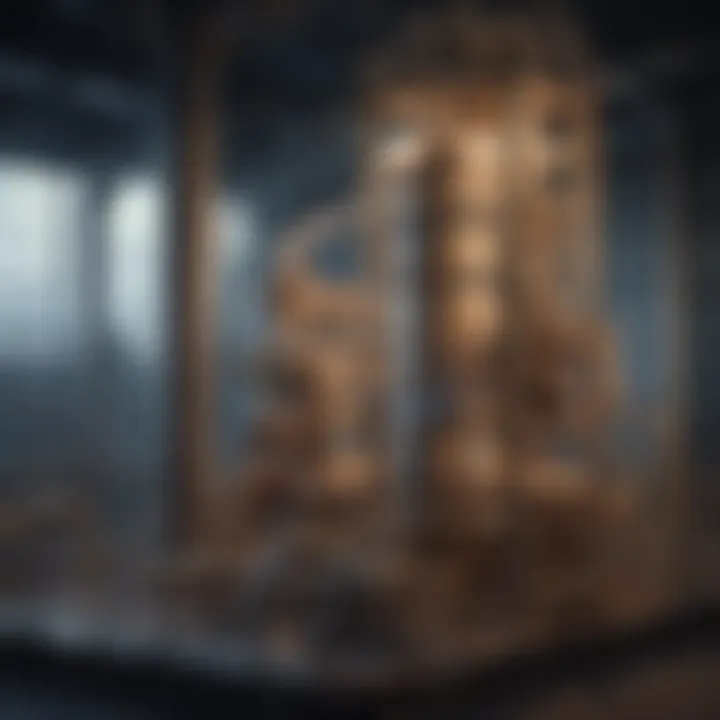
- Pipeline Transportation: After gas processing, the treated gas needs to reach consumers quickly and safely. Efficient pipeline systems are designed to transport processed gas, and they often incorporate technologies that ensure minimal loss during transit.
- End-User Applications: Natural gas finds use in various industries, including power generation, heating, and chemical manufacturing. The processing stage needs to align with these downstream applications to guarantee that consumers receive gas that meets specific purity and performance standards.
- Market Dynamics: The gas processing stage can influence market prices and availability. Understanding the integration between processing technologies and market demands is crucial for industry stakeholders. This adaptability can lead to better management of resources, helping to maintain stable energy costs.
The future of gas processing within the energy sector is closely tied to these integrations, suggesting that advancements in technology can lead to increased productivity and sustainability. As new methods and technologies develop, the industry must prioritize collaborative approaches to address emerging challenges in energy efficiency, environmental impact, and regulatory compliance.
Technological Innovations in Gas Processing
Technological innovations play a vital role in the evolution of gas processing. These advancements have transformed traditional methodologies, enhancing efficiency and sustainability. The gas processing sector is under constant pressure to reduce costs and meet demanding environmental regulations. Innovations lead not only to optimized operational performance but also to breakthroughs that align with broader energy trends. As the industry faces challenges like resource scarcity and climate change, the importance of these innovations cannot be overstated.
Advancements in Efficiency
Advancements in efficiency in gas processing are mainly focused on minimizing waste and maximizing output. By employing newer technologies, companies can achieve higher recovery rates of valuable components from natural gas. For instance, the integration of advanced sensors and control systems in processing plants can optimize the parameters for separating components. Automation, process control, and instrumentation have been refined to allow real-time monitoring of gas quality and flow rates.
Moreover, smaller and more efficient processing units are becoming popular. These units can be modular, which allows for scalability and flexibility in operations. This modularity reduces capital expenditure and enables swift responses to market changes. Ultimately, enhanced efficiency translates to cost savings, creating a more competitive position for gas processors.
Emerging Technologies
Emerging technologies such as membrane separation and hybrid systems represent the forefront of gas processing innovation. Membrane technology allows for precise separation of gases with minimal energy requirements. This technology shows promise for applications such as carbon capture, where it can efficiently separate carbon dioxide from methane.
Another notable development involves the use of cryogenics for gas processing. This technology enables the liquefaction of gases at significantly lower energy costs than traditional methods. Hybrid systems that integrate various processing techniques are opening new avenues for efficiency and improved product quality. Such innovations are likely to shape the future of gas processors, making them more resilient and adaptable.
Digitalization and Automation Trends
The move towards digitalization and automation in gas processing has been accelerated by advances in technology. Companies are adopting digital tools to analyze data, predict maintenance, and improve decision-making processes. Automation frees up human resources for more critical tasks while improving the consistency of processes.
Applications of advanced analytics and machine learning enable predictive maintenance, allowing for a proactive approach to operational issues. Automated systems can identify potential failures before they occur, minimizing downtime. This trend towards digital integration contributes to not only operational efficiency but also safety in processing facilities.
The introduction of digital technologies in gas processing not only increases operational efficiency but also enhances safety and reliability, making the sector more robust to future challenges.
As gas processors embrace these digital trends, the potential for reshaping the entire landscape of gas processing becomes clear. It is an essential shift that should not be underestimated.
Environmental and Regulatory Considerations
The topic of environmental and regulatory considerations is crucial within the scope of gas processing. The operations associated with gas processors have significant implications for eco-system health and regulatory frameworks. As the energy landscape evolves, the gas processing sector faces increased scrutiny regarding its contributions to air pollution and compliance with environmental standards. Hence, discussions on these aspects are imperative.
Impact on Air Quality
Gas processing facilities emit various pollutants that can degrade air quality. These emissions include volatile organic compounds (VOCs), nitrogen oxides (NOx), and sulfur dioxide (SO2). Each of these compounds can contribute to smog formation and negatively affect public health. The relationship between gas processing activities and air quality is complex.
Efforts to mitigate emissions are becoming vital. Many facilities have adopted advanced technologies to filter or altogether avoid harmful emissions in an effort to uphold air quality standards. For example, implementing carbon capture technologies can dramatically reduce the amount of CO2 released into the atmosphere. Additionally, regular emissions monitoring helps keep track of air quality impacts.
"Effective air quality management in gas processing not only meets regulatory standards but also supports community health and safety."
Regulatory Compliance
Regulatory compliance is a cornerstone of sustainable gas processing. Governments around the world impose strict regulations to ensure that gas processors operate within safe environmental limits. Compliance with the Clean Air Act in the U.S. is one such requirement that aims to reduce air pollution from industrial sources. This necessitates that gas processing facilities regularly conduct environmental assessments and adhere to reporting guidelines.
A failure to comply can lead to serious consequences such as heavy fines, operational shutdowns, and reputational damage. Thus, companies in the gas processing industry must develop comprehensive compliance programs. These programs often include:
- Routine Audits: Regular checks on emissions and compliance with safety protocols.
- Training Programs: Educating staff on regulatory requirements and best practices.
- Technological Upgrades: Investing in cleaner technologies to reduce environmental impact.
In summary, understanding environmental and regulatory considerations is essential for the gas processing industry's future. Addressing air quality and maintaining compliance not only helps in protecting the environment but also fosters sustainable business practices.
Future Trends in Gas Processing
The future of gas processing is evolving rapidly, influenced by global shifts towards sustainability, innovation in technology, and increased regulatory demands. Understanding these trends is crucial because they guide how the industry adapts to meet the changing needs of society and the environment. The gas processing sector is at a crossroads and must navigate these future directions to ensure its relevance and efficiency in the energy landscape.
Shift to Sustainable Practices
Sustainability is not just a trend; it is becoming a necessity in gas processing. Companies are increasingly realizing the importance of reducing their carbon footprint. This shift is driven by regulatory pressures and consumer expectations for environmentally friendly practices. Sustainable practices may include using renewable energy sources in operations, optimizing processes to minimize waste, and implementing carbon capture technology.
Moreover, integrating circular economy principles can prove beneficial. This means finding ways to reuse materials and recycle by-products generated during gas processing. Transitioning to sustainable practices does not only enhance corporate image but also leads to potential cost savings and operational efficiencies.
"The transition to sustainable models is reshaping the operational blueprints of gas processors globally."
Efforts in this area can also stimulate innovation, resulting in new technologies and solutions that may redefine how gas is processed. As companies adopt these sustainable methods, consumers can expect higher transparency and accountability regarding energy consumption and sourcing.
Impact of Renewable Energy Integration
The growing integration of renewable energy sources into the gas processing industry is a significant trend. As renewable technologies advance, the synergy between renewable energy and gas processing becomes increasingly evident. For instance, the pairing of wind or solar energy with gas processing facilities can effectively reduce dependency on fossil fuel sources, promoting a cleaner energy output.
Additionally, advancements in hydrogen production as a clean energy vector are becoming vital. As gas processors explore hydrogen derived from renewable sources, they facilitate a shift towards decarbonization. This not only supports global climate goals but also opens new markets for gas processors.
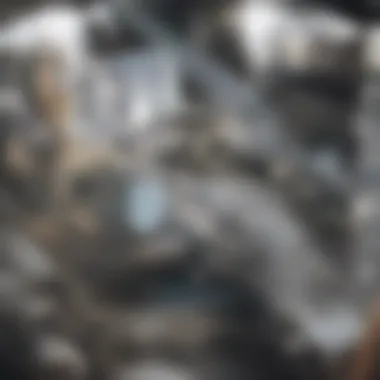
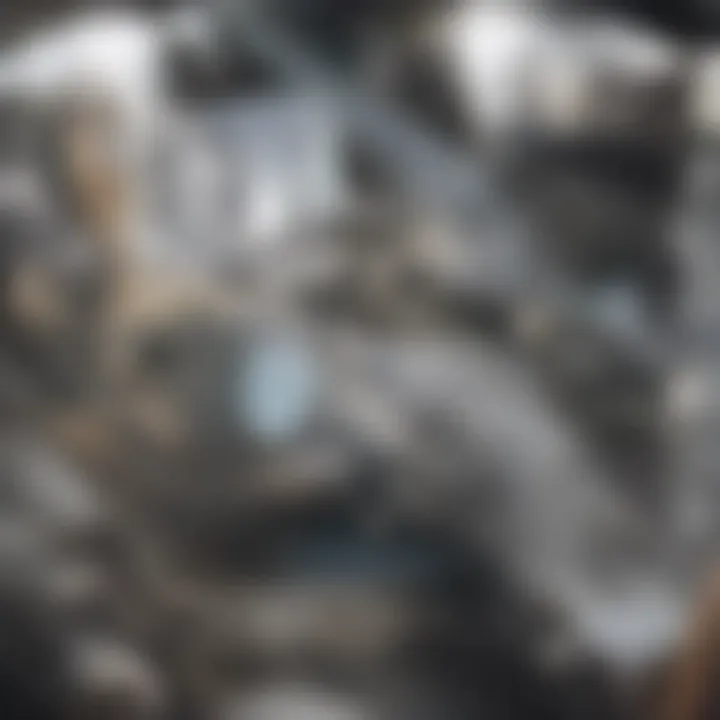
The challenge is to ensure that these renewable integrations are economically viable and not just environmentally sound. Successful adoption will rely on a combination of regulatory support, advancements in technology, and awareness within the industry of the long-term benefits. Evaluating the implications of these changes will help shape future strategies in gas processing.
In summary, navigating through these future trends will require a proactive approach. The focus on sustainable practices and renewable energy integration is essential for driving the gas processing industry forward.
Case Studies of Gas Processors
Case studies play a vital role in understanding the practical applications and effectiveness of gas processors. They provide tangible examples of how different technologies and methodologies are implemented in real-world scenarios. These case studies allow for a detailed examination of successes and failures, providing insights that can be valuable for future projects. Through these detailed analyses, stakeholders can gain a clear perspective on the operational complexities and benefits associated with various gas processing solutions.
Success Stories in Gas Processing
Success stories in gas processing illustrate how innovative technologies and best practices can lead to significant improvements in performance and efficiency. One notable example includes the use of cryogenic gas processors in the liquefaction of natural gas. This technology not only enhances the recovery of marketable gas but also minimizes waste. In facilities such as the Qatar Liquefied Gas Company (Qatargas), state-of-the-art cryogenic technologies have enabled the production of LNG at unprecedented scales while maintaining stringent environmental standards.
"Success in gas processing is about balancing efficiency with sustainability."
In another instance, an absorption gas processing unit implemented by ExxonMobil showcased remarkable efficiency in removing CO2 from natural gas streams. This allowed for the production of cleaner gas that meets stringent regulatory requirements. The successful integration of the latest absorption technologies helped the company reduce operational costs while increasing overall yield. These case studies not only highlight successful implementations but also serve as benchmarks for the industry.
Lessons Learned from Implementations
The lessons derived from gas processing implementations are essential for driving future innovation. One key takeaway is the importance of adapting to site-specific conditions. Each location has its unique challenges, and customizing gas processing technologies can significantly improve outcomes. For example, applying different compressor types based on local geothermal conditions has led to optimized performance in several projects.
In addition, the value of continuous monitoring and data analysis cannot be overstated. Facilities that have adopted digital monitoring systems have reported enhanced operational performance and safety. These systems provide real-time insights into equipment status and process efficiency, leading to timely interventions that prevent unplanned outages.
Furthermore, collaboration with industry peers has proven beneficial as well. Engaging in knowledge sharing and partnerships has resulted in innovations in environmental compliance and operational excellence.
Challenges Facing the Gas Processing Industry
The gas processing industry plays a vital role in ensuring that natural gas is refined to meet safety and quality standards before it is distributed. However, this sector faces numerous challenges that affect its efficiency and sustainability. Addressing these hurdles is crucial for the industry's future.
Technical and Economic Constraints
One primary concern is the technical constraints that exist within gas processing systems. Equipment often requires significant maintenance. Degradation of components can lead to reduced operational efficiency and higher operational costs. Maintaining state-of-the-art technology is also essential, yet it can be prohibitively expensive for many operators.
Economic factors compound these technical issues. Fluctuations in natural gas prices directly influence profitability. In addition to this, investments in new technologies can be a gamble. Companies may hesitate to allocate resources toward innovation. They might worry that the returns will not justify the expense. Furthermore, competition from alternative energy sources creates pressure on gas processors to minimize costs without sacrificing quality or efficiency.
Regulatory frameworks also introduce complexity. Each government has specific regulations that dictate processing methods and environmental compliance. Organizations must navigate these regulations without incurring delays or fines.
To illustrate:
- Increased Operational Costs: Continuous investment is needed for modern equipment.
- Compliance Requirements: Keeping up with changing regulations can stretch resources.
- Competition: The need to lower operational costs to remain competitive complicates profit margins.
These constraints necessitate innovation and strategic planning for gas processing companies to sustain competitive advantage and financial viability.
Future Workforce Preparation
As the industry evolves, so does the requirement for a skilled workforce. The integration of advanced technologies, including automation and data analytics, alters job profiles in this domain. New employees must not only understand traditional gas processing techniques but also be adept in technology-driven processes.
The future workforce should prioritize cross-training. This ensures versatility among employees as operations become more complex. Additionally, educational institutions need to adapt their curricula to include emerging technologies. Programs in engineering, data science, and environmental science will become vital to prepare new graduates for these roles.
Also, mentorship programs could facilitate knowledge transfer from experienced professionals to new recruits. Investing in training and development within organizations helps cultivate the necessary skill sets and can improve employee retention rates.
"Continuous education and training play a key role in bridging the skills gap in the gas processing workforce."
- Interdisciplinary Skills: Graduates should possess a blend of engineering, economics, and environmental knowledge.
- Adaptability: Employees need to be flexible and open to learn new systems and technologies.
- Training Programs: Organizations must commit to ongoing professional development.
By proactively addressing these workforce considerations, the gas processing industry can create a robust foundation that supports its growth and addresses the significant challenges it faces.
Culmination
In the context of this article, the conclusion serves as a pivotal component that synthesizes the findings, reflecting on the intricacies of gas processors and their significant role in contemporary energy landscapes. The importance of articulating a well-rounded conclusion cannot be understated. It provides clarity and encapsulates the essence of the discussions held in preceding sections. Through examining mechanisms, technologies, and applications, this article establishes how gas processors are not merely technical tools, but critical enablers of energy efficiency and environmental stewardship.
Summary of Key Insights
Throughout the exploration of gas processors, several key insights emerged:
- Mechanisms and Functions: Gas processors utilize varied mechanisms such as separation techniques and energy recovery systems, playing a crucial role in extracting and purifying gases.
- Technological Advancements: The evolution in technology enhances both efficiency and sustainability. Innovations such as digitalization and automation are shaping the future landscape of gas processing.
- Environmental Impact: Regulatory compliance and the impact on air quality are paramount considerations. As the industry shifts towards sustainable practices, gas processors must adapt to meet environmental standards.
- Challenges Ahead: The gas processing industry faces both technical and economic challenges that require strategic workforce preparations and adaptable technology solutions.
These insights collectively underscore the dynamic nature of gas processing and its increasing relevance, especially as global energy demands transition towards more sustainable practices.
Final Thoughts on the Gas Processing Landscape
The future of gas processing is a promising yet complex journey. As industries continue to innovate, the integration of renewable energy sources alongside traditional methods highlights the duality of progress and challenge. It is essential for professionals and researchers to stay abreast of these trends, as they will shape the market's operational and technological structure.
Moreover, addressing the challenges in the gas processing industry requires a concerted effort from all stakeholders.
"Gas processors are not just machines; they are vital cogs in the mechanism of modern energy solutions, driving efficiency and compliance with environmental standards."
Engaging with this evolving landscape offers myriad opportunities for innovation and impact. Through foresight and collaborative efforts, the gas processing field can address the pressing energy challenges of today while paving the way for a cleaner, more efficient energy future.