Exploring Aluminum Vapor Deposition Techniques
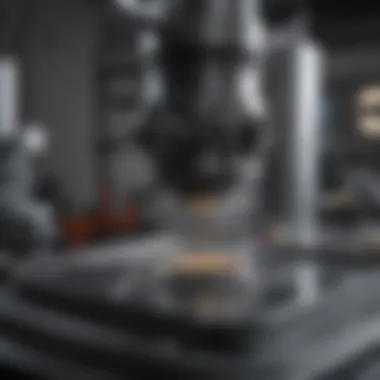
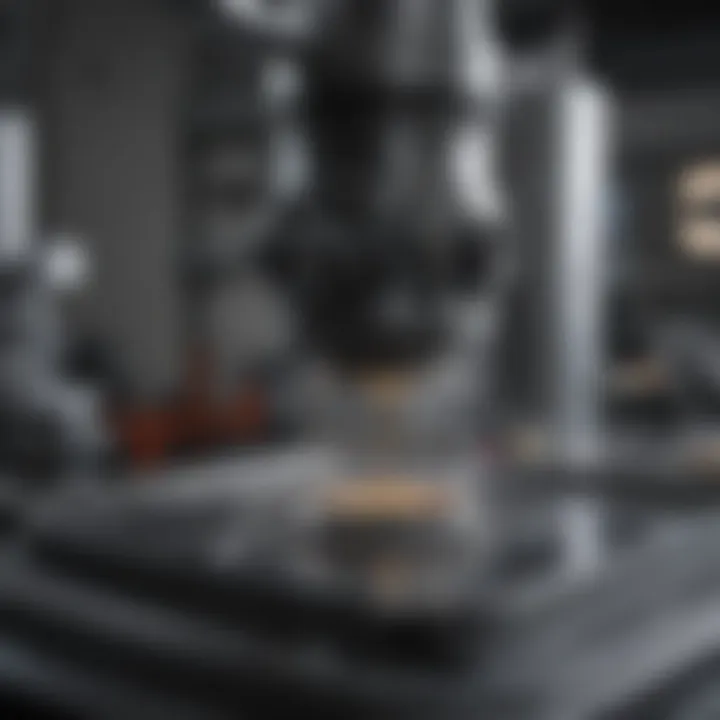
Intro
Aluminum vapor deposition plays a crucial role in many industries today, providing essential coatings and materials for a variety of applications. This technique enables the deposition of aluminum in a way that enhances the protective and functional properties of substrates. With advancements in technology, this method has been widely adopted, particularly in electronics, optics, and materials science.
In this article, we will explore various aspects of aluminum vapor deposition, including its fundamental principles, the necessary equipment required, and the detailed procedures involved. Understanding the advantages and limitations of this process helps to highlight its significance across different fields.
Key Findings
This section summarizes critical insights into aluminum vapor deposition, revealing its essential role in several applications.
Major Results
- Wide Applicability: Aluminum vapor deposition is used in electronics for creating reflective coatings on circuit boards, enhancing their performance. It also finds application in optics for mirror coatings in lasers.
- Process Efficiency: This method allows for uniform coatings over large areas with excellent adhesion. The efficiency of aluminum vapor deposition contributes to cost-effective manufacturing processes.
- Material Properties: Coatings created through this method exhibit properties such as high reflectivity, corrosion resistance, and low thermal conductivity, making them suitable for diverse applications.
Discussion of Findings
The findings indicate that the technique is versatile and efficient. The specific properties of aluminum make it an excellent choice for various coatings. These traits contribute to the robustness of devices in which they are used. Moreover, the continuous advancement in equipment and methodologies ensures that aluminum vapor deposition remains relevant and competitive in modern industrial applications.
Methodology
Understanding the methodology behind aluminum vapor deposition clarifies how it integrates into different processes.
Research Design
The research design for aluminum vapor deposition studies typically encompasses experimental setups that test the effectiveness of different deposition parameters. This includes variations in temperature, pressure, and substrate materials.
Data Collection Methods
Data is often collected through:
- Experimental Trials: Observation of coating results under various conditions.
- Analytical Techniques: Using methods such as spectrophotometry and electron microscopy to analyze the physical and chemical properties of the deposited layers.
"Aluminum vapor deposition not only improves material performance but also drives innovation in multiple fields such as renewable energy and aerospace."
Foreword to Aluminum Vapor Deposition
Aluminum vapor deposition is a key technique in various industrial fields, valued for its ability to create thin films of aluminum on a variety of surfaces. This process is significant not only for its applications in electronics, optics, and architecture, but also for its efficiency and adaptability. The growing demand for precise, functional coatings has solidified its importance in manufacturing and technology.
Definition and Overview
Aluminum vapor deposition refers to the process whereby aluminum is vaporized and then deposited onto a substrate. This can be accomplished through physical or chemical methods. During the process, aluminum atoms are transferred in a vacuum environment, allowing them to condense on the substrate surface. The initial step typically involves heating aluminum until it reaches a gaseous state. Once vaporized, these aluminum atoms settle uniformly on the target material, forming a thin layer. This process is essential in producing coatings with specific properties, including enhanced conductivity and resistance to corrosion.
Historical Context
The development of vapor deposition technology can be traced back to the mid-20th century. Initially, aluminum deposition methods were rudimentary, often resulting in uneven coatings. However, advancements in vacuum technology and materials science have drastically improved both the quality and efficiency of aluminum vapor deposition.
One of the first significant applications was in the production of mirrors made of aluminum, which quickly became known for their reflective properties. Over the decades, industries expanded the technique to electronics, where aluminum's properties complement semiconductors, ensuring efficient conductivity. With each innovation, the methods have evolved, leading to new applications across various sectors, indicating an ongoing transformation that closely aligns with technological progress.
Fundamentals of Vapor Deposition Techniques
Understanding vapor deposition techniques is crucial for anyone looking to dive into the intricacies of aluminum vapor deposition. These methods not only define the efficiency and effectiveness of the coating process but also determine the overall quality of the materials produced. This discussion elaborates on two primary techniques: Physical Vapor Deposition (PVD) and Chemical Vapor Deposition (CVD). Both techniques offer unique advantages and come with specific considerations that impact their application in various industries.
Physical Vapor Deposition (PVD)
PVD is a widely used vacuum coating technique. In this process, solid materials are vaporized in a vacuum environment. The vapor then condenses on the substrate, forming a thin film. This technique is characterized by several critical steps:
- Material Vaporization: The desired material, such as aluminum, is heated to a point where it transitions into a vapor state. This can be achieved through methods like thermal evaporation or sputtering.
- Transport of Vapor: Once vaporized, the particles travel through the vacuum space toward the substrate.
- Condensation and Film Formation: As the vapor comes in contact with the cooler surfaces of the substrate, it condenses, forming a uniform coating.
This method is particularly valued in various applications, including semiconductor manufacturing and optical devices, due to its ability to produce high-purity films with good adhesion and uniform thickness. However, PVD processes often require precise control of deposition parameters, such as substrate temperature and deposition rate, to achieve desired outcomes.
Chemical Vapor Deposition ()
CVD stands out by utilizing chemical reactions to produce thin films on substrates. In this process, gaseous precursors (reactants) react with each other on the substrate surface. Some key features of CVD include:
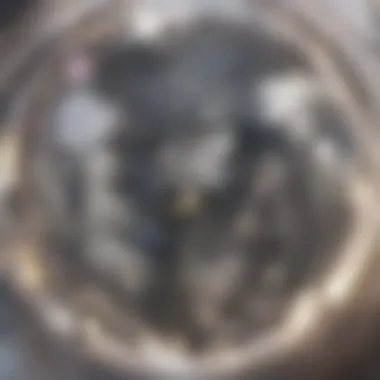
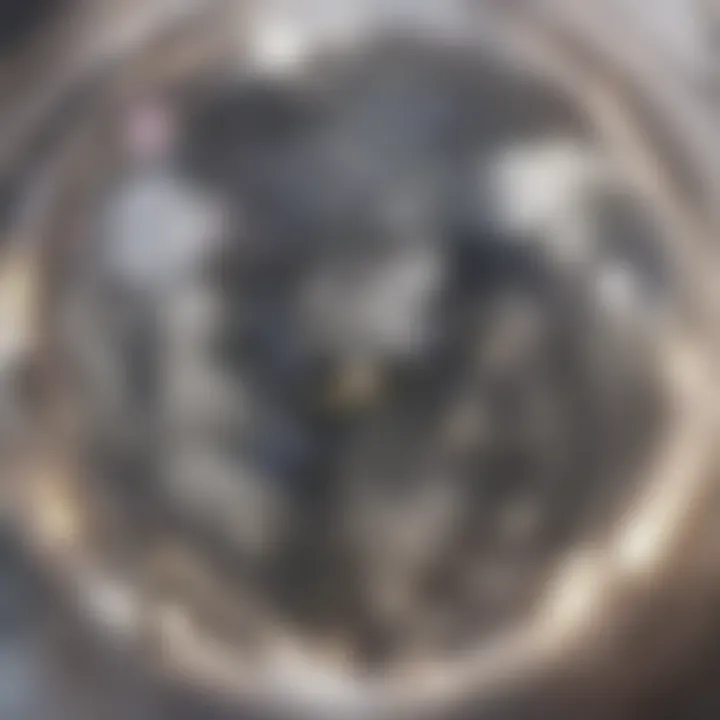
- Chemical Reactions: Unlike PVD, where the material is solely vaporized, CVD relies on chemical reactions to deposit materials. This can lead to better film quality and density.
- Temperature Control: The reactions typically take place at elevated temperatures, which can enhance the mobility of adatoms (atoms that migrate on a surface).
- Versatility: CVD is adaptable for a wide range of materials, making it suitable for applications across different fields, such as microelectronics and photovoltaic cells.
CVD also allows for better coating uniformity over complex geometries compared to PVD. However, managing the precursors and ensuring a consistent deposition can pose challenges.
Both PVD and CVD are instrumental in advancing technology within various sectors, highlighting the importance of mastering these techniques for successful outcomes in aluminum vapor deposition.
The Aluminum Vapor Deposition Process
The aluminum vapor deposition process plays a critical role in the broader context of material engineering. It encompasses two primary methods—physical vapor deposition and chemical vapor deposition—that are instrumental in producing aluminum coatings. Understanding the mechanics behind aluminum vapor deposition provides insight into its applications, advantages, and challenges. In this section, we will explore these details, highlighting the significance of this process in modern technology.
Mechanism of Deposition
Aluminum vapor deposition is characterized by a straightforward but effective mechanism. Essentially, it involves transforming aluminum into a vapor and subsequently depositing it onto a substrate. The vapor is commonly generated by heating aluminum to high temperatures, which allows it to evaporate and then condense on the desired surface. This creates a thin film of aluminum that adheres well to the substrate.
Factors such as temperature, pressure, and deposition time play crucial roles in determining the quality of the aluminum film. High temperatures generally increase the rate of deposition, but they can also affect the film's microstructure. If the deposition occurs in a vacuum environment, this can enhance the film's purity and adhesion properties. Control over these parameters is vital to achieving optimal results.
"The efficiency of aluminum vapor deposition hinges on precise control of both the process and materials involved."
Types of Aluminum Sources
When discussing aluminum deposition, the source of aluminum is significant. There are several types of aluminum sources that may be utilized, each with its unique characteristics. Commonly used sources include:
- Aluminum pellets: The simplest form, these are solid pieces of aluminum that can be easily melted and vaporized.
- Aluminum foil: This thin sheet can be employed for lower-volume applications and offers good vaporization properties.
- Aluminum wire: Sometimes used in wire-feed systems, allowing for continuous processing.
- Sputtering targets: In cases of advanced techniques like sputtering, specially prepared aluminum targets can be used to increase efficiency.
Choosing the appropriate aluminum source depends on various factors, including the desired film thickness, deposition rate, and the application requirements. By understanding these various sources, practitioners can optimize their processes to meet specific goals.
Equipment and Setup
The success of aluminum vapor deposition heavily relies on the right equipment and setup. Selecting suitable systems can influence deposition quality, efficiency, and scalability. Properly designed equipment enhances process control and reproducibility, crucial factors especially in industrial settings.
Vapor Deposition Systems
Vapor deposition systems are central to the aluminum deposition process. These systems generally fall into two categories: Physical Vapor Deposition (PVD) and Chemical Vapor Deposition (CVD). Each system has strengths that align with specific application needs.
PVD Systems: These systems utilize physical processes to vaporize aluminum, often involving thermal or electron beam evaporation. They operate in a vacuum environment, allowing for high purity deposits. PVD systems are commonly employed in electronic component manufacturing due to their ability to create thin, uniform layers directly on substrates like silicon or glass.
CVD Systems: In contrast, CVD systems involve chemical reactions to deposit aluminum on substrates. This method often results in superior conformality and can be used for more complex material structures. CVD is particularly valued in the semiconductor industry where precise control over film thickness is essential.
When selecting between PVD and CVD, a company must consider factors such as desired film characteristics, substrate type, and production volume. The integration of advanced technologies, like robotic handling systems, further enhances these setups by improving throughput and reducing contamination risks.
Control Systems and Parameters
Control systems are essential for monitoring and regulating the aluminum deposition process. Effective control ensures that the vaporization rate, temperature, and pressure are maintained within specified limits, thus fostering quality and uniformity.
Key Parameters:
- Temperature: Essential for controlling the rate of aluminum vapor generation. Too high temperatures can lead to unwanted reactions in the chamber, while too low can result in insufficient vaporization.
- Pressure: The operating pressure influences the mean free path of vapor particles, significantly affecting deposition rates and film morphology.
- Vapor Density: Monitoring the density of aluminum vapor is crucial for achieving desired film thickness. Real-time sensors can provide valuable data during the deposition process.
In a well-designed setup, the use of closed-loop control systems provides real-time data for making instant adjustments. This approach facilitates consistent output, thus minimizing defects. Sophisticated software can also simulate conditions before the actual deposition, allowing operators to predict outcomes and plan accordingly.
The importance of thoroughly understanding these elemental factors cannot be understated. By optimizing equipment and setup, manufacturers can enhance product quality, meet industry standards, and remain competitive in a rapidly evolving market.
Applications of Aluminum Vapor Deposition
The applications of aluminum vapor deposition are varied and significant. The technology plays a critical role in numerous industries. Understanding its practical uses provides insight into its relevance in manufacturing and technology. Each application harnesses the characteristics of aluminum deposition to meet specific needs.
In the following sections, we will explore the distinct areas where aluminum vapor deposition finds its application. The focus will be on the electronics industry, optical coatings, automotive applications, and architectural uses. Each of these applications illustrates the broad spectrum of benefits derived from this technology.
Electronics Industry
The electronics industry has embraced aluminum vapor deposition for its essential functionality. This process allows the creation of precise coatings that enhance electronic components.
Semiconductors
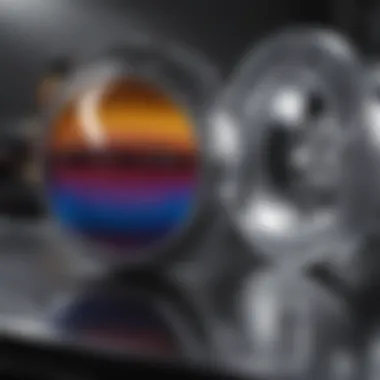
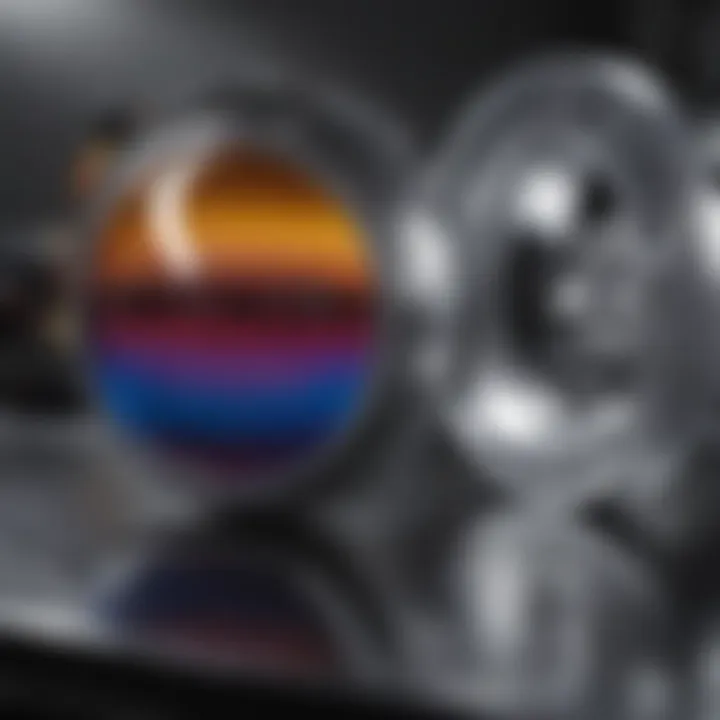
Semiconductors utilize aluminum vapor deposition to create thin layers crucial for electronic circuits. These layers are integral for efficient conductivity and performance. Aluminum’s conductive properties make it an ideal material for this application. One of the key characteristics is its ability to form uniform coatings. This uniformity is vital for maintaining the reliability of semiconductor devices. The deposition process supports the creation of intricate structures, which is essential for modern electronics.
This approach has significant advantages. It is cost-effective compared to other methods, and offers excellent adhesion to various substrates. However, there are also disadvantages, such as potential thermal instability in certain conditions.
Thin Films
Thin films are another critical application within the electronics realm. Aluminum vapor deposition forms these films with specific properties tailored for various uses. A thin film is often used in capacitors, resistors, and transistors.
A notable characteristic is the adaptability in thickness control. This aspect allows manufacturers to meet precise specifications easily. Thin films produced through vapor deposition exhibit good electrical characteristics. They can also reduce the size and weight of electronic devices while improving performance.
Yet, challenges arise from the thickness uniformity and potential defects in the film.
Optical Coatings
Optical coatings represent a significant field where aluminum vapor deposition shines. The need for specific optical properties makes this application crucial.
High Reflectivity Mirrors
High reflectivity mirrors are constructed using aluminum vapor deposition due to its excellent reflective qualities. These mirrors are vital in applications such as telescopes and lasers where efficiency is crucial.
The key characteristic of these mirrors is high reflectivity across a wide range of wavelengths. This property makes them an ideal choice for various optical systems. The unique feature of aluminum coatings allows mirrors to achieve reflectivities greater than 90%.
However, one disadvantage is susceptibility to oxidation, which requires protective overcoatings.
Antireflective Coatings
Antireflective coatings utilize aluminum vapor deposition to enhance optical performance by minimizing unwanted reflections. This application is vital for lenses, displays, and solar panels.
A primary benefit is improved transmission of light through surfaces, enhancing clarity and efficiency. The distinct feature here is the layers of different materials that reduce reflection at specific wavelengths.
Nonetheless, the main challenge is ensuring durability and resilience against environmental factors.
Automotive Applications
Aluminum vapor deposition is increasingly recognized in the automotive sector. This process improves the performance and sustainability of vehicle components.
The application in this domain allows for lightweight coatings that protect against corrosion. These characteristics help enhance vehicle longevity and performance. Besides, it allows for the production of aesthetically appealing surfaces, giving a modern look to vehicles. However, the challenge lies in balancing performance with cost-efficiency in this highly competitive industry.
Architectural Applications
Aluminum vapor deposition is also applied in architecture, particularly for facades and interior designs. This process contributes to the durability and aesthetic appeal of buildings.
The ability to coat surfaces with aluminum improves weather resistance. It also allows for various finishes that reflect light and color beautifully. This can impact energy efficiency positively through improved insulation and shielding from UV rays. Yet, one must consider the installation costs and maintenance of these coated surfaces.
Overall, the applications of aluminum vapor deposition span multiple industries. Each application highlights unique benefits while also facing specific challenges and considerations.
Advantages of Aluminum Vapor Deposition
Aluminum vapor deposition is a widely utilized technique in many industries due to its distinct advantages. Understanding these benefits is critical for researchers and practitioners who are involved in material science and engineering. The following sections will address the cost-effectiveness of this deposition technique and its environmental impact.
Cost-effectiveness
Cost is a major factor in any manufacturing process, and aluminum vapor deposition offers notable economic benefits. This technique allows for the production of thin films and coatings with relatively low material waste. Compared to alternatives like electroplating or bulk coating methods, the vapor deposition process minimizes excess use of aluminum, leading to decreased expenses for materials.
Moreover, the speed of deposition can contribute to lower operational costs. The process is often quicker than traditional techniques, enabling higher throughput in manufacturing. This efficiency results in reduced labor costs over time, as workers can focus on additional tasks rather than monitoring lengthy coating processes.
Another aspect of cost-effectiveness is the versatility of aluminum coatings. Due to their properties, the applications span from electronics to architectural finishes, expanding the market potential. Industries can benefit from a single process to meet various coating needs, further consolidating material costs and minimizing the need for multiple systems.
In summary, aluminum vapor deposition is a cost-effective solution that supports various applications while delivering material savings and enhancing production efficiency.
Environmental Impact
In today’s industrial landscape, the environmental impact of manufacturing processes is under scrutiny. Aluminum vapor deposition presents several advantages in this area. First, the technique generally produces fewer pollutants compared to alternatives like chemical baths in electroplating. The process uses fewer hazardous substances, resulting in a cleaner working environment.
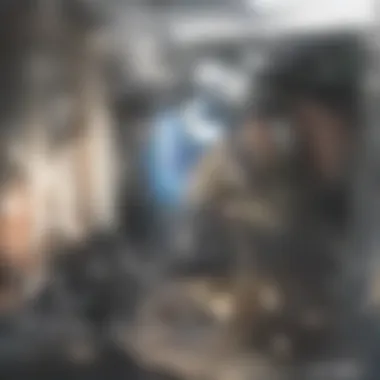
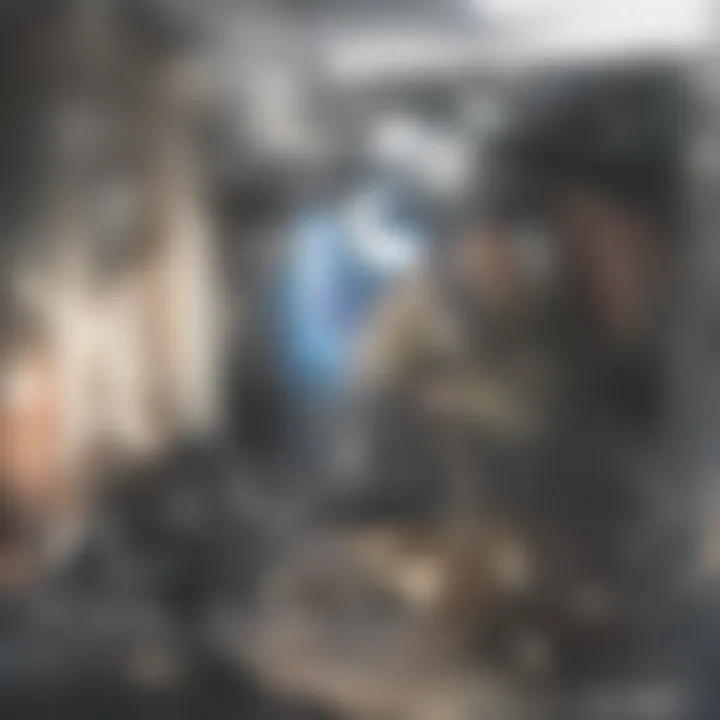
Additionally, the high efficiency of aluminum vapor deposition means that less energy is consumed in applying coatings. Since the process often requires lower temperatures than many thermal spray methods, it decreases energy usage overall. This can have a significant positive effect on reducing the carbon footprint associated with manufacturing.
Another consideration is the recyclability of aluminum coatings. Aluminum itself is a valuable resource that can be reclaimed from waste materials without significant degradation of quality. Thus, the use of aluminum vapor deposition not only supports sustainable practices but also aligns with the principles of circular economy.
Limitations and Challenges
Understanding the limitations and challenges of aluminum vapor deposition is essential for those seeking to employ this technique effectively. While aluminum vapor deposition presents various benefits, it is not without its drawbacks. The importance of examining these constraints lies in informed decision-making, ensuring that researchers and engineers can optimize their processes while navigating potential pitfalls.
Material Limitations
One notable material limitation involves the compatibility of aluminum with certain substrates. Not all materials support the adhesion of aluminum vapor deposits effectively. For instance, if the substrate lacks the necessary surface energy or chemical reactivity, aluminum films may delaminate, leading to performance issues.
Additionally, thin films produced through vapor deposition can exhibit vulnerabilities, such as increased susceptibility to oxidation. When aluminum films are exposed to moisture or oxygen, they can corrode, compromising their integrity and performance. Careful material selection is therefore paramount to ensure optimal outcomes.
Furthermore, the inherent properties of aluminum itself can contribute to limitations. For example, while aluminum has excellent conductivity, it may not suffice in high-temperature applications where other materials might perform better. Recognizing these limitations helps researchers tailor their approaches appropriately.
Technical Challenges
The technical challenges associated with aluminum vapor deposition can vary significantly based on the specific application and settings used. One primary issue is achieving uniform film thickness across different substrates. Variations in temperature during the deposition process often result in non-uniformity, affecting the performance of the deposited layers. Control over environmental conditions is essential to mitigate this problem.
Process monitoring also poses challenges, as real-time adjustments during deposition may be difficult to implement. Traditional monitoring techniques might lack the accuracy required to ensure consistent deposition quality. As a result, the need for advanced control systems becomes evident, requiring additional investments in technology and training.
Moreover, scaling the aluminum vapor deposition process for industrial applications presents its own complexities. Equipment designed for laboratory settings may not translate seamlessly to larger-scale manufacturing. Engineers must address these scaling issues while maintaining quality, reliability, and cost-effectiveness.
"Acknowledging the limitations and challenges of aluminum vapor deposition is crucial for optimizing outcomes and ensuring the success of various applications."
In summary, both material limitations and technical challenges play a significant role in the effectiveness of aluminum vapor deposition. Understanding these factors aids in developing strategies that enhance the technique while mitigating potential risks.
Future Trends in Vapor Deposition Technology
The landscape of vapor deposition technology continues to evolve rapidly. Understanding future trends is crucial for staying competitive in industries where aluminum vapor deposition is a key process. As technology advances, we see innovations that not only improve efficiency but also enhance the quality of deposited materials. Integration of automation and artificial intelligence, for instance, is changing the way companies approach deposition processes.
A major focus lies in developing more precise equipment that allows for better control over various parameters during the deposition process. This precision translates to better coatings and thinner films that have enhanced functionality.
Innovations in Equipment
In the realm of vapor deposition, equipment innovation plays a critical role. Advanced systems now incorporate features such as real-time monitoring and feedback mechanisms. These features help in adjusting variables on-the-fly to achieve desired outcomes.
Some of the latest equipment trends include:
- Fully Automated Systems: The move towards automation simplifies workflow, allowing operators to manage multiple processes concurrently. This leads to increased productivity and reduced labor costs.
- Higher Throughput: By optimizing vacuum generation and material handling, new equipment designs facilitate faster deposition. This is particularly important for industries that operate on tight production schedules.
- Enhanced Material Compatibility: Modern deposition systems are often designed to handle a variety of substrates. This versatility expands the potential applications of aluminum vapor deposition.
Emerging Materials
As industries demand more advanced coatings, the exploration of emerging materials becomes vital. New materials can offer better performance metrics compared to traditional aluminum. These advancements include:
- Nano-coatings: These coatings provide superior strength and weight reduction, essential for applications such as aerospace and automotive industries.
- Hybrid Coatings: By combining aluminum with other materials, hybrid coatings can achieve unique properties, such as increased corrosion resistance or enhanced electrical conductivity.
Emerging research in this area shows promise in not just enhancing product performance but also reducing environmental impacts. By using alternative materials and processes, the industry can work towards more sustainable practices.
Future advancements in aluminum vapor deposition technology are set to redefine standards, pushing the boundaries of what is possible in material engineering.
Ending
The exploration of aluminum vapor deposition reveals its extensive relevance and applications across various industries. The conclusion of this article summarizes the vital aspects discussed and emphasizes the significance of understanding this technology in detail. Aluminum vapor deposition plays a crucial role in enhancing the performance and functionality of numerous products and systems, which means insights into the process are beneficial for researchers, students, and professionals alike.
Summary of Key Points
Aluminum vapor deposition is not just a means of applying a thin aluminum layer; it is an intricate process that demands knowledge of both theoretical and practical aspects. Key points from this article include:
- Understanding the Techniques: The differentiation between Physical Vapor Deposition (PVD) and Chemical Vapor Deposition (CVD) reveals how each method affects the final properties of the aluminum coating.
- Equipment Necessities: Knowing the types of vapor deposition systems and their specific components is essential for successful application in various scenarios.
- Applications Across Industries: From electronics to automotive, aluminum vapor deposition serves practical purposes that enhance product capabilities.
- Advantages and Limitations: Recognizing the cost-effectiveness and environmental impact alongside the challenges faced promotes informed decision-making in industry practices.
- Future Trends: Awareness of emerging technologies and innovative equipment will help steer developments in the field, offering exciting possibilities for future applications.
Final Thoughts on the Impact
The impact of aluminum vapor deposition cannot be overstated. It not only contributes to advancements within industries but also has the potential to foster significant improvements in product durability and functionality. As technology evolves, so do the applications and techniques of aluminum vapor deposition, presenting fresh opportunities for research and implementation. Continued study and innovation in this field hold promise for enhanced efficiency and sustainability.
In summary, understanding aluminum vapor deposition is integral to appreciating its role in contemporary engineering and manufacturing. The insights provided in this article will serve as a valuable resource for anyone engaged in relevant fields.
"Aluminum vapor deposition is not merely a process; it is a gateway to innovation in material engineering."